To kategooria:
Freesitööd
Ratsionaalsete freesimisrežiimide valik
Ratsionaalse freesimisrežiimi valimine sellel masinal tähendab, et antud töötlemistingimuste jaoks (tooriku materjal ja mark, selle profiil ja mõõtmed, töötlemisvaru) on vaja valida optimaalne lõikuri tüüp ja suurus, materjali klass. ja lõikuri lõikeosa, määrde- ja jahutusvedeliku geomeetrilised parameetrid ning määrake järgmiste lõikerežiimi parameetrite optimaalsed väärtused: B, t, sz. v, n, Ne, Tm.
Valemist (32) järeldub, et parameetritel B, t, sz ja v on freesimise mahulisele tootlikkusele sama mõju, kuna igaüks neist siseneb valemisse esimeses astmes. See tähendab, et kui ükskõik milline neist suureneb, näiteks kaks korda (kui muud parameetrid ei muutu), suureneb ka mahuline tootlikkus kaks korda. Need parameetrid ei mõjuta aga tööriista kasutusiga samaväärselt (vt § 58). Seetõttu on tööriista kasutusiga arvestades soodsam valida esmalt nende parameetrite maksimaalsed lubatud väärtused, millel on tööriista elueale vähem mõju, st järgmises järjestuses: lõikesügavus, ettenihe hamba kohta ja lõikekiirus. Seetõttu tuleks selle masina freesimise ajal nende lõikerežiimide parameetrite valimist alustada samas järjestuses, nimelt:
1. Lõikesügavus määratakse sõltuvalt töötlusvarust, pinnakareduse nõuetest ja masina võimsusest. Töötlemise varu on soovitav eemaldada ühe käiguga, võttes arvesse masina võimsust. Tavaliselt ei ületa töötlemata freesimise lõikesügavus 4-5 mm. Esipinnaga töötlemata freesimiseks karbiidist lõikurid(pead) võimsatel freespinkidel võib see ulatuda 20-25 mm või rohkem. Freesimise lõpetamisel ei ületa lõikesügavus 1-2 mm.
2. Määratakse maksimaalne lubatud sööt vastavalt töötlemistingimustele. Maksimaalsete lubatud ettenihkete määramisel tuleks kasutada ettenihkeid hamba kohta, mis on lähedased "murdmistele".
Viimane valem väljendab ettenihke sõltuvust hamba kohta freesimissügavusest ja lõikuri läbimõõdust. Maksimaalse lõikepaksuse väärtus ehk konstantse koefitsiendi I c väärtus valemis (21) sõltub töödeldava materjali füüsikalistest ja mehaanilistest omadustest \ (teatud tüüpi ja lõikuri konstruktsiooni puhul). Maksimaalse lubatud sööda väärtused on j piiratud erinevate teguritega:
a) karestamise ajal - tööriista jäikus ja vibratsioonikindlus (masina piisava jäikuse ja vibratsioonikindlusega), töödeldava detaili jäikus ja tööriista lõikeosa tugevus, näiteks lõikehammas, ebapiisav maht laastude soonte jaoks, näiteks ketaslõikurite jms jaoks. Niisiis valitakse terase töötlemata freesimisel sisestusnugade ja suure hambaga silindriliste lõikuritega etteanne hamba kohta vahemikus 0,1-0,4 mm / hammas ning malmi töötlemisel kuni 0,5 mm / hammas;
b) viimistlemisel - pinna karedus, mõõtmete täpsus, pinnakihi olek jne. Terase ja malmi freesimisel määratakse suhteliselt väike etteanne ühe lõikuri hamba kohta (0,05-0,12 mm / hammas).
3. Määratakse lõikekiirus; nagu ta kõige rohkem teeb suur mõju tööriista vastupidavuse põhjal, siis valitakse see selle tööriista jaoks vastuvõetud vastupidavusstandardi alusel. Lõikekiirus määratakse valemiga (42) või lõiketingimuste standardite tabelite järgi, olenevalt freesimise sügavusest ja laiusest, ettenihkest hamba kohta, lõikuri läbimõõdust, hammaste arvust, jahutustingimustest jne.
4. Efektiivne lõikevõimsus Ne määratakse valitud režiimis vastavalt standarditabelitele või valemile (39a) ja võrreldakse masina võimsusega.
5. Autor määra kiirus lõikamine (u või i ^) määratakse masina spindli pöörlemissageduse lähim samm sellel masinal saadaolevate hulgast vastavalt valemile (2) või graafikule (joonis 174). Tehke punktist, mis vastab aktsepteeritud lõikekiirusele (näiteks 42 m / min). horisontaaljoon, ja punktist, millel on valitud lõikuri läbimõõdu märk (näiteks 110 mm) - vertikaalne. Nende joonte lõikepunktis määratakse spindli kiiruse lähim samm. Niisiis, joonisel fig. 172, freesimisel D = 110 mm läbimõõduga lõikuriga lõikekiirusel 42 m/min on spindli kiirus 125 p/min.
Joon.174 Freesi kiiruse nomogramm
6. Minutiline sööt määratakse valemiga (4) või ajakava järgi (joonis 175). Niisiis, freesimisel lõikuriga D = 110 mm, z = 10, kui sz = 0,2 mm/hammas ja n = 125 pööret minutis, määratakse minutine etteanne vastavalt graafikule järgmiselt. Punktist, mis vastab ettenihkele hamba kohta sg = 0,2 mm / hammas, joonistame vertikaalne joon kuni see lõikub kaldjoonega, mis vastab lõikuri hammaste arvule r = 10. Saadud punktist tõmbame horisontaalset joont, kuni see lõikub kaldjoonega, mis vastab aktsepteeritud spindli kiirusele l = 125 pööret minutis. Järgmisena tõmmake saadud punktist vertikaalne joon. Selle joone lõikepunkt sellel masinal saadaolevate madalamate minutivoogude skaalaga määrab lähima minutisööte astme.
7. Määratakse masina aeg.
masina aeg. Aega, mille jooksul laastude eemaldamise protsess toimub ilma töötaja otsese osaluseta, nimetatakse masinaajaks (näiteks tooriku tasapinna freesimiseks mehaanilise pikisuunalise etteande sisselülitamise hetkest kuni selle väljalülitamiseni).
Riis. 1. Minutisööda nomogramm
Tootlikkuse kasvu metalli lõikamismasinatel töötlemisel piiravad kaks peamist tegurit: masina tootmisvõimalused ja tööriista lõikeomadused. Kui masina tootmisvõimalused on väikesed ja ei võimalda tööriista lõikeomadusi täiel määral ära kasutada, siis on sellise masina tootlikkus vaid murdosa võimalikust tootlikkusest tööriista maksimaalse kasutamise juures. Juhul, kui masina tootmisvõimsused ületavad oluliselt tööriista lõikeomadusi, on selle tööriistaga võimalik saavutada masinal maksimaalne võimalik tootlikkus, kuid masina võimalused, st masina võimsus, maksimaalne. ei kasutata täielikult ära lubatud lõikejõude jne. e. Masina ja tööriista tootlikkuse ja kasutamise ökonoomsuse seisukohalt on optimaalsed juhud, kui masina tootmisvõimsus ja tööriista lõikeomadused sobivad või on üksteisega lähedased.
See tingimus on aluseks nn tööpinkide tootmiskarakteristikutele, mille pakkus välja ja töötas välja prof. A. I. Kaširin. Masina tootmiskarakteristikuks on masina ja tööriista võimaluste vaheliste sõltuvuste graafik. Tootmisomadused muudavad optimaalsete lõiketingimuste määramise antud masinal töötlemisel lihtsamaks ja lihtsamaks.
Konkreetse tööriista lõikeomadusi iseloomustavad töötlemise ajal lubatud lõiketingimused. Lõikekiirust antud töötlemistingimustes saab määrata valemiga (42, a). Praktikas leitakse see lõiketingimuste tabeli järgi, mis on toodud hindaja või tehnoloogi teatmeteostes. Siiski tuleb märkida, et nii freesimise kui ka muude töötlemisviiside lõiketingimuste standardid töötatakse välja tööriista lõikeomadustest lähtuvalt. erinevatel puhkudel töötlemine (tööriista tüüp ja suurus, lõikeosa materjali tüüp ja mark, töödeldav materjal jne) ning need ei ole seotud masinatega, millel töötlemine toimub. Kuna erinevate masinate tootmisvõimalused on erinevad, on praktiliselt teostatav optimaalne töötlemisrežiim erinevatel masinatel samade töötlemistingimuste puhul erinev. Tööpinkide tootmisvõimalused sõltuvad eelkõige masina efektiivsest võimsusest, kiirusest, ettenihkest jne.
Riis. 2. Sukeldumine ja ülesõit
Freeside tootmiskarakteristikud raskete lõikuritega lõikamiseks töötasid välja prof A. I. Kashirin ja autor.
Otsfreesidega töötamiseks mõeldud freespinkide tootmiskarakteristikute (nomogrammide) konstrueerimise põhimõte põhineb liitekohal. graafiline lahendus kaks võrrandit, mis iseloomustavad ühelt poolt lõikekiiruse vT sõltuvust valemiga (42) juures -Bz' = const ja teiselt poolt lõikekiiruse id„ masina lubatud võimsusega. Lõikekiirust vN saab määrata valemist
Riis. 3. Konsoolfreespingi 6P13 tootmisomadused
Lõikamise tingimused
Vasaku käega lõikurid
Miks on sööda vastu jahvatamine parem.Probleem: 2-käivitusega lõikur sulatab PVC vahu.
Lahendus: vali väiksem pöörete arv või freesi ühe keermega lõikuriga. (Pilt)
1. Keelekümblus:
Lõikur peab suutma otspinnast materjali sisse tungida (puurimisfunktsioon).
2. Lõikeserv:
Reeglina erinevad läbipääsu servad üksteisest. Liikumise vastaspool on "ilusam" kui sünkroonsuse pool. See on eriti ilmne 1-käivitusega lõikuri kasutamisel, samuti alumiiniumi freesimisel.
Nõuanne; Freesi sisekontuure päripäeva, välimisi vastupäeva. Seega on "halb" pool laastudes
3. Kiibi eemaldamine:
Laastud tuleb kiiresti evakueerida, et lõikurite õõnsused ei täituks ja selle tulemusena ei puruneks lõikur. Mida sügavamal ja kiiremini toimub freesimine, seda keerulisem on laastude eemaldamine. Juhised: Ärge freesige sügavamalt kui kahe- või kolmekordne lõikuri läbimõõt. Mine sügavamatesse soontesse mitme käiguga. Polüstüreeni ja muude plastide freesimisel on parema väljundi saavutamiseks otstarbekas kasutada poleeritud flöötidega lõikureid.
4. Soojuse hajumine/määrimine:
Lõikur ei tohiks liiga kuumaks minna: Ühelt poolt kaotab tööriist oma omadused liiga kõrgel temperatuuril, teisalt, veelgi kriitilisem, võivad plast- ja alumiiniumlaastud soontesse "kleepuda", takistades laastude sattumist. eemaldatakse ja selle tulemusena võib lõikur puruneda. Metallide töötlemisel on hädavajalik soovitada määrdeainet. Märkus: alumiiniumi ja värvilisi metalle saab jahvatada alkoholi või spetsiaalsete emulsioonidega ning pleksiklaasi jaoks võib kasutada seebivet.
5. Purunemise oht:
kasvab lineaarselt etteandekiiruse suurenemisega ja keelekümblussügavuse suurenemisega: topeltsööt tähendab kahekordset osariski, kahekordne keelekümblussügavus tähendab kaheksa korda suuremat osariski.
Juhised:
Parem on freesida mitme käiguga vähem sügavalt ja suurema ettenihkega. Kasutage võimalikult lühikese lõikepikkusega lõikurit. Pingutage seda nii palju kui võimalik. Üldreegel: surutud padrunisse (padrunitang) kolmandiku üldpikkus lõikurid.
Õige lõige toob laastud üles.
Õige lõigatud lõikur hõlbustab laastude eemaldamist, mis on hea pidevaks väljastamiseks, kuid selle puuduseks on see, et lõikur liigutab nagu korgitser ka alusmaterjali (toorikut) üles, "mohr" puidu freesimisel või " urgu" õhukese lehtmaterjali töötlemisel (näiteks žestid). Vasaku spiraaliga lõikur seevastu surub materjali alla ja kiudmaterjalide nagu puit või papp lõikamisel saavutate siledama ülemise serva (kiud ei tõuse, vaid "pressitakse" alusmaterjali sisse ). Kuid siin on negatiivne tegur kiibi eemaldamise raskus.
Märge:
Tavalistel juhtudel kasutage parempoolset lõikurit.
Vasakpoolsed lõikurid on kasulikud madalate sisselõigete jaoks õhukesed materjalid, kus õige lõikega tooriku "kaevamise" ja ülestõmbumise oht on suur. Mida kõvemat materjali aga kasutad, seda kiiremini saad vasakpoolsest spiraalilõikurist lahti.
A. Parem lõige (tavaline vorm):
Tõmmake nöör üles. Lõikuril on kalduvus alusmaterjali "urguda" ja tõsta.
"korgitseri efekt".
B. Vasak spiraal (spetsiaalne kuju): ajab laastud maha, kui need on vastamisi või kasutatakse juba freesitud õõnsuses töötamisel. Lõikur vajutab alusmaterjalile ("korgitseri efekti" vastand).
Ei sobi sügavfreesimiseks.
Lõikuri tüüp: 1 või 2 tera?
Lõikureid on lõpmatu arv, kuid sisuliselt teeme vahet teravatel ja nüridel. Mida teravam on tera, seda kiiremini ots kulub.Üldreegel: mida suurem on materjali tugevus, seda lamedam peaks teritus olema tera juures. See teritus sobib kõvade metallide (nt messing) jaoks. Teravam kalasaba teritus plastikule, puidule ja pehmele alumiiniumile. Terad on lõikuri väga kuluvad osad. Rohkem kui ühe teraga lõikuritel jaotub koormus ja pikeneb tööriista tööiga. Need lõikurid töötavad kiiremini, vibreerivad vähem rasketes materjalides, nagu roostevaba teras. Mitme teraga – samadel freesimistingimustel – on laastud õhemad, mille tulemuseks on lõppkokkuvõttes siledam pind.
"Ideaalse" lõikuri tüübi valik sõltub alati töödeldavast materjalist:
"Pehmete" materjalide freesimisel: pehmed plastid (PVC, pleksiklaas, vaht), puitmaterjalid (puit, puitkiudplaat, vineer, puitlaastplaat), pehme alumiinium ja sandwich-materjalid (alumiinium/plast) saavad kasu teravatest 1-käivituslõikuritest. Kuna siin on kiirema nüristamise probleem eelistatavam kui ummistumise ja lõikuri purunemise oht.
Kõvade plastide jaoks sobiv terav 2-suunaline, kalasabaprofiiliga.
Kõvemate metallide töötlemisel nagu messing, võib soovitada tasase pinnasega 2-käivituslõikureid.
Eriti kõva konstruktsiooniterase freesimisel või väga kvaliteetsest terasest, kasutage kolme või nelja pliilõikurit.
Üksikkäivituslõikur
Üks nuga jätab suure vaba ruumi
kiibi eemaldamiseks
Kolmekäivitusega lõikur ristlõikega
Kolm tera vähendavad oluliselt ruumi
kiibi eemaldamiseks
Lõikuri ja graveerija erinevus
Paljud inimesed kasutavad mõisteid "lõikur" ja "graveerija" sünonüümidena. Siiski räägime kahest erinevast tööriistast.
Graveerija on lihtne tööriist, pooleks jagatud silinder, millele järgneb tagasilihvimine.
Kuju võib olla erinev; levinumad on kolmnurksed. Erinevalt freesidest ei ole neil spiraalset laasturenni.
Tööriista materjal: HSS või karbiid?
Reklaamitehnoloogias kasutatakse valdavalt karbiidist lõikurid.
Karbiid (HM) on kallis kunstlik toode, mis on aglomeeritud peenest pulbrist (nt Wolfram-Carbid). Aglomeratsiooniprotsessi käigus tekib lõikuri kuju kohe ja see ei muutu hiljem (seda ainult teritatakse). Karbiid on äärmiselt kõva ja kulumiskindel, kuid vastuvõtlik vibratsioonile ja põrutustele. HM lõikurite kasutamisel on oluline stabiilne, võimalik, et raskem ja massiivsem masin, täpse pöörlemisega spindel ja kvaliteetsed kinnitustangid. Freesitav materjal peab olema kindlalt ja kindlalt masinale kinnitatud.
Kiirterast (HSS) kasutatakse eelkõige seal, kus karbiid on liiga tundlik: roostevaba terase freesimisel, võnkuvatel masinatel või juhtudel, kui kinnituse jäikus ei ole piisavalt tagatud. HSS kulub palju kiiremini, kuid selle sitkuse tõttu on enneaegse rikke oht väiksem.
HSS-kattega lõikurite eluiga pikeneb oluliselt. Näiteks titaannitriidi (TiN) kasutusiga pikeneb kuus korda.
Titan-Nitrid on oluliselt jäigem kui HSS ja ka sitkem kui HM. Titan-Nitrid kattega peavad HM tööriistad ka kauem vastu, kuigi kõvaduse erinevus on tühine.
Veelgi olulisem on see, et katvus kajastub pöörete arvus ja etteandes. Sel viisil saab töötlemisaega pikendada ja lühendada. Alumiiniumi freesimisel hoiab TiN ära alumiiniumi hirmuäratava küpsemise lõikuris. Kate toimib nagu teflon pannil (laastud libisevad)
Kiirus ja optimaalne söötmine
Freesimisel on olulisemad parameetrid pöörete arv ja ettenihe. Tabeli andmed vastavad enamiku lõikuritootjate soovitustele. (Kahtluse korral küsige tarnijalt, milliseid režiime nad oma toote jaoks soovitavad).Esmalt võtke töödeldava materjali jaoks soovitatav lõikekiirus ja rakendage see pöörete arvu arvutamise valemis.
Kui kasutatakse masinat, mis ei ole väga jäik, määratakse pöörete arv ülemises piirkonnas ja etteanne alumises piirkonnas. Kui pöörete arv on teada, arvutatakse etteanne valemi abil.
Põhimõtteliselt arvestatakse: Mida suurem on lõikekiirus (vc = p * d * n), seda siledam on pind. Kuid lõikekiiruse suurenedes suureneb ka lõikuri nürisus.
Arvutusprotseduur:
1. Pöörete arv n:
Valige lõikekiirus vc laualt. (Kui materjali lõikekiirus on väga erinev, kontrollige juhendeid).
Andmete põhjal arvutage spindli pöörete arv
N = (vc *1000) / (3,14 * d)
F = n*fz*z
fz = sööt 1 hamba kohta
z = labade arv
Näide:
Soovite freesida kõva alumiiniumi, 3 mm läbimõõduga 2-käivitusega lõikuriga. Tabelist leiate: vc = 100...200 m/min. Selle põhjal arvutate:Max pöörete arv: n = (200 * 1000) / (3,14 * 3) = 200 000 / 9,42 = 21,230 U/min
Vastav sööt: f = 21230 * 0,04 * 2 = 1698 mm/minSuured etteandekiirused – eriti metallide puhul – nõuavad stabiilset ja vaikset masinat. Lisaks ei tohiks soone sügavus olla liiga suur (umbes 1 * d 1).
Vähem stabiilsete või suurema freesimissügavusega masinate puhul arvutatakse režiim järgmiselt:Max kiirus:
n = (200 * 1000) / (3,14 * 3) = 200 000 / 9,42 = 21,230 U/min(nagu eespool)
Min. pöörete arv: n = (100 * 1000) / (3,14 * 3) = 100 000 / 9,42 = 10,615 U/min
Vastav voog (minimaalne): f = 10615 * 0,04 * 2 = 849 mm/minKombineerite n=21230 U/min ja f=849 mm/min.
Vastuliikumine ja sünkroniseeritud liikumine
Kuidas luuakse lõike erinevad servad:Tera siseneb tuulepoolsest küljest materjali sisse. Liikumisjuhtimisalal jookseb lõikur vastu materjali. Kiibi paksus on materjali söötmise aluses pidevalt suurem. Sünkroonpiirkonnas jookseb lõikur koos materjaliga, laastu paksust vähendatakse väljumiseks. Varjutatud ala näitab laastu suhtelist paksust igas laastudes pöörde kohta. Vastuliikumises olev tera "võtab" materjali pidevalt, samas kui sünkroonse liikumise korral võetakse vaid väike kogus vahetult enne tera õhku väljumist. Seetõttu viimane tükk sageli justkui "lahti lööb". See on põhjus, miks liikumise vastaskülg on alati sujuvam kui sünkroonne pool.
Milline lõikur millise materjali jaoks | 1-juhe | 2-juhtmeline | 3-suunaline | |||
karm | puhtalt | karm | puhtalt | karm | puhtalt | |
puitmaterjalid | ||||||
Okaspuu (mänd) | ++ | 0 | +(+) | 0 | 0 | - |
Massiivne (tamm, pöök), vineer, MDF | +(+) | 0 | ++ | 0 | +(-) | - |
plastid | ||||||
PVC, polüstüreen, teflon, vaht | ++ | + | + | 0 | - | -- |
Duroplast, materjalid bakeliidiga (puitlaastplaat) | + | + | ++ | + | + | - |
Valatud pleksiklaas | ++ | + | +(+) | - | 0 | - |
Metallid | ||||||
Pehme alumiinium (Alucobond) | ++ | + | + | 0 | - | -- |
Jäik alumiinium (Floxal) | 0 | + | + | ++ | 0 | + |
Messing, pronks, vasesulamid | -- | - | 0 | +(-) | + | ++ |
Konstruktsiooniterasest | -- | -- | - | + | - | ++ |
kõrge kvaliteediga teras | -- | -- | -- | - | -- | + |
++ Väga hea + Hea 0 Rahuldav |
- Halvasti -- Ei sobi |
Kõvade terase klasside töötlemisel kasutatakse 4 või enamat tera.
Osaline või täielik kasutamine seda materjali ainult kokkuleppel ja kohustusliku viitega allikale
Ettevõtetes, kuhu kuuluvad toorikute pinnatöötlusega tegelevad allüksused, alusel normatiivdokumendid koostatakse spetsiaalsed kaardid, mis juhendavad operaatorit konkreetse detaili valmistamisel. Kuigi mõnel juhul (näiteks uued seadmed, tööriistad) peab freesioperaator tehnoloogiliste toimingute nüansse ise kindlaks määrama. Kui kodus käiakse väikese võimsusega masinat, siis seda enam, et ametlikke näpunäiteid reeglina käepärast pole.
See artikkel aitab mitte ainult mõista freesimise ajal lõikerežiimi arvutamise aluseid ja sobiva tööriista valimist, vaid ka praktilisi nõuandeid, millest piisab osade töötlemiseks leibkonna tasandil.
Neile, kes rohkem metallidega seotud, freesimise nüanssidega üksikasjalikumaks tutvumiseks peaksite tutvuma õpikuga "Metallilõikemasinad" - 2003, Cherpakov B.I., Alperovich T.A. Lõiketingimuste arvutamise protseduur on hästi kirjeldatud ka erinevates juhendites. Näiteks sisse juhised aastast 2000 (MGAU - Kolokatov A.M., Bagramov L.G.).
Freesimise omapäraks on see, et lõikeservad puutuvad materjaliga vahetult kokku vaid perioodiliselt. Selle tulemusena - vibratsioon, löökkoormused ja lõikurite suurenenud kulumine. Kõige tõhusamaks peetakse seda režiimi, mille puhul on optimaalselt kombineeritud järgmised parameetrid - sügavus, etteanne ja lõikekiirus, ilma et see kahjustaks töötlemise täpsust ja kvaliteeti. See võimaldab oluliselt vähendada tehnoloogilise operatsiooni maksumust ja tõsta tootlikkust.
Kõiki freesimise nüansse on võimatu ette näha. Töödeldavad toorikud erinevad struktuuri, mõõtmete ja kuju poolest; lõikeriistad - nende geomeetria, konstruktsiooni, kaitsekihi olemasolu / puudumise jne järgi. Kõike, mis on allpool lõiketingimuste osas välja toodud, tuleks võtta ainult juhisena. Konkreetsete freesimisparameetrite selgitamiseks peaksite kasutama spetsiaalseid tabeleid ja viiteandmeid.
Tööriista valik
See viitab peamiselt selle läbimõõdule. Mis on selle parameetri jaoks lõikuri () valimise omadus?
- Läbimõõdu suurendamine suurendab automaatselt tööriista maksumust.
- Kahe indikaatori vastastikune sõltuvus - kui etteanne suureneb, siis lõikekiirus langeb, kuna seda piirab tooriku struktuur (vt allpool).
Lõikuri optimaalne läbimõõt loetakse selliseks, et selle väärtus vastab (või veidi rohkem) vajalikule lõikesügavusele. Mõnel juhul saab ühe käiguga valida paksemad laastud, kuid see kehtib ainult materjalide kohta, mida iseloomustab madal tihedus. Näiteks polüstüreen või mõned puiduliigid.
Lõikekiirus
Sõltuvalt proovi materjalist saate keskenduda järgmistele näitajatele (m / min):
- puit, termoplast - 300 - 500;
- PVC - 100 - 250;
- roostevaba teras - 45 - 95;
- pronks - 90 - 150;
- messing - 130 - 320;
- bakeliit - 40 - 110;
- alumiinium ja selle sulamid - 200 - 420.
Lõikuri kiirus
Lihtsaim valem näeb välja selline:
N (pöörete arv) = 1000 Vc (soovitud lõikekiirus) / π D (lõikuri läbimõõt).
Ohutuse seisukohalt ei tohiks spindlit maksimaalsel kiirusel sõita. See tähendab, et ainult tänu sellele väheneb lõikekiirus umbes 10 - 15%. Seda "kaotust" saab osaliselt kompenseerida suurema läbimõõduga lõikuri paigaldamisega. See suurendab kiirust mõnevõrra. Kui sobivat käepärast pole, peate otsustama - kulutada raha uus tööriist või jääge rahule freespinki pakutavate võimalustega. Jällegi kontrollib seda kõike ainult konkreetsete seadmetega töötamise praktika, kuid terve mõistus soovitus on arusaadav.
Innings
Pöörake sellele jahvatusparameetrile suurt tähelepanu!
Lõikuri vastupidavus ja tooriku töötlemise kvaliteet sõltuvad sellest, kui paks kiht eemaldatakse ühe läbitungiga, see tähendab iga spindli pöördega. Sel juhul räägitakse 1 (2,3) hamba ettenihkest, olenevalt tööriista tüübist (ühe-, kahe- või kolmekäivitusega lõikur).
Soovitatavad väärtused ettenihke kohta hamba kohta määrab tööriista tootja. Freesioperaatoril on selles lõikerežiimi punktis raskusi, kui ta töötab "Hiinas valmistatud" või mõne kahtlase (tundmatu) päritoluga lõikuritega. Enamikul juhtudel saate keskenduda etteandevahemikule (mm) 0,1–0,25. See režiim sobib peaaegu kõigi tavaliste freesmaterjalide jaoks. Lõikamise käigus selgub, kas “lisamisest” piisab või vähe (aga mitte varem kui pärast 1. kõnet). Kuid alla 0,1 ei tohiks proovida, välja arvatud ehtetööde tegemisel mikroveskite abil.
Alusta freesimist minimaalse ettenihkega 0,1. Selle käigus selgub, kui tempermalmist on töödeldav materjal konkreetse lõikuri ees. See välistab lõikeserva (hamba) purunemise võimaluse ja võimaldab teha masina ja tööriista võimaluste täpset "diagnoosi", eriti kui tegemist on "võõra" seadmega.
- Optimaalse etteande väärtuse ületamine on täis temperatuuri tõusu tööpiirkonnas, paksude laastude moodustumist ja lõikuri kiiret purunemist. Tööriista puhul, mille läbimõõt on üle 3 mm, peaksite alustama 0,15-st, mitte rohkem
- Kui detaili freesimise kiirust pole võimalik seadmete võimaluste optimaalse kasutamise tõttu tõsta, võib proovida paigaldada kahekeermelise lõikuri.
- Tööriista valikul tuleb arvestada, et lõikeosa pikkuse suurenemine toob kaasa etteande vähenemise ja vibratsiooni suurenemise.
- Te ei tohiks püüda töötlemiskiirust suurendada, asendades lõikuri sarnase, kuid suure hulga hammastega. Sellise tööriista laastud on halvemad, seetõttu põhjustab see sageli freesimise kvaliteedi järsu languse. Mõnel juhul, kui sooned on täielikult täidetud, hakkab lõikur tühikäigul töötama. Sellisel asendamisel pole mõtet.
Järeldus
Kvaliteetset freesimist saab saavutada ainult kogemuste põhjal. Konkreetne tööpink + tööriist + praktiline kogemus, oskused. Seetõttu ei tohiks pimesi usaldada isegi tabeliandmeid. Näiteks ei võeta arvesse selle lõikuri kulumisastet, millega töötada. Katsetamist ei pea kartma, kuid alustama tuleks alati parameetrite minimaalsest väärtusest. Kui meister masinat, lõikurit ja töödeldavat materjali “katsutab”, määrab ta ise, millises režiimis tasub töötada.
Miks lõikur kiiresti tuhmub? Mis põhjustab töödeldud materjali (puitlaastplaat, MDF või puit) söestumise pärast freesimist? Miks lõikur põleb? Kuidas vältida vaikude kleepumist lõikuri lõikeservadele? Ülaltoodud küsimustele on ainult üks vastus - lõikuri pöörlemiskiirus (sagedus) on valesti valitud.
Kaasaegsed freesseadmed lamineeritud puitlaast- või MDF-plaatide materjalide töötlemiseks on varustatud mootoritega, mis võimaldavad saavutada spindli kiirust üle 20 000 p/min. Ühelt poolt mõjutab see seadmete tootlikkust, kuna tööriista kiirus või tooriku ettenihe suureneb. Teisest küljest tõuseb töötlemise kvaliteet: väheneb MDF-i hunniku kergitamise tõenäosus, puidule kulumiste ja lamineeritud puitlaastplaadi laastude ilmnemine.
Harjumusest, teadmatusest või lihtsalt laiskusest, et mitte jännata kõikvõimalike kasutusjuhendite, töötlemisrežiimide ja muude nippidega, seatakse lõikuri pöörlemiskiirus maksimaalsele tasemele, mille juures töödeldakse kõiki materjale. kõik saadaolevad lõikurid. See on see, mis valetab peamine põhjus kõik hädad.
Fakt on see, et lõikuri suure pöörlemiskiiruse (sageduse) ja tooriku madala etteandekiiruse korral muutub lõikuri lõikeserv enamus aja jooksul töötab see tühikäigul ja selle asemel, et töödeldavalt materjalilt veel üks laast ära lõigata, hõõrub see asjatult vastu. Kõik teavad, mis hõõrdumise – kuumenemise – tagajärjel juhtub. Veelgi enam, mida suurem on lõikuri pöörlemiskiirus, seda intensiivsem on hõõrdumine ja seda rohkem lõikur kuumeneb.
Tundub, et seal on midagi erilist? Noh, see on soe. Kui peopessa võtta, siis käsi peab vastu. Mis saab metallist? Aga siiski…
Miks lõikur põleb ja tuhmub kiiresti
Lõikurite hõõrdumisest materjalile tekkiv soojus jaotub järk-järgult ühtlaselt kogu selle kehale. Seetõttu ei ole lühiajalise töötamise ajal kuumutamist praktiliselt tunda. Kuid materjalide töötlemisel saavutab temperatuur maksimumtaseme just lõikeservades. Ja mida suurem on lõikuri pöörlemiskiirus, seda suurem on servade hõõrdumine ja kuumenemine.
See on eriti märgatav suure läbimõõduga lõikurite puhul. Siin liini kiirus lõikeserva välimise osa liikumine materjali suhtes on palju suurem. Selle tulemusena kuumenevad lõikuri servad ja tumenevad pärast jahtumist sinaka varjundiga ning see on kindel märk, et metall on kuumenenud sedavõrd, et see hakkab oma omadusi muutma. Teaduslikus mõttes põleb süsinikkomponent metallis läbi, mis annab sellele jäikuse omadused. Kui mäletate, kui pehmeks ja painduvaks muutub tavaline nael, olles ahjus või tules kuumades söes, siis on lihtne ette kujutada, millised uued omadused omandab lõikur ülekuumenemise tagajärjel.
Tasub lisada, et lõikuri teritamisel mõjutavad lihvketta või ketta pöörlemiskiirus ja tööriista surveaste otseselt teritatavate servade kuumenemist. Kui te jahutusvedelikku ei kasuta, muutub igasugune karbiidmetall tavaliseks rauatükiks, mis võib pärast deformeeruda väike koormus. Muide, seetõttu väheneb oluliselt lõikurite, puurite ja saagide tööiga pärast teritamist.
Miks materjal põleb
Siin on kõik väga selge: lõikuri hõõrdumise tagajärjel materjalile tekib kõrge temperatuur, mille mõjul hakkab puit läbi põlema. Selle nähtuse vältimiseks on vaja vähendada lõikuri pöörlemiskiirust (sagedust) ja suurendada tooriku etteandekiirust. Kuid neid toiminguid tuleks teha tingimusel, et lõikur on säilitanud oma teritamise. AT muidu, suureneb selle või jõuallika koormus märkimisväärselt, mis võib põhjustada nende rikke.
Lõikuri külge kleepuv vaik
Paljud puidud sisaldavad vaiku. Plaatide puitmaterjalide, nagu puitlaastplaat ja MDF, valmistamisel kasutatakse lisaks formaldehüüdvaikusid. Nende materjalide töötlemisel hõõrdumisel kuumutatud vaiguosakesed keevad, langevad lõikeriista hammastele ja kleepuvad koos tolmuga nende külge. Tavaliselt ei tekita see olulisi probleeme, kui tooriku etteanderežiim ja tööriista lõikekiirus on õigesti valitud. Vastasel juhul, kui üks parameeter on valesti arvutatud, on lõikuri pöörlemiskiirus liiga suur ja töötlemine toimub väikese kiirusega, ilmub tööriista lõikuritele tume vaigukate. Veelgi enam, mida tugevam on see lahknevus, seda kiiremini see moodustub. Samal ajal langeb töötlemise kvaliteet, lamineeritud pindadele ilmuvad laastud, puit hakkab põlema, tööriist saab lisakoormuse, kuumeneb kiiresti üle ja ebaõnnestub. Seetõttu on lõikuri kiiruse ja materjali etteandekiiruse valik nii oluline.
Lisaks materjalide töötlemisviisi õigele arvutamisele on vaja pöörata tähelepanu lõikeriista hooldamisele, see tähendab moodustunud vaiguladestiste õigeaegsele puhastamisele või tavalise sooja veega maha pesemisele. .
Lõikuri pöörlemiskiiruse (sageduse) arvutamine
Lõikuri pöörlemiskiiruse ja selle liikumiskiiruse õigeks arvutamiseks on vaja arvestada paljude teguritega, sealhulgas materjali ja tööriista füüsikalised ja mehaanilised omadused, töötlemise sügavus ja laius jne. .
Seevastu materjale nagu MDF ja puitlaastplaat on palju lihtsam töödelda kui näiteks erinevaid metalle. Seetõttu saab alust võtta ainult töötlemise kvaliteedi näitajana, see tähendab kareduse, servade, laastude ja kriimustuste olemasolu töödeldud pinnal.
Puitlaastplaadi lamineeritud plaatide enam-vähem kvaliteetseks töötlemiseks on vajalik, et ühe lõikehamba etteande kogus (või lihtsalt lõikuri alt väljuva laastu paksus) oleks 0,05 - 0,15 mm. Seega peaks tavaline kahe lõikuriga lõikur lõikama 0,1–0,3 mm pöörde kohta ja 1500–4500 mm 15 000 pöörde kohta. See tähendab, et materjali etteandekiirus lõikurile 15 000 pööret minutis peaks olema 1,5–4,5 m / min või 25–75 mm / s.
Kui soovite töödelda väikese ettenihkega, näiteks töötamise ajal manuaalne ruuter, siis saab lõikuri pöörlemiskiiruse arvutamise teha ruuteri liikumiskiiruse põhjal, tehes arvutused vastupidises järjekorras. Oletame, et materjali töödeldakse kiirusega 10 mm/sek ehk 600 mm/min. Kui ettenihe ühe hamba kohta on võrdne 0,1 mm ja kahe lõikuriga lõikuriga, on lõiketera vajalik pöörlemiskiirus 600/(0,1× 2) = 3000 pööret minutis.
Ettevaatusabinõud lõikuritega töötamisel
Reeglina lisavad freesseadmete ja -tööriistade tootjad oma toodetele ohutusjuhised ja näitavad freesi soovitatavad töörežiimid. Allolev tabel näitab lõikuri pöörlemiskiiruse ohutuid parameetreid sõltuvalt läbimõõdust.
Lõikuri läbimõõt, mm |
Lõikuri maksimaalne pöörlemiskiirus, p/min |
kuni 25 |
24000 |
26 – 50 |
18000 |
51 – 63 |
16000 |
64 – 75 |
14000 |
76 – 87 |
12000 |
LÕIKAMISREŽIIMI VALIK FRESIMISEKS
§ 78. LÕIKEREŽIIMI VALIKU MÄÄRAMISE TINGIMUSED
Kõige soodsama lõikerežiimi kontseptsioon
Sellist lõikamisrežiimi tuleks töötamisel pidada kõige soodsamaks freespink, mille juures on lõikekihi lõikekiirus, ettenihe ja sügavus kõige edukamalt kombineeritud, tagades etteantud kindlatel tingimustel (st võttes arvesse tööriista lõikeomaduste, masina kiiruse ja võimsuse parimat kasutamist) , kõrgeim tööviljakus ja toimingu madalaim hind, kui töötlemise täpsuse ja puhtuse osas on ette nähtud tehnilised tingimused.
NSV Liidu Ministrite Nõukogu Riikliku Töö- ja Tööküsimuste Komitee Tööuuringute Instituut palgad välja töötatud suurimate kodumaiste teadlaste osalusel, võttes arvesse praktilise rakendamise tootmistingimustes lõiketingimused kiirterasest ja kõvasulamitest valmistatud tööriistadega freesimisel. Neid saab kasutada algandmetena lõikekiiruste ja minutisöötmete määramisel.
Need standardid on saadaval igas tehases ja need on väljatöötamise juhised tehnoloogiline protsess ja lk 204-205 toodud töögraafikute koostamine. Nendes antud lõikekiirused ja minutisöödud ei ole aga piiravad ning mõnel juhul võivad freesid neid blokeerida, kui nad kasutavad tootlikumaid tööriistu või töötavad võimsamatel ja jäigematel masinatel.
Seevastu noored, st algajad ja piisava kogemuseta freesijad ei ole alati võimelised töötama piiravates lõiketingimustes, mistõttu on noorte freesija käsiraamatus neile ette nähtud leebemad lõiketingimused, millest alates täiendõppena on vaja liikuda rangemale.
Selleks, et ise uusi režiime tutvustada, pead teadma freesimisrežiimide seadistamise järjekorda ja järjestust.
Lõikuri lõikeosa materjal
Otsustavaks teguriks lõikerežiimi taseme määramisel on lõikuri lõikeosa materjal. Nagu eespool mainitud, võimaldab karbiidist sisetükkidega lõikurite kasutamine võrreldes kiirterasest valmistatud lõikuritega töötada suure lõikekiiruse ja suure ettenihkega; nagu allpool näeme, võimaldavad karbiidist lõikurid tõsta tootlikkust kaks kuni kolm korda võrreldes kiirlõikuritega. Seetõttu on peaaegu igat tüüpi freesimiseks soovitatav kasutada karbiidist lõikurid; nende kasutamise takistuseks võib olla seadmete ebapiisav võimsus või töödeldava tooriku materjali spetsiifilised omadused.
Mõnel juhul on aga süsiniku, legeeritud tööriista ja kiirteraste kasutamine freeside lõikeosas ratsionaalne, eriti kui töödeldud pinna puhtus ja sellest tuleneva detaili pinna täpsus on olulisemad kui töö kiirus.
Lõikeosa geomeetrilised parameetrid
Sama oluline lõiketingimuste valikut mõjutav tegur on lõikuri lõikeosa geomeetrilised parameetrid (lõikenurgad, hamba mõõtmed ja kuju), mida sageli nimetatakse nn. lõikuri geomeetria. Varem, §-s 7, käsitleti iga lõikehamba geomeetria elemendi tähendust ja mõju lõikeprotsessis; siin käsitleme P18 kiirterasest ja kõvasulamist plaatidega lõikurite lõikeosa soovitatavaid geomeetrilisi parameetreid.
Tabelis. 35 ja 36 näitavad kiirterasest valmistatud silindriliste, otsa-, ketta-, lõike-, otsa- ja kujuga lõikurite geomeetriliste parameetrite soovituslikke väärtusi.
Tabel 35
P18 kiirterasest valmistatud lõikurite lõikeosa geomeetrilised parameetrid
I. Esinurgad

II. Tagumised nurgad

III. Juht- ja üleminekunurgad

Märkmed. 1. Silindriliste lõikurite puhul, mille hammaste nurk on üle 30°, on terase töötlemisel kaldenurk γ väiksem kui 60 kg/mm 2 on võrdne 15°-ga.
2. Profiililõikuritel, mille kaldenurk on suurem kui 0°, on täpsete profiilide töötlemisel vajalik kontuuride korrigeerimine.
3. Kuumakindlate teraste töötlemisel otsafreesidega võtke esinurkade, otsa ja silindrikujuliste – alumise ja keskmise – ülemised väärtused.
4. Lõikurite tagumisele pinnale jätke teritamisel ringikujuliselt lihvitud lint, mille laius ei ületa 0,1. mm. Lõikuliste (piludega) ja eemaldatavate (ketassae) lõikurite hambad teritatakse ilma linti jätmata.

Tabelis. 37 - 40 on näidatud esi- ja taganurkade soovitatavad väärtused, plaani põhi-, abi- ja üleminekunurgad, lõiketera kaldenurgad ja spiraalsed sooned, raadius esikülje ülaosas, silindriline, ots ja kõvametallist sisestustega ketaslõikurid.
Enamiku toorikute töötlemiseks kasutatavaid freese tarnivad reeglina GOST-ile vastavate geomeetriliste parameetritega tööriistatehased ning freespinkil on erinevalt trei- ja höövlist peaaegu võimatu muuta lõikurite lõikenurki teritamise teel. Selle tulemusena on toodud tabelis. 35 - 40 lõikurite lõikeosa geomeetrilised parameetrid aitavad freesil valida õppe- ja tootmistsehhi tööriistasahvris leiduvate standardlõikurite hulgast õige antud töötlusele vastava lõikuri. Nende tabelite põhieesmärk on aga anda soovitusi juhuks, kui frees ise soovib selle töötlemise jaoks tellida optimaalsete geomeetriliste parameetritega standard- või spetsiaalseid freese.
Tabel 37
Karbiidist sisetükkidega otsafreeside lõikeosa geomeetrilised parameetrid

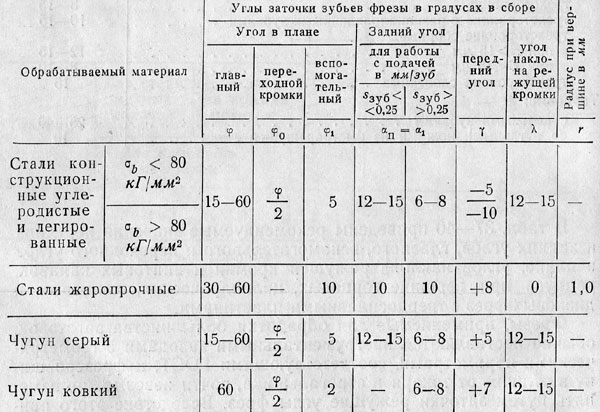
Märge. Väiksemaid esinurki φ = 15 - 30° tuleks kasutada jäikade masinatega töötlemisel väikese lõikesügavusega töötlemiskäikudeks või viimistlustöödeks, mille puhtuse ja täpsuse nõuded töödeldava pinna suhtes on madalad.
Tabel 38
Kõvasulamist spiraalsete teradega silindriliste lõikurite lõikeosa geomeetrilised parameetrid


Märge. Hamba tagapinnal piki lõikeserva lint, mille laius ei ületa 0,1 mm.
Tabel 39
Volframkarbiiddetailidega otsafreeside lõikeosa geomeetrilised parameetrid struktuursete süsinik- ja legeerteraste töötlemisel


* Süsteemi masina – kinnitusdetaili – tööriista – osa madala jäikusega ja suurte laastuosadega ( AT rohkem D; t rohkem kui 0,5 D), samuti töötamisel madalad kiirused lõikamine ebapiisava spindli kiirusega ( v alla 100 m/min) kaldenurk γ on määratud positiivseks + vahemikus 0 kuni +8°.
** Suuremad väärtused pehmete teraste puhul, väiksemad kõvade teraste puhul.
Freesimise laius ja sügavus
Freesimise laius detaili joonisel täpsustatud. Mitme paralleelselt kinnitatud tooriku töötlemisel ühes kinnitusseadmes on freesimise laius võrdne kõigi toorikute laiusega. Freesimisel koos freesikomplektidega on freesimise laius võrdne kõigi ühenduspindade kogulaiusega.
Freesimise sügavus(lõikesügavus, lõikekihi paksus) on antud kaugusena töödeldud ja töödeldud pindade vahel. Töötlemisaja vähendamiseks on soovitatav freesimine läbi viia ühe käiguga. Kõrgendatud nõuetega töödeldud pinna täpsusele ja puhtusele toimub freesimine kahes etapis - karestamine ja viimistlemine. Mõnel juhul on suurte varude eemaldamisel või ebapiisava võimsusega masinatel freesimisel võimalik töötlemine kahe jämetöötluskäiguga.
Tabel 40
Karbiidsisustustega ketaslõikurite lõikeosa geomeetrilised parameetrid


Katlakiviga, valukoorikuga kaetud või valuliivaga saastunud terassepiste, teras- ja malmvalandite freesimisel peab freesimise sügavus olema suurem saastunud kihi paksusest, et lõikuri hambad ei jätaks töödeldud pinnale musti lõikeid, kuna piki maakoort libisemine mõjutab lõikurit negatiivselt, kiirendades lõiketera kulumist.
Levinumate freesimisjuhtumite puhul on soovitatav teostada terase karestamine lõikesügavusega 3-5 mm, ja terasel ja Malm- lõikesügavusega 5-7 mm. Viimistlemiseks freesimiseks võta lõikesügavus 0,5-1,0 mm.
lõikuri läbimõõt
Lõikuri läbimõõt valitakse peamiselt sõltuvalt freesi laiusest AT ja lõikesügavus t. Tabelis. 41 on näidatud silindriliste lõikurite valiku andmed tabelis. 42 - otsafreesid ja tabelis. 43 - ketaslõikurid.

* Kasutage GOST 1979-52 järgi kokkupandavaid liitlõikureid.


Mõelge lõikuri läbimõõdu mõjule freesimise jõudlusele.
Silindrilise lõikuri läbimõõt mõjutab lõike paksust: mida suurem on lõikuri läbimõõt D mida õhem on lõige; sama pakkumisega s hammaste ja freesimissügavus t.
Joonisel fig. 327 on näidatud sama freesimissügavusega tehtud lõige t ja esitamine s hammas, kuid erineva läbimõõduga lõikuritega. Lõiketera suurema läbimõõduga (joonis 327, a) saadud lõige on väiksema paksusega kui väiksemaga tehtud lõige; lõikuri läbimõõt (joonis 327, b).

Kuna erirõhk suureneb lõigatud kihi paksuse vähenemisega a naib (vt tabel 38), on tulusam töötada paksemate viiludega, st ceteris paribus, väiksema lõikuri läbimõõduga.
Lõikuri läbimõõt mõjutab tee pikkust, mille lõikur peab ühe käiguga läbima.
Joonisel fig. 328 näitab teekonda, mille lõikur peab pikkusega detaili töötlemisel läbima L; joonisel fig. 329 - tee, mille esifrees peab läbima töödeldava detaili asümmeetrilise freesimise pikkusega L; joonisel fig. 330 - tee, mille koogilõikur peab läbima, kui freesitakse sümmeetriliselt töödeldavat detaili pikkusega L.

Toiteväärtus l(sisselõigatud tee):
silindriliste, ketas-, lõike- ja kujuga lõikuritega töötamisel sõltub lõikuri läbimõõt D freesimise sügavus t ja seda väljendatakse valemiga
otsafreeside ja asümmeetrilise freesimise otsfreesidega töötamisel sõltub lõikuri läbimõõt D freesimise laius AT ja seda väljendatakse valemiga
töötamisel tahvfreesidega, kui sümmeetriline freesimine sõltub lõikuri läbimõõdust D freesimise laius AT ja seda väljendatakse valemiga
Ülekulu väärtus l 1 valitakse sõltuvalt lõikuri läbimõõdust vahemikus 2-5 mm.
Seetõttu on lõikuri sisestamise ja ülejooksu tee vähendamiseks, st masina tühikäigu vähendamiseks soovitatav valida väiksem lõikuri läbimõõt.
Raamatu lõpus, lisades 2 ja 3, on tabelid lõikurite laskumistee ja ülejooksu väärtuste tabelid.
Lõikuri läbimõõt mõjutab väärtust pöördemoment: mida väiksem on lõikuri läbimõõt, seda vähem tuleb masina spindlile anda pöördemomenti.
Seega tunduks väiksema läbimõõduga lõikuri valik sobivam. Kuid lõikuri läbimõõdu vähenemisel on vaja valida õhem, st vähem jäik freessüdamik, mistõttu on vaja vähendada torni koormust, st vähendada lõigatud kihi ristlõiget. .
Innings
Sööda kell karestamine sõltub töödeldavast materjalist, lõikuri lõikeosa materjalist, masina ajami võimsusest, süsteemi masina - kinnitusseadme - tööriista - detaili jäikusest, töötlemismõõtmetest ja lõikuri teritusnurkadest.
Sööda kell viimistlus sõltub detailjoonisel märgitud pinna puhtusklassist.
Peamiseks sisendiks jämedaks freesimiseks ettenihke valimisel on etteanne s hammas.
Söödavalikuga esifreesidele s hammas annab võimaluse lõikuri paigaldamiseks töödeldava detaili suhtes, mis määrab lõiketera hamba nurga toorikuga kokkupuutel ja lõigatud laastude paksuse lõikehamba sisenemisel ja kokkupuutel toorikuga. On kindlaks tehtud, et karbiidfreesi puhul saavutatakse kõige soodsamad tingimused hamba lõikamiseks toorikuks, kui lõikur asub tooriku suhtes, nagu joonisel fig. 324, c, st kui lõikur on tooriku suhtes nihkes FROM = (0,03 - 0,05)D. Lõikuri telje selline nihe võimaldab suurendada sümmeetrilisel freesimisel (joonis 324, a) malmi ja terase ettenihet ühe hamba kohta ettenihke suhtes kahe või enama teguri võrra.
Tabelis. Tabelis 44 on näidatud nende kahe juhtumi puhul soovitatavad ettenihked karbiidfreesidega töötlemata freesimiseks.

Märkmed. 1. Näidatud jämetöötluse ettenihked põhinevad tavalistel freesidel. Suurenenud hammaste arvuga mittestandardsete lõikuritega töötamisel tuleks etteandeväärtusi vähendada 15–25%.
2. Lõikuri algsel tööperioodil kuni kulumiseni 0,2-0,3 mm, väheneb töödeldud pinna puhtus peenfreesimisel umbes ühe klassi võrra.

Märge. Võtke suuri etteande väiksema lõikesügavuse ja töötlemislaiuse jaoks, väiksemaid ettenihkeid suurte sügavuste ja töötlemislaiuste jaoks.

Märge. Etteanded on antud jäiga süsteemi masina - kinnitusdetaili - tööriista - detaili jaoks.
Karbiidlõikuritega tahvfreesimisel mõjutab esinurk φ ka ettenihke kiirust. Tabelis esitatud ettepanekud. 44 on mõeldud lõikurite jaoks, mille φ = 60 - 45°. Juhtnurga φ vähendamine 30°-ni võimaldab etteannet 1,5 korda suurendada ja nurga φ suurendamine 90°-ni nõuab ettenihke vähendamist 30%.
Etteanded karbiidlõikuritega viimistlemiseks on toodud tabelis. 44 on antud ühe lõikuri pöörde kohta, kuna ettenihked ühe hamba kohta on liiga väikesed. Söödad antakse sõltuvalt töödeldud pinna puhtusklassist vastavalt standardile GOST 2789-59.
Tabelis. 45 näitab soovitatavat ettenihet lõikehamba kohta silindrilise, esipinna ja kettaga tasapindade töötlemata freesimisel kolmnurksed lõikurid kiirterasest P18.
Tabelis. 46 kujutab ettenihkeid tasapindade viimistlusfreesimisel P18 kiirterasest valmistatud silindriliste lõikuritega ja tabelis. 47 - freespindade viimistlemisel P18 kiirterasest esi- ja ketas kolmepoolsete lõikuritega. Tänu väikestele ettenihke väärtustele ühe lõikuri hamba kohta, mis on saadud peenfreesimisel, tabelis. 46 ja 47 on ettenihked ühe lõikuri pöörde kohta.
Tuleb meeles pidada, et töötage tabelis näidatud söötadega. 44-47, seab hädavajalikuks tingimuseks lõikuri hammaste minimaalse väljavoolu olemasolu (vt tabel 50).

Märge. Ettenihked on antud jäiga süsteemi masin - kinnitus - tööriist - detail freesimisel freesidega abinurgaga plaanis φ 1 = 2°; lõikurite puhul, mille φ 1 = 0, saab etteannet suurendada 50 - 80%.