SA kategorya:
Paggiling ng trabaho
Pagpipilian ng mga rational milling mode
Ang pagpili ng isang makatwirang mode ng paggiling sa isang naibigay na makina ay nangangahulugan na para sa ibinigay na mga kondisyon ng machining (materyal at grado ng workpiece, profile at sukat nito, allowance sa machining), kinakailangan upang piliin ang pinakamainam na uri at sukat ng cutter, grado ng materyal at geometric na mga parameter ng cutting part ng cutter, cutting fluid at italaga ang pinakamainam na halaga ng mga sumusunod na parameter ng cutting mode: B, t, . v, n, Ne, Tm.
Mula sa formula (32) sumusunod na ang mga parameter B, t, sz at v ay may parehong epekto sa volumetric na produktibidad ng paggiling, dahil ang bawat isa sa kanila ay pumapasok sa formula sa unang antas. Nangangahulugan ito na sa isang pagtaas sa alinman sa mga ito, halimbawa, sa pamamagitan ng isang kadahilanan ng dalawa (na may iba pang mga parameter na hindi nagbabago), ang volumetric na produktibo ay tataas din ng isang kadahilanan ng dalawa. Gayunpaman, ang mga parameter na ito ay walang parehong epekto sa buhay ng tool (tingnan ang § 58). Samakatuwid, isinasaalang-alang ang buhay ng tool, mas kapaki-pakinabang na una sa lahat piliin ang pinakamataas na pinahihintulutang halaga ng mga parameter na may mas mababang epekto sa buhay ng tool, ibig sabihin, sa sumusunod na pagkakasunud-sunod: lalim ng hiwa, feed sa bawat ngipin at bilis ng pagputol. Samakatuwid, ang pagpili ng mga parameter na ito ng mga mode ng pagputol sa panahon ng paggiling sa makina na ito ay dapat na magsimula sa parehong pagkakasunud-sunod, lalo na:
1. Ang lalim ng hiwa ay itinalaga depende sa machining allowance, ang mga kinakailangan para sa pagkamagaspang sa ibabaw at ang kapangyarihan ng makina. Ito ay kanais-nais na alisin ang allowance para sa pagproseso sa isang pass, isinasaalang-alang ang kapangyarihan ng makina. Karaniwan, ang lalim ng hiwa para sa magaspang na paggiling ay hindi lalampas sa 4-5 mm. Para sa magaspang na paggiling gamit ang mukha mga pamutol ng karbida(mga ulo) sa makapangyarihang mga milling machine, maaari itong umabot sa 20-25 mm o higit pa. Kapag tinatapos ang paggiling, ang lalim ng hiwa ay hindi lalampas sa 1-2 mm.
2. Ang pinakamataas na pinapahintulutang feed ayon sa mga kondisyon sa pagpoproseso ay itinalaga. Kapag nagtatakda ng pinakamataas na pinapahintulutang feed, dapat gamitin ang mga feed sa bawat ngipin na malapit sa "pagsira" ng mga feed.
Ang huling formula ay nagpapahayag ng pag-asa ng feed sa bawat ngipin sa lalim ng paggiling at ang diameter ng cutter. Ang halaga ng maximum na kapal ng slice, ibig sabihin, ang halaga ng pare-parehong koepisyent I c sa formula (21), ay nakasalalay sa pisikal at mekanikal na mga katangian ng materyal na pinoproseso \ (para sa isang naibigay na uri at disenyo ng pamutol). Ang mga halaga ng maximum na pinapahintulutang feed ay nalilimitahan ng iba't ibang salik:
a) sa panahon ng roughing - ang rigidity at vibration resistance ng tool (na may sapat na rigidity at vibration resistance ng machine), ang rigidity ng workpiece at ang lakas ng cutting part ng tool, halimbawa, ang ngipin ng cutter, ang hindi sapat na volume ng chip grooves, halimbawa, para sa mga disk cutter, atbp. .4 mm / toothron hanggang sa pagpoproseso ng ngipin 0.
b) kapag tinatapos - pagkamagaspang sa ibabaw, katumpakan ng sukat, ang estado ng layer ng ibabaw, atbp. Kapag tinatapos ang paggiling ng bakal at cast iron, ang isang medyo maliit na feed sa bawat cutter tooth (0.05-0.12 mm / tooth) ay itinalaga.
3. Natutukoy ang bilis ng pagputol; bilang siya ang pinaka malaking impluwensya sa tibay ng tool, pagkatapos ay pinili ito batay sa pamantayan ng tibay na pinagtibay para sa tool na ito. Ang bilis ng pagputol ay tinutukoy ng formula (42) o ayon sa mga talahanayan ng mga pamantayan para sa mga kondisyon ng pagputol, depende sa lalim at lapad ng paggiling, feed sa bawat ngipin, diameter ng cutter, bilang ng mga ngipin, mga kondisyon ng paglamig, atbp.
4. Ang epektibong cutting power Ne ay tinutukoy sa napiling mode ayon sa mga talahanayan ng mga pamantayan o ayon sa formula (39a) at inihambing sa kapangyarihan ng makina.
5. Ni itakda ang bilis pagputol (u, o i ^) ang pinakamalapit na hakbang ng bilis ng spindle ng makina ay tinutukoy mula sa mga magagamit sa makinang ito ayon sa formula (2) o ayon sa iskedyul (Fig. 174). Mula sa punto na naaayon sa tinanggap na bilis ng pagputol (halimbawa, 42 m / min), isagawa pahalang na linya, at mula sa isang punto na may marka ng napiling diameter ng pamutol (halimbawa, 110 mm) - patayo. Sa punto ng intersection ng mga linyang ito, ang pinakamalapit na hakbang ng bilis ng spindle ay tinutukoy. Kaya, sa halimbawang ipinapakita sa Fig. 172, kapag ang paggiling gamit ang isang pamutol na may diameter na D = 110 mm sa bilis ng pagputol na 42 m/min, ang bilis ng spindle ay magiging 125 rpm.
Fig.174 Nomogram ng bilis ng paggiling ng pamutol
6. Ang minutong feed ay tinutukoy ng formula (4) o ayon sa iskedyul (Fig. 175). Kaya, kapag nagpapaikut-ikot gamit ang isang pamutol D = 110 mm, z = 10 sa sz = 0.2 mm/ngipin at n = 125 rpm, ang minutong feed ayon sa iskedyul ay tinutukoy bilang mga sumusunod. Mula sa punto na naaayon sa feed sa bawat ngipin sg = 0.2 mm / ngipin, gumuhit kami patayong linya hanggang sa ito ay bumalandra sa isang hilig na linya na naaayon sa bilang ng mga ngipin ng pamutol r = 10. Mula sa nakuha na punto, gumuhit kami ng isang pahalang na linya hanggang sa ito ay bumalandra sa isang hilig na linya na naaayon sa tinatanggap na bilis ng spindle l = 125 rpm. Susunod, gumuhit ng patayong linya mula sa nagresultang punto. Tinutukoy ng intersection point ng linyang ito na may mas mababang sukat ng mga minutong feed na available sa makinang ito ang pinakamalapit na hakbang ng mga minutong feed.
7. Natutukoy ang oras ng makina.
oras ng makina. Ang oras kung saan nagaganap ang proseso ng pag-alis ng chip nang walang direktang partisipasyon ng manggagawa ay tinatawag na oras ng makina (halimbawa, para sa paggiling ng workpiece plane mula sa sandaling naka-on ang mechanical longitudinal feed hanggang sa ito ay patayin).
kanin. 1. Nomogram ng minutong feed
Ang mga nadagdag sa pagiging produktibo sa pagma-machine sa mga metal cutting machine ay nalilimitahan ng dalawang pangunahing salik: ang mga kakayahan sa produksyon ng makina at ang mga katangian ng pagputol ng tool. Kung ang mga kakayahan sa produksyon ng makina ay maliit at hindi pinapayagan ang buong paggamit ng mga katangian ng pagputol ng tool, kung gayon ang pagiging produktibo ng naturang makina ay magiging isang bahagi lamang ng posibleng produktibidad na may pinakamataas na paggamit ng tool. Kung sakaling ang mga kakayahan sa produksyon ng makina ay higit na lumampas sa mga katangian ng pagputol ng tool, ang makina ay maaaring makamit ang pinakamataas na posibleng produktibidad sa isang naibigay na tool, ngunit ang mga kakayahan ng makina, ibig sabihin, ang kapangyarihan ng makina, ang maximum na pinapahintulutang puwersa ng pagputol, atbp., ay hindi ganap na magagamit. Pinakamainam mula sa punto ng view ng pagiging produktibo at pang-ekonomiyang paggamit ng mga kaso ng makina at ang kagamitan at kapasidad ng paggawa ay magiging ganoong mga katangian ng makina at ang kagamitan at kapasidad ng makina. malapit sa isa't isa.
Ang kundisyong ito ay ang batayan ng tinatawag na mga katangian ng produksyon ng mga kagamitan sa makina, na iminungkahi at binuo ng prof. A. I. Kashirin. Ang katangian ng produksyon ng makina ay isang graph ng mga dependency sa pagitan ng mga kakayahan ng makina at ng tool. Ang mga katangian ng produksyon ay ginagawang mas madali at mas madali upang matukoy ang pinakamainam na kondisyon ng pagputol kapag nagpoproseso sa isang partikular na makina.
Ang mga katangian ng pagputol ng isang partikular na tool ay nailalarawan sa pamamagitan ng mga kondisyon ng pagputol na pinapayagan sa panahon ng pagproseso. Ang bilis ng pagputol sa ilalim ng ibinigay na mga kondisyon sa pagproseso ay maaaring matukoy ng formula (42, a). Sa pagsasagawa, ito ay matatagpuan ayon sa talahanayan ng mga kondisyon ng pagputol, na ibinibigay sa mga reference na libro ng rater o technologist. Gayunpaman, dapat tandaan na ang mga pamantayan para sa mga kondisyon ng pagputol para sa parehong paggiling at iba pang mga uri ng pagproseso ay binuo batay sa mga katangian ng pagputol ng tool para sa iba't ibang okasyon pagpoproseso (uri at sukat ng tool, uri at tatak ng materyal ng bahagi ng pagputol, materyal na pinoproseso, atbp.), at hindi nauugnay sa mga makina kung saan isasagawa ang pagproseso. Dahil ang mga kakayahan sa produksyon ng iba't ibang mga makina ay iba, ang praktikal na magagawa na pinakamainam na mode ng pagproseso sa iba't ibang mga makina ay magiging iba para sa parehong mga kondisyon sa pagpoproseso. Ang mga kakayahan sa produksyon ng mga kagamitan sa makina ay pangunahing nakasalalay sa epektibong kapangyarihan ng makina, bilis, feed, atbp.
kanin. 2. Plunge at overrun
Ang mga katangian ng produksyon ng mga milling cutter para sa kaso ng pagputol na may mabibigat na pamutol ay binuo ni Prof. A. I. Kashirin at ng may-akda.
Ang prinsipyo ng pagbuo ng mga katangian ng produksyon ng mga milling machine (nomograms) para sa pagtatrabaho sa mga face mill ay batay sa pinagsamang graphic na solusyon dalawang equation na nagpapakilala sa dependence ng cutting speed vT ayon sa formula (42) na may -Bz' = const, sa isang banda, at ang cutting speed id„, ang pinapahintulutang kapangyarihan ng makina, sa kabilang banda. Ang bilis ng pagputol vN ay maaaring matukoy mula sa formula
kanin. 3. Mga katangian ng produksyon ng console milling machine 6P13
Mga kondisyon ng pagputol
Mga pamutol ng kaliwang kamay
Bakit mas mabuti ang paggiling laban sa feed.Problema: Tinutunaw ng 2-start cutter ang PVC foam.
Solusyon: pumili ng mas maliit na bilang ng mga rebolusyon o gilingan na may single-thread cutter. (Larawan)
1. Paglulubog:
Ang pamutol ay dapat na makapasok sa dulo ng mukha sa materyal (pagbabarena function).
2. Cutting edge:
Bilang isang patakaran, ang mga gilid ng daanan ay naiiba sa bawat isa. Ang counter side ng paggalaw ay "mas maganda" kaysa sa side ng synchronicity. Ito ay lalo na maliwanag kapag gumagamit ng isang 1-start cutter, pati na rin kapag milling ng aluminyo.
Payo; I-mill ang panloob na mga contour clockwise, ang panlabas na counterclockwise. Kaya ang "masamang" bahagi ay nasa chips
3. Pag-alis ng chip:
Ang mga chips ay dapat na mabilis na lumikas upang ang mga cavity ng mga cutter ay hindi mapuno, at bilang isang resulta ang cutter ay hindi masira. Ang mas malalim at mas mabilis na paggiling ay nangyayari, mas mahirap na ilikas ang mga chips. Mga Direksyon: Huwag gilingin nang mas malalim kaysa doble o triple ang diameter ng pamutol. Pumunta sa mas malalim na mga grooves sa ilang mga pass. Kapag nagpapaikut-ikot ng polystyrene at iba pang plastik, makatuwirang gumamit ng mga cutter na may pinakintab na plauta para sa mas mahusay na output.
4. Pag-alis ng init / pagpapadulas:
Ang pamutol ay hindi dapat masyadong mainit: Sa isang banda, ang isang tool na may masyadong mataas na temperatura ay nawawala ang mga katangian nito, sa kabilang banda, kahit na mas kritikal, ang plastic at aluminum chips ay maaaring "dumikit" sa mga grooves, na pumipigil sa pag-alis ng mga chips at, bilang isang resulta, na humahantong sa pagbasag ng cutter. Kapag nagpoproseso ng mga metal, kinakailangang magrekomenda ng pampadulas. Tandaan: Ang mga aluminyo at non-ferrous na metal ay maaaring gilingin ng alkohol o mga espesyal na emulsyon, at ang tubig na may sabon ay maaaring gamitin para sa plexiglass.
5. Panganib ng pagkasira:
tumataas nang linear sa pagtaas ng rate ng feed at sa pagtaas ng lalim ng immersion: Ang double feed ay nangangahulugang doble ang fractional na panganib, doble ang immersion depth ay nangangahulugang walong beses ang fractional na panganib.
Direksyon:
Mas mainam na gilingin sa maraming pass nang hindi gaanong malalim at sa mas mataas na rate ng feed. Gumamit ng pamutol na may pinakamaikling haba ng pagputol na posible. Higpitan ito hangga't maaari. Pangkalahatang tuntunin: naka-clamp sa chuck (chuck collet) one third Kabuuang haba mga pamutol.
Ang tamang hiwa ay nagdadala ng mga chips sa itaas.
Ang tamang cut cutter ay nagpapadali sa pag-alis ng mga chips up, na mabuti para sa tuluy-tuloy na output, gayunpaman, ito ay may kawalan na ang cutter, tulad ng isang corkscrew, ay inililipat din ang base na materyal (blangko) pataas, "mohr" kapag milling ng kahoy o "burrows" kapag nagpoproseso ng manipis na sheet na materyal (halimbawa, lata). Ang isang pamutol na may kaliwang helix, sa tapat, ay pumipindot sa materyal at kapag pinuputol ang mga fibrous na materyales tulad ng kahoy o karton, makakamit mo ang isang mas makinis na gilid sa itaas (ang mga hibla ay hindi tumataas, ngunit "pinipindot" sa base na materyal). Ngunit dito ang negatibong kadahilanan ay ang kahirapan ng pag-alis ng chip.
Tandaan:
Sa karaniwang mga kaso, gumamit ng pamutol ng kanang kamay.
Ang mga pamutol ng kaliwang kamay ay kapaki-pakinabang para sa mababaw na hiwa manipis na materyales, kung saan ang panganib ng "burrowing" at jerking up ang workpiece ng tamang hiwa ay malaki. Gayunpaman, mas mahirap ang materyal na iyong ginagamit, mas maaga mong mapupuksa ang kaliwang helix cutter.
A. Kanang hiwa (normal na anyo):
Hilahin ang string pataas. Ang pamutol ay may posibilidad na "burrow" at iangat ang base material.
"corkscrew effect".
B. Kaliwang helix (espesyal na hugis): Ibinababa ang mga chips kapag nakaharap, o ginagamit kapag nagtatrabaho sa isang na-milled na lukab. Pinindot ng pamutol ang base material (kabaligtaran ng "corkscrew effect").
Hindi angkop para sa malalim na paggiling.
Uri ng pamutol: 1 o 2 blades?
Mayroong isang walang katapusang bilang ng mga cutter, ngunit mahalagang gumawa kami ng pagkakaiba sa pagitan ng matalim at mapurol. Kung mas matalas ang talim, mas mabilis maubos ang dulo.Pangkalahatang tuntunin: mas mataas ang lakas ng materyal, mas flat ang hasa dapat sa talim. Ang pagpapatalas na ito ay angkop para sa matitigas na metal (hal. tanso). Mas matalas na fishtail sharpening para sa mga plastik, kahoy at malambot na aluminyo. Ang mga blades ay mga bahagi ng pamutol na mataas ang suot. Sa mga cutter na may higit sa isang talim, ang load ay ipinamamahagi at ang buhay ng tool ay nadagdagan. Ang mga cutter na ito ay tumatakbo nang mas mabilis, mas mababa ang vibrate sa mahihirap na materyales tulad ng hindi kinakalawang na asero. Sa ilang mga blades - sa ilalim ng parehong mga kondisyon ng paggiling - ang mga chips ay mas payat, na nagreresulta sa isang mas makinis na ibabaw sa dulo.
Ang pagpili ng "ideal" na uri ng pamutol ay palaging nakasalalay sa materyal na gagawing makina:
Kapag nagpapaikut-ikot ng mga "malambot" na materyales: ang malambot na plastik (PVC, plexiglass, foam), mga materyales na gawa sa kahoy (kahoy, fibreboard, plywood, chipboard), malambot na aluminyo at mga materyales sa sandwich (aluminium/plastic) ay nakikinabang mula sa matatalas na 1-start cutter. Dahil dito ang problema ng mas mabilis na blunting ay higit na mabuti kaysa sa panganib ng pagbara at pagbasag ng pamutol.
Para sa matigas na plastik angkop na matalas na 2-way, na may profile ng fishtail.
Kapag gumagawa ng mas matitigas na metal gaya ng tanso, maaaring irekomenda ang 2-start cutter na may patag na lupa.
Kapag nagpapaikut-ikot ng napakahirap na istrukturang bakal o napakataas na kalidad na bakal, gumamit ng tatlo o apat na lead cutter.
Single start cutter sa cross section
Ang isang kutsilyo ay nag-iiwan ng malaking espasyo
para sa pagtanggal ng chip
Three-start cutter sa cross section
Ang tatlong blades ay makabuluhang bawasan ang espasyo
para sa pagtanggal ng chip
Mga pagkakaiba sa pagitan ng isang pamutol at isang ukit
Maraming tao ang gumagamit ng konsepto ng "cutter" at "engraver" bilang kasingkahulugan. Gayunpaman, pinag-uusapan natin ang tungkol sa dalawang magkaibang tool.
Ang engraver ay isang simpleng kasangkapan, isang silindro na nahati sa kalahati, na sinusundan ng paggiling sa likod.
Maaaring iba ang hugis; ang pinakakaraniwan ay tatsulok. Hindi tulad ng mga milling cutter, wala silang helical chip chute.
Tool material: HSS o carbide?
Sa teknolohiya ng advertising, ang mga carbide milling cutter ay kadalasang ginagamit.
Ang Carbide (HM) ay isang mahal, artipisyal na produkto na pinagsama-sama mula sa mga pinong pulbos (hal. Wolfram-Carbid). Sa panahon ng proseso ng pagsasama-sama, ang hugis ng pamutol ay agad na nalikha at pagkatapos ay hindi nagbabago (ito ay pinatalas lamang). Ang karbida ay napakatigas at lumalaban sa pagsusuot, ngunit madaling kapitan ng panginginig ng boses at pagkabigla. Ito ay mahalaga kapag gumagamit ng HM milling cutter upang magkaroon ng isang matatag, posibleng mas mabigat at mas malaking makina, isang spindle na may tumpak na pag-ikot at mataas na kalidad na clamping collet. Ang materyal na giniling ay dapat na matatag at matatag na naayos sa makina.
Ang high speed steel (HSS) ay pangunahing ginagamit kung saan ang carbide ay masyadong sensitibo: kapag milling ng hindi kinakalawang na asero, sa umaalog na mga makina, o sa mga kaso kung saan ang higpit ng fixation ay hindi sapat na natiyak. Mas mabilis ang pagsusuot ng HSS, ngunit mas mababa ang panganib ng napaaga na pagkabigo dahil sa katigasan nito.
Ang buhay ng HSS coated cutter ay lubhang nadagdagan. Halimbawa, para sa titanium nitride (TiN), ang buhay ng serbisyo ay nadagdagan ng anim na beses.
Ang Titan-Nitrid ay makabuluhang mas matigas kaysa sa HSS at mas matigas din kaysa sa HM. Gamit ang Titan-Nitrid coating, ang mga tool ng HM ay tumatagal din, kahit na ang pagkakaiba sa tigas ay bale-wala.
Higit na makabuluhan, ang saklaw ay makikita sa bilang ng mga rebolusyon at feed. Maaari itong dagdagan at paikliin sa ganitong paraan ang oras ng pagproseso. Sa paggiling ng aluminyo, pinipigilan ng TiN ang nakakatakot na pagluluto ng aluminyo sa cutter. Ang patong ay kumikilos tulad ng Teflon sa isang kawali (ang shavings slide)
Bilis at pinakamainam na feed
Ang pinakamahalagang parameter sa paggiling ay ang bilang ng mga rebolusyon at ang feed. Ang data sa talahanayan ay naaayon sa karamihan sa mga rekomendasyon ng mga tagagawa ng pamutol. (Kung may pagdududa, tanungin ang supplier kung aling mga mode ang inirerekomenda nila para sa kanilang produkto).Una, kunin ang inirerekomendang bilis ng pagputol para sa materyal na pinoproseso at ilapat ito sa formula para sa pagkalkula ng bilang ng mga rebolusyon.
Kung ang isang makina na hindi masyadong matibay ay ginagamit, pagkatapos ay ang bilang ng mga rebolusyon ay tinutukoy sa itaas na rehiyon, at ang feed sa mas mababang rehiyon. Kung ang bilang ng mga rebolusyon ay kilala, pagkatapos ay ang feed ay kinakalkula gamit ang formula.
Sa prinsipyo ito ay isinasaalang-alang: Kung mas mataas ang bilis ng pagputol (vc = p * d * n), magiging mas makinis ang ibabaw. Gayunpaman, ang pagkapurol ng pamutol ay tumataas din sa bilis ng pagputol.
Pamamaraan sa pagkalkula:
1. Bilang ng mga rebolusyon n:
Piliin ang bilis ng pagputol vc mula sa mesa. (Kung ang bilis ng pagputol ng materyal ay lubhang nag-iiba, suriin sa mga manual).
Batay sa data, kalkulahin ang bilang ng mga spindle revolution
N = (vc *1000) / (3.14 * d)
F = n*fz*z
fz = feed bawat 1 ngipin
z = bilang ng mga blades
Halimbawa:
Gusto mong gilingin ang matigas na aluminyo, na may 3mm diameter na 2-start cutter. Mula sa talahanayan makikita mo ang: vc = 100...200 m/min. Mula dito kinakalkula mo:Max. bilang ng mga rebolusyon: n = (200 * 1000) / (3.14 * 3) = 200,000 / 9.42 = 21.230 U/min
Kaugnay na feed: f = 21230 * 0.04 * 2 = 1698mm/minAng mataas na rate ng feed - lalo na sa mga metal - ay nangangailangan ng isang matatag at tahimik na makina. Bilang karagdagan, ang lalim ng uka ay hindi dapat masyadong malaki (mga 1 * d 1).
Para sa mga hindi gaanong matatag na makina o may tumaas na lalim ng paggiling, ang mode ay kinakalkula bilang mga sumusunod:Max. bilis:
n = (200 * 1000) / (3.14 * 3) = 200,000 / 9.42 = 21.230 U/min(tulad ng nasa itaas)
Min. bilang ng mga rebolusyon: n = (100 * 1000) / (3.14 * 3) = 100,000 / 9.42 = 10.615 U/min
Kaugnay na feed (minimum): f = 10615 * 0.04 * 2 = 849mm/minPinagsasama mo ang n=21230 U/min at f=849 mm/min.
Counter-motion at synchronized na paggalaw
Paano nilikha ang iba't ibang mga gilid ng hiwa:Ang talim ay pumapasok mula sa windward side papunta sa materyal. Sa lugar ng kontrol ng paggalaw, ang pamutol ay tumatakbo laban sa materyal. Ang kapal ng chip ay magiging batayan ng feed sa materyal ay patuloy na mas malaki. Sa kasabay na rehiyon, ang pamutol ay tumatakbo kasama ang materyal, ang kapal ng chip ay nabawasan upang lumabas. Ipinapakita ng shaded area ang relatibong kapal ng chip sa bawat posisyon ng chip bawat rebolusyon. Ang talim sa counter motion ay patuloy na "kumukuha" ng materyal, habang sa kasabay na paggalaw ay maliit na halaga lamang ang nakukuha bago lumabas ang talim sa hangin. Samakatuwid, ang huling piraso ay madalas na "pumutok" tulad nito. Ito ang dahilan kung bakit ang kabaligtaran ng kilusan ay palaging mas makinis kaysa sa magkasabay na panig.
Aling pamutol para sa kung aling materyal | 1-lead | 2-lead | 3-way | |||
magaspang | panay | magaspang | panay | magaspang | panay | |
mga materyales sa kahoy | ||||||
Softwood (pine) | ++ | 0 | +(+) | 0 | 0 | - |
Solid (oak, beech), playwud, MDF | +(+) | 0 | ++ | 0 | +(-) | - |
mga plastik | ||||||
PVC, Polystyrene, Teflon, Foam | ++ | + | + | 0 | - | -- |
Duroplast, Mga materyales na may bakelite (chipboard) | + | + | ++ | + | + | - |
Bumuhos ang plexiglas | ++ | + | +(+) | - | 0 | - |
Mga metal | ||||||
Malambot na aluminyo (Alucobond) | ++ | + | + | 0 | - | -- |
Matibay na aluminyo (Floxal) | 0 | + | + | ++ | 0 | + |
Mga haluang metal na tanso, tanso, tanso | -- | - | 0 | +(-) | + | ++ |
Structural steel | -- | -- | - | + | - | ++ |
mataas na kalidad na bakal | -- | -- | -- | - | -- | + |
++ Napakahusay + Mabuti 0 Kasiya-siya |
- Masama -- Hindi kasya |
Kapag nagpoproseso ng matitigas na grado ng bakal, 4 o higit pang mga blades ang ginagamit.
Bahagyang o buong paggamit materyal na ito sa pamamagitan lamang ng kasunduan, at may obligadong pagtukoy sa pinagmulan
Sa mga negosyo na kinabibilangan ng mga subdibisyon na nakikibahagi sa pagproseso sa ibabaw ng mga workpiece, batay sa mga normatibong dokumento ang mga espesyal na mapa ay iginuhit, na gumagabay sa operator sa paggawa ng isang partikular na bahagi. Bagaman sa ilang mga kaso (halimbawa, mga bagong kagamitan, mga tool), ang milling operator ay kailangang matukoy ang mga nuances ng mga teknolohikal na operasyon sa kanyang sarili. Kung ang isang mababang-kapangyarihan na makina ay pinatatakbo sa bahay, lalo na, bilang panuntunan, walang mga opisyal na tip sa kamay.
Ang artikulong ito ay makakatulong hindi lamang upang maunawaan ang batayan kung saan ang cutting mode ay kinakalkula sa panahon ng paggiling at ang pagpili ng naaangkop na tool, ngunit nagbibigay din praktikal na payo, na sapat para sa pagproseso ng mga bahagi sa antas ng sambahayan.
Sa mga taong higit pa na nauugnay sa mga metal, para sa isang mas detalyadong kakilala sa mga nuances ng paggiling, dapat kang sumangguni sa aklat-aralin na "Metal Cutting Machines" - 2003, Cherpakov B.I., Alperovich T.A. Ang pamamaraan para sa pagkalkula ng mga kondisyon ng pagputol ay mahusay ding inilarawan sa iba't ibang mga manwal. Halimbawa, sa mga alituntunin mula 2000 (MGAU - Kolokatov A.M., Bagramov L.G.).
Ang kakaiba ng paggiling ay ang mga cutting edge ay direktang nakikipag-ugnay sa materyal na pana-panahon lamang. Bilang resulta - mga panginginig ng boses, pag-load ng shock at pagtaas ng pagsusuot ng mga cutter. Ang pinaka-epektibong mode ay itinuturing na isa kung saan ang mga sumusunod na parameter ay mahusay na pinagsama - lalim, feed at bilis ng pagputol nang hindi nakompromiso ang katumpakan at kalidad ng pagproseso. Ito ang nagbibigay-daan upang makabuluhang bawasan ang gastos ng teknolohikal na operasyon at dagdagan ang pagiging produktibo.
Imposibleng mahulaan nang literal ang lahat ng mga nuances ng paggiling. Ang mga blangko na ipoproseso ay naiiba sa istraktura, sukat at hugis; mga tool sa pagputol - sa pamamagitan ng kanilang geometry, disenyo, presensya / kawalan ng isang proteksiyon na layer, atbp. Ang lahat ng nakasaad sa ibaba sa mga tuntunin ng mga kondisyon ng pagputol ay dapat isaalang-alang lamang bilang isang patnubay. Upang linawin ang mga partikular na parameter ng paggiling, dapat kang gumamit ng mga espesyal na talahanayan at data ng sanggunian.
Pagpili ng kasangkapan
Pangunahing tumutukoy ito sa diameter nito. Ano ang tampok ng pagpili ng cutter () para sa parameter na ito?
- Ang pagtaas ng diameter ay awtomatikong nagpapataas ng halaga ng tool.
- Ang pagtutulungan ng dalawang tagapagpahiwatig - kung ang feed ay tumaas, pagkatapos ay bumaba ang bilis ng pagputol, dahil ito ay limitado ng istraktura ng workpiece (tingnan sa ibaba).
Ang pinakamainam na diameter ng cutter ay itinuturing na tulad na ang halaga nito ay tumutugma (o bahagyang higit pa) sa kinakailangang lalim ng hiwa. Sa ilang mga kaso, maaaring mapili ang mas makapal na mga chip sa 1 pass, ngunit nalalapat lamang ito sa mga materyales na nailalarawan sa mababang density. Halimbawa, polystyrene o ilang uri ng kahoy.
Ang bilis ng pagputol
Depende sa materyal ng sample, maaari kang tumuon sa mga sumusunod na tagapagpahiwatig (m / min):
- kahoy, thermoplastics - 300 - 500;
- PVC - 100 - 250;
- hindi kinakalawang na asero - 45 - 95;
- tanso - 90 - 150;
- tanso - 130 - 320;
- bakelite - 40 - 110;
- aluminyo at mga haluang metal nito - 200 - 420.
Bilis ng pamutol
Ang pinakasimpleng formula ay ganito:
N (bilang ng mga rebolusyon) = 1000 Vc (nais na bilis ng pagputol) / π D (diameter ng pamutol).
Mula sa punto ng view ng kaligtasan, hindi mo dapat itaboy ang spindle sa maximum na bilis. Nangangahulugan ito na dahil lamang dito, ang bilis ng pagputol ay bababa ng mga 10 - 15%. Ang "pagkawala" na ito ay maaaring bahagyang mabayaran sa pamamagitan ng pag-install ng isang pamutol na may mas malaking diameter. Medyo pinapataas nito ang bilis. Kung walang angkop na isa sa kamay, kailangan mong magpasya - upang gumastos ng pera bagong kasangkapan o maging kontento sa mga posibilidad na mayroon ang milling machine. Muli, ang lahat ng ito ay nasuri lamang sa pamamagitan ng pagsasanay ng pagtatrabaho sa mga tiyak na kagamitan, ngunit bait naiintindihan ang rekomendasyon.
Innings
Bigyang-pansin ang parameter ng paggiling na ito!
Ang tibay ng pamutol at ang kalidad ng pagproseso ng workpiece ay nakasalalay sa kung gaano kakapal ang layer ay tinanggal sa isang pagtagos, iyon ay, sa bawat rebolusyon ng spindle. Sa kasong ito, nagsasalita sila ng isang feed ng 1 (2.3) ngipin, depende sa uri ng tool (isa-, dalawa- o tatlong-start cutter).
Ang mga inirerekomendang halaga para sa feed sa bawat ngipin ay tinukoy ng tagagawa ng tool. Ang milling operator sa puntong ito ng cutting regime ay nahaharap sa mga paghihirap kung siya ay nagtatrabaho sa mga cutter na "made in China" o ilang kahina-hinala (hindi kilalang) pinanggalingan. Sa karamihan ng mga kaso, maaari kang tumuon sa hanay ng feed (mm) 0.1 - 0.25. Ang mode na ito ay angkop para sa halos lahat ng karaniwang mga materyales sa paggiling. Sa proseso ng pagputol, magiging malinaw kung ito ay sapat o kaunti upang "idagdag" (ngunit hindi mas maaga kaysa pagkatapos ng unang tawag). Ngunit mas mababa sa 0.1 ay hindi dapat subukan, maliban kapag nagsasagawa ng gawaing alahas gamit ang mga micro-mill.
Simulan ang paggiling na may pinakamababang feed na 0.1. Sa proseso, magiging malinaw kung gaano malleable ang materyal na pinoproseso sa harap ng isang partikular na pamutol. Aalisin nito ang posibilidad na masira ang cutting edge (ngipin) at gagawing posible na makagawa ng tumpak na "diagnosis" ng mga kakayahan ng makina at tool, lalo na kung ito ay "banyagang" kagamitan.
- Ang paglampas sa halaga ng pinakamainam na feed ay puno ng pagtaas ng temperatura sa lugar ng pagtatrabaho, ang pagbuo ng mga makapal na chips at isang mabilis na pagbasag ng pamutol. Para sa isang tool na may diameter na higit sa 3 mm, dapat kang magsimula sa 0.15, hindi na
- Kung hindi posible na madagdagan ang bilis ng paggiling ng isang bahagi dahil sa pinakamainam na paggamit ng mga kakayahan ng kagamitan, maaari mong subukang mag-install ng double-thread cutter.
- Kapag pumipili ng isang tool, dapat itong isaalang-alang na ang pagtaas sa haba ng bahagi ng pagputol ay humahantong sa isang pagbawas sa feed at isang pagtaas sa panginginig ng boses.
- Hindi ka dapat magsikap na dagdagan ang bilis ng pagproseso sa pamamagitan ng pagpapalit ng pamutol ng isang katulad, ngunit may isang malaking bilang ng mga ngipin. Ang mga chips mula sa naturang tool ay mas masahol pa, samakatuwid, madalas itong humahantong sa katotohanan na ang kalidad ng paggiling ay nabawasan nang husto. Sa ilang mga kaso, kapag ang mga grooves ay ganap na napuno, ang pamutol ay nagsisimulang gumana "idle". Walang kwenta ang ganyang kapalit.
Konklusyon
Ang mataas na kalidad na paggiling ay makakamit lamang sa pamamagitan ng karanasan. Tukoy na machine tool + tool + praktikal na karanasan, kasanayan. Samakatuwid, hindi ka dapat bulag na magtiwala kahit sa tabular na data. Halimbawa, hindi nila isinasaalang-alang ang antas ng pagsusuot ng pamutol kung saan gagana. Hindi kailangang matakot na mag-eksperimento, ngunit dapat kang palaging magsimula sa pinakamababang halaga ng mga parameter. Kapag "naramdaman" ng master ang makina, ang pamutol, at ang materyal na pinoproseso, siya mismo ang magpapasiya kung aling mode ito ay nagkakahalaga ng pagtatrabaho.
Bakit mabilis mapurol ang pamutol? Ano ang sanhi ng pagkasunog ng naprosesong materyal (chipboard, MDF o kahoy) pagkatapos ng paggiling? Bakit nasusunog ang pamutol? Paano maiiwasan ang pagdikit ng mga resin sa mga cutting edge ng cutter? Mayroon lamang isang sagot sa mga tanong sa itaas - ang bilis (dalas) ng pag-ikot ng pamutol ay hindi napili nang tama.
Ang mga modernong kagamitan sa paggiling para sa pagproseso ng laminated chipboard o mga materyales sa MDF board ay nilagyan ng mga motor na ginagawang posible upang makamit ang bilis ng spindle na higit sa 20,000 rpm. Sa isang banda, nakakaapekto ito sa pagiging produktibo ng kagamitan, dahil pinapataas nito ang bilis ng tool o ang rate ng feed ng workpiece. Sa kabilang banda, ang kalidad ng pagproseso ay tumataas: ang posibilidad na itaas ang pile sa MDF, ang hitsura ng mga scuffs sa kahoy at mga chips sa laminated chipboard ay nabawasan.
Dahil sa ugali, dahil sa kamangmangan, o dahil lamang sa katamaran, upang hindi mapuno ang iyong ulo ng lahat ng uri ng mga tagubilin sa pagpapatakbo, mga mode ng pagproseso at iba pang mga trick, ang bilis ng pag-ikot ng cutter ay nakatakda sa pinakamataas na antas, kung saan ang lahat ng mga materyales ay naproseso sa lahat ng magagamit na mga cutter. Ito ang kasinungalingan pangunahing dahilan lahat ng problema.
Ang katotohanan ay na sa isang mataas na bilis (dalas) ng pag-ikot ng cutter at isang mababang rate ng feed ng workpiece, ang cutting edge ng cutter karamihan sa oras na ito ay tumatakbo nang walang ginagawa, at sa halip na putulin ang isa pang chip mula sa materyal na pinoproseso, ito ay walang silbi na kuskusin laban dito. Alam ng lahat kung ano ang nangyayari bilang isang resulta ng alitan - pag-init. Bukod dito, mas mataas ang bilis ng pag-ikot ng cutter, mas matindi ang friction, at mas umiinit ang cutter.
Parang may kakaiba? Well, ito ay mainit-init. Kung kukunin mo ito sa iyong palad, kung gayon ang kamay ay magtitiis. Ano ang mangyayari sa metal? Ngunit pa rin…
Bakit nasusunog at mabilis na mapurol ang pamutol
Ang init na nagreresulta mula sa alitan ng mga cutter cutter sa materyal ay unti-unting naipamahagi sa buong katawan nito. Samakatuwid, sa panahon ng panandaliang operasyon, ang pag-init ay halos hindi nararamdaman. Gayunpaman, sa panahon ng pagproseso ng mga materyales, nasa mga cutting edge na ang temperatura ay umabot sa pinakamataas na antas. At mas mataas ang bilis ng pag-ikot ng pamutol, mas malaki ang alitan at pag-init ng mga gilid.
Ito ay lalong kapansin-pansin sa mga cutter na may malaking diameter. Dito bilis ng linya ang paggalaw ng panlabas na bahagi ng cutting edge na may kaugnayan sa materyal ay mas mataas. Bilang isang resulta, ang mga gilid ng pamutol ay uminit at, pagkatapos ng paglamig, dumidilim na may isang mala-bughaw na tint, at ito ay isang tiyak na senyales na ang metal ay pinainit hanggang sa ito ay nagsisimulang baguhin ang mga katangian nito. Sa mga pang-agham na termino, ang bahagi ng carbon ay nasusunog sa metal, na nagbibigay dito ng mga katangian ng katigasan. Kung naaalala mo kung gaano malambot at nababaluktot ang isang ordinaryong kuko, na nasa mainit na uling ng isang hurno o apoy, kung gayon madaling isipin kung anong mga bagong katangian ang makukuha ng pamutol bilang resulta ng sobrang pag-init.
Ito ay nagkakahalaga ng pagdaragdag na kapag pinatalas ang isang pamutol, ang bilis ng pag-ikot ng grinding wheel o disk at ang antas ng presyon ng tool ay direktang nakakaapekto sa pag-init ng mga gilid na pinatalas. Kung hindi ka gumagamit ng coolant, ang anumang carbide metal ay magiging isang ordinaryong piraso ng bakal na maaaring mag-deform pagkatapos maliit na load. Sa pamamagitan ng paraan, iyon ang dahilan kung bakit ang buhay ng pagtatrabaho ng mga cutter, drills at saws pagkatapos ng hasa ay makabuluhang nabawasan.
Bakit nasusunog ang materyal
Ang lahat ay napakalinaw dito: bilang isang resulta ng alitan ng pamutol sa materyal, ang isang mataas na temperatura ay nabuo, sa ilalim ng impluwensya kung saan ang kahoy ay nagsisimulang masunog. Upang maiwasan ang hindi pangkaraniwang bagay na ito, kinakailangan upang bawasan ang bilis (dalas) ng pag-ikot ng pamutol at dagdagan ang rate ng feed ng workpiece. Ngunit ang mga pagkilos na ito ay dapat isagawa sa kondisyon na ang pamutol ay nagpapanatili ng hasa nito. SA kung hindi, ang pagkarga dito, o ang power unit, ay tataas nang malaki, na maaaring humantong sa kanilang pagkasira.
Ang dagta ay dumidikit sa pamutol
Maraming kakahuyan ang naglalaman ng mga dagta. Sa paggawa ng mga materyales sa board wood, tulad ng chipboard at MDF, ang mga formaldehyde resin ay ginagamit bilang karagdagan. Sa proseso ng mekanikal na pagproseso ng mga materyales na ito, na pinainit ng alitan, ang mga particle ng dagta ay kumukulo, nahuhulog sa mga ngipin ng cutting tool at, kasama ng alikabok, dumikit sa kanila. Karaniwan, hindi ito nagiging sanhi ng mga makabuluhang problema kung ang feed mode ng workpiece at ang bilis ng pagputol ng tool ay napili nang tama. Kung hindi man, kapag ang isa sa mga parameter ay hindi kinakalkula nang tama, ang bilis ng pag-ikot ng pamutol ay masyadong mataas at ang pagproseso ay isinasagawa sa isang mababang bilis, ang isang madilim na patong ng resin ay lilitaw sa mga cutter ng tool. Bukod dito, mas malakas ang pagkakaibang ito, mas mabilis itong nabuo. Kasabay nito, bumababa ang kalidad ng pagproseso, lumilitaw ang mga chips sa mga nakalamina na ibabaw, ang kahoy ay nagsisimulang masunog, ang tool ay tumatanggap ng karagdagang pagkarga, mabilis na nag-overheat at nabigo. Ito ang dahilan kung bakit napakahalaga ng pagpili ng bilis ng pamutol at materyal na feed rate.
Bilang karagdagan sa tamang pagkalkula ng mode ng mga materyales sa pagproseso, kinakailangang bigyang-pansin ang pag-aalaga ng cutting tool, iyon ay, upang linisin ang nabuong mga deposito ng dagta sa isang napapanahong paraan, o hugasan ito ng ordinaryong maligamgam na tubig.
Pagkalkula ng bilis (dalas) ng pag-ikot ng pamutol
Upang makagawa ng tamang pagkalkula ng bilis ng pag-ikot ng cutter at ang bilis ng paggalaw nito, kinakailangang isaalang-alang ang maraming mga kadahilanan, kabilang ang mga pisikal at mekanikal na katangian ng materyal at tool, ang lalim at lapad ng pagproseso, atbp.
Sa kabilang banda, ang mga materyales tulad ng MDF at chipboard ay mas madaling iproseso kaysa, halimbawa, iba't ibang mga metal. Samakatuwid, ang batayan ay maaaring kunin lamang bilang isang tagapagpahiwatig ng kalidad ng pagproseso, iyon ay, ang pagkakaroon ng pagkamagaspang, tagaytay, chips at scuffs sa ginagamot na ibabaw.
Para sa higit pa o hindi gaanong mataas na kalidad na pagproseso ng chipboard laminated boards, kinakailangan na ang halaga ng feed sa bawat cutter tooth (o, simple, ang kapal ng mga chips na lumalabas mula sa ilalim ng cutter) ay 0.05 - 0.15 mm. Kaya, ang isang maginoo na dalawang-cutter cutter ay dapat i-cut 0.1 - 0.3 mm bawat rebolusyon, at 1500 - 4500 mm bawat 15,000 revolutions. Iyon ay, ang feed rate ng materyal sa cutter, sa 15,000 rpm, ay dapat na 1.5 - 4.5 m / min, o 25 - 75 mm / s.
Kung gusto mong makina sa mababang rate ng feed, tulad ng kapag nagtatrabaho manu-manong router, pagkatapos ay ang pagkalkula ng bilis ng pag-ikot ng pamutol ay maaaring gawin batay sa bilis ng paggalaw ng router, na gumagawa ng mga kalkulasyon sa reverse order. Sabihin nating naproseso ang materyal sa bilis na 10 mm/sec, o 600 mm/min. Sa rate ng feed bawat ngipin na katumbas ng 0.1 mm at dalawang-cutter cutter, ang kinakailangang bilis ng pag-ikot ng cutter ay magiging 600/(0.1× 2)=3000 rpm.
Mga pag-iingat sa kaligtasan kapag nagtatrabaho sa mga cutter
Bilang isang patakaran, ang mga tagagawa ng mga kagamitan sa paggiling at mga tool ay naglalagay ng mga tagubilin sa kaligtasan sa kanilang mga produkto at ipinapahiwatig ang mga inirekumendang operating mode para sa mga milling cutter. Ipinapakita ng talahanayan sa ibaba ang mga ligtas na parameter para sa bilis ng pag-ikot ng cutter depende sa diameter.
Diametro ng pamutol, mm |
Pinakamataas na bilis ng pag-ikot ng cutter, rpm |
hanggang 25 |
24000 |
26 – 50 |
18000 |
51 – 63 |
16000 |
64 – 75 |
14000 |
76 – 87 |
12000 |
PAGPILI NG CUTTING MODE PARA SA PAGMILING
§ 78. MGA KONDISYON NA NAGTIYAK SA PAGPILI NG CUTTING MODE
Ang konsepto ng pinaka-kapaki-pakinabang na mode ng pagputol
Ang pinaka-kapaki-pakinabang ay dapat isaalang-alang tulad ng isang cutting mode kapag nagtatrabaho sa milling machine, kung saan ang bilis ng pagputol, feed at lalim ng cut layer ay pinakamatagumpay na pinagsama, na nagbibigay, sa ilalim ng mga partikular na kondisyon (ibig sabihin, isinasaalang-alang ang pinakamahusay na paggamit ng mga katangian ng pagputol ng tool, bilis at mga kakayahan ng kapangyarihan ng makina), ang pinakamataas na produktibidad sa paggawa at ang pinakamababang gastos ng operasyon, napapailalim sa tinukoy na mga teknikal na kondisyon sa mga tuntunin ng katumpakan at kalinisan ng pagproseso.
Research Institute of Labor ng State Committee ng Konseho ng mga Ministro ng USSR sa Paggawa at sahod binuo kasama ang pakikilahok ng pinakamalaking domestic scientist, na isinasaalang-alang praktikal na aplikasyon sa mga kondisyon ng produksyon, mga kondisyon ng pagputol kapag nagpapaikut-ikot gamit ang mga tool na gawa sa high-speed na bakal at matitigas na haluang metal. Maaari silang magsilbi bilang paunang data kapag nagtatalaga ng mga bilis ng pagputol at mga minutong feed.
Ang mga pamantayang ito ay makukuha sa bawat planta at nagsisilbing gabay para sa pagpapaunlad teknolohikal na proseso at paggawa ng mga operational chart tulad ng nasa pp. 204-205. Gayunpaman, ang mga bilis ng pagputol at mga minutong feed na ibinigay sa kanila ay hindi nililimitahan at sa ilang mga kaso ay maaaring ma-block ng mga miller kung gumagamit sila ng mas produktibong mga tool o gumagana sa mas malakas at matibay na mga makina.
Sa kabilang banda, ang mga bata, ibig sabihin, mga baguhan at walang sapat na karanasan, ang mga miller ay hindi palaging maaaring gumana sa mga limitasyon ng mga kondisyon ng pagputol, samakatuwid, ang mga hindi gaanong malubhang kondisyon ng pagputol ay ibinibigay para sa kanila sa Handbook ng Young Milling Operator, simula kung saan, ito ay kinakailangan, habang pinapabuti nila ang kanilang mga kasanayan, upang lumipat sa mas mahihigpit.
Upang ikaw mismo ang magpakilala ng mga bagong mode, kailangan mong malaman ang pagkakasunud-sunod at pagkakasunud-sunod ng pagtatakda ng mga milling mode.
Materyal ng pagputol na bahagi ng pamutol
Ang mapagpasyang kadahilanan na tumutukoy sa antas ng cutting mode ay ang materyal ng pagputol na bahagi ng cutter. Tulad ng nabanggit sa itaas, ang paggamit ng mga cutter na may mga carbide insert ay nagpapahintulot sa iyo na magtrabaho sa mataas na bilis ng pagputol at mataas na mga feed kumpara sa mga cutter na gawa sa high speed steel; tulad ng makikita natin sa ibaba, ginagawang posible ng mga carbide cutter na mapataas ang produktibidad ng dalawa hanggang tatlong beses kumpara sa mga high-speed cutter. Samakatuwid, ipinapayong gumamit ng mga carbide cutter para sa halos lahat ng uri ng paggiling; Ang isang balakid sa kanilang paggamit ay maaaring ang hindi sapat na lakas ng kagamitan o ang mga partikular na katangian ng materyal ng workpiece na pinoproseso.
Gayunpaman, sa ilang mga kaso, ang paggamit ng carbon, alloyed tool at high-speed steels para sa cutting part ng milling cutter ay makatuwiran, lalo na kapag ang kalinisan ng machined surface at ang katumpakan ng resultang surface ng bahagi ay mas mahalaga kaysa sa bilis ng trabaho.
Mga geometric na parameter ng bahagi ng pagputol
Ang isang pantay na mahalagang kadahilanan na nakakaimpluwensya sa pagpili ng mga kondisyon ng pagputol ay ang mga geometric na parameter ng pagputol na bahagi ng pamutol (pagputol ng mga anggulo, sukat at hugis ng ngipin), na kadalasang tinatawag cutter geometry. Mas maaga, sa § 7, ang kahulugan at impluwensya ng bawat isa sa mga elemento ng cutter tooth geometry sa proseso ng pagputol ay isinasaalang-alang; dito isasaalang-alang natin ang inirerekumendang geometrical na mga parameter ng cutting part ng mga cutter na gawa sa P18 high-speed steel at may hard alloy plates.
Sa mesa. Ang 35 at 36 ay nagpapakita ng mga inirerekomendang halaga para sa mga geometric na parameter ng cylindrical, end, disk, cut-off, end at shaped cutter na gawa sa high-speed steel.
Talahanayan 35
Mga geometrical na parameter ng cutting part ng mga cutter na gawa sa P18 high-speed steel
I. Mga sulok sa harap

II. Mga sulok sa likod

III. Mga anggulo ng lead at transition

Mga Tala. 1. Para sa mga cylindrical cutter na may anggulo ng ngipin na higit sa 30°, ang anggulo ng rake γ kapag ang machining steel σ b ay mas mababa sa 60 kg/mm 2 ay kinuha katumbas ng 15°.
2. Para sa mga profile cutter na may rake angle na mas malaki sa 0°, kinakailangan ang contour correction kapag gumagawa ng mga tumpak na profile.
3. Kapag nagpoproseso ng mga bakal na lumalaban sa init gamit ang mga end mill, kunin ang mga itaas na halaga ng mga anggulo sa harap, dulo at cylindrical - mas mababa at gitna.
4. Sa likod na ibabaw ng mga cutter, kapag hasa, mag-iwan ng circularly ground tape na may lapad na hindi hihigit sa 0.1 mm. Ang mga ngipin ng slotted (slotted) at detachable (circular saw) cutter ay hinahasa nang hindi nag-iiwan ng ribbon.

Sa mesa. Ang 37 - 40 ay nagpapakita ng mga inirekumendang halaga ng mga anggulo sa harap at likuran, ang pangunahing, auxiliary at mga anggulo ng paglipat sa plano, ang mga anggulo ng pagkahilig ng cutting edge at helical grooves, ang radius sa tuktok ng mukha, cylindrical, end at disk cutter na may mga carbide insert.
Ang mga cutter na ginagamit upang iproseso ang karamihan sa mga workpiece ay karaniwang ibinibigay ng mga pabrika ng tool na may mga geometric na parameter na sumusunod sa GOST, at halos imposible para sa isang milling machine, hindi tulad ng isang turner at planer, na baguhin ang mga anggulo ng pagputol ng mga cutter sa pamamagitan ng hasa. Bilang isang resulta, ibinigay sa talahanayan. 35 - 40 ang mga geometrical na parameter ng cutting part ng milling cutter ay makakatulong sa milling operator na piliin nang tama ang naaangkop na milling cutter mula sa standard cutter na available sa tool pantry ng training at production workshop. Gayunpaman, ang pangunahing layunin ng mga talahanayan na ito ay upang magbigay ng mga rekomendasyon kung sakaling ang miller mismo ay gustong mag-order ng standard o espesyal na mga milling cutter na may pinakamainam na geometric na mga parameter para sa pagproseso na ito.
Talahanayan 37
Mga geometric na parameter ng cutting part ng end mill na may mga carbide insert

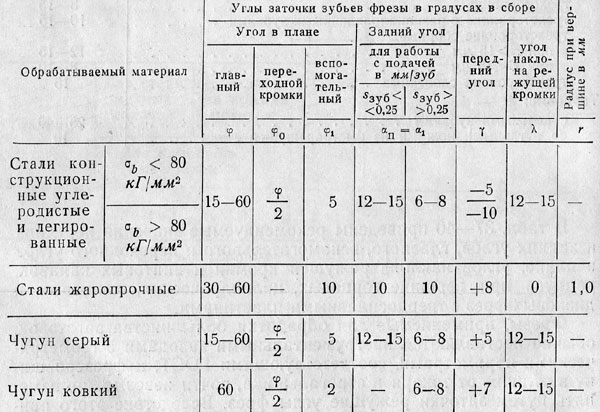
Tandaan. Ang mga maliliit na anggulo ng lead φ = 15 - 30° ay dapat gamitin kapag nag-machining sa mga matibay na makina para sa mga roughing pass na may maliit na lalim ng cut o finishing pass na may mababang mga kinakailangan para sa kalinisan at katumpakan sa machined na ibabaw.
Talahanayan 38
Mga geometrical na parameter ng cutting part ng cylindrical cutter na may helical blades ng hard alloy


Tandaan. Sa likod na ibabaw ng ngipin kasama ang cutting edge, isang laso na may lapad na hindi hihigit sa 0.1 mm.
Talahanayan 39
Mga geometric na parameter ng pagputol ng bahagi ng mga end mill na may mga pagsingit ng tungsten carbide sa pagproseso ng mga istrukturang carbon at haluang metal na bakal


* Sa mababang tigas ng makina ng system - kabit - tool - bahagi at may malalaking seksyon ng chip ( SA higit pa D; t higit sa 0.5 D), pati na rin kapag nagtatrabaho kasama mababang bilis pagputol sa hindi sapat na bilis ng spindle ( v mas mababa sa 100 m/min) ang anggulo ng rake γ ay itinalagang positibo + mula 0 hanggang +8°.
** Mas malalaking halaga para sa banayad na bakal, mas maliit na halaga para sa matitigas na bakal.
Lapad at lalim ng paggiling
Lapad ng paggiling tinukoy sa pagguhit ng bahagi. Sa kaso ng pagproseso ng ilang mga workpiece na naka-clamp nang magkatulad sa isang clamping device, ang lapad ng milling ay katumbas ng lapad ng lahat ng workpieces. Sa kaso ng paggiling na may mga hanay ng mga milling cutter, ang lapad ng paggiling ay katumbas ng kabuuang lapad ng lahat ng mga ibabaw ng isinangkot.
Lalim ng paggiling(depth of cut, cut layer thickness) ay ibinibigay bilang distansya sa pagitan ng machined at machined surface. Upang mabawasan ang oras ng pagproseso, inirerekomenda na magsagawa ng paggiling sa isang pass. Sa pagtaas ng mga kinakailangan para sa katumpakan at kalinisan ng machined surface, ang paggiling ay isinasagawa sa dalawang yugto - roughing at pagtatapos. Sa ilang mga kaso, kapag nag-aalis ng malalaking allowance o kapag nagpapaikut-ikot sa mga makina na walang sapat na kapangyarihan, ang pagproseso sa dalawang roughing pass ay posible.
Talahanayan 40
Mga geometric na parameter ng pagputol ng bahagi ng mga disc cutter na may mga carbide insert


Kapag ang paggiling ng mga forging ng bakal, bakal at cast iron castings na natatakpan ng scale, foundry crust o kontaminado ng foundry sand, ang lalim ng paggiling ay dapat na mas malaki kaysa sa kapal ng kontaminadong layer upang ang mga ngipin ng cutter ay hindi mag-iwan ng mga itim na hiwa sa machined surface, dahil ang pag-slide sa kahabaan ng crust ay negatibong nakakaapekto sa cutter, na nagpapabilis sa pagkasira ng pagputol.
Para sa pinakakaraniwang mga kaso ng paggiling, inirerekumenda na magsagawa ng roughing sa bakal na may lalim na hiwa ng 3-5. mm, at sa bakal at cast iron- may cutting depth 5-7 mm. Para sa pagtatapos ng paggiling kumuha ng cutting depth na 0.5-1.0 mm.
diameter ng pamutol
Ang diameter ng pamutol ay pinili higit sa lahat depende sa lapad ng paggiling SA at lalim ng hiwa t. Sa mesa. Ipinapakita ng 41 ang data para sa pagpili ng mga cylindrical cutter, sa talahanayan. 42 - end mill at nasa talahanayan. 43 - mga pamutol ng disk.

* Gumamit ng mga prefabricated compound cutter ayon sa GOST 1979-52.


Isaalang-alang ang epekto ng diameter ng pamutol sa pagganap ng paggiling.
Ang diameter ng cylindrical cutter ay nakakaapekto sa kapal ng cut: mas malaki ang diameter ng cutter D mas manipis ang hiwa; na may parehong supply s ngipin at lalim ng paggiling t.
Sa fig. Ang 327 ay nagpapakita ng isang hiwa na nakuha na may parehong lalim ng paggiling t at paghahain s ngipin, ngunit may iba't ibang diameter ng mga pamutol. Ang hiwa na nakuha na may mas malaking diameter ng pamutol (Larawan 327, a) ay may mas maliit na kapal kaysa sa hiwa na may mas maliit; diameter ng pamutol (Larawan 327, b).

Dahil ang tiyak na presyon ay tumataas na may pagbaba sa kapal ng cut layer A naib (tingnan ang Talahanayan 38), ito ay mas kumikita upang gumana sa mas makapal na hiwa, ibig sabihin, ceteris paribus, na may mas maliit na diameter ng pamutol.
Ang diameter ng cutter ay nakakaapekto sa dami ng landas na ang cutter ay dapat maglakbay sa isang pass.
Sa fig. Ipinapakita ng 328 ang landas na dapat dumaan ng cutter kapag pinoproseso ang isang bahagi na may haba L; sa fig. 329 - ang landas kung saan dapat dumaan ang face mill sa asymmetrical milling ng isang workpiece na may haba L; sa fig. 330 - ang landas na dapat dumaan ng pamutol ng cake kapag simetriko ang paggiling ng workpiece na may haba L.

Halaga ng infeed l(cut-in path):
kapag nagtatrabaho sa cylindrical, disc, cut-off at hugis cutter ay depende sa diameter ng cutter D lalim ng paggiling t at ipinapahayag ng pormula
kapag nagtatrabaho sa mga end mill at end mill para sa asymmetrical milling ay depende sa diameter ng cutter D lapad ng paggiling SA at ipinapahayag ng pormula
kapag nagtatrabaho sa mga face mill kapag ang simetriko na paggiling ay nakasalalay sa diameter ng pamutol D lapad ng paggiling SA at ipinapahayag ng pormula
Overrun value l 1 ay pinili depende sa diameter ng pamutol sa loob ng 2-5 mm.
Samakatuwid, upang mabawasan ang landas ng pagpasok at pag-overrun ng pamutol, ibig sabihin, upang mabawasan ang kawalang-ginagawa ng makina, ipinapayong pumili ng mas maliit na diameter ng pamutol.
Sa dulo ng libro, sa mga appendice 2 at 3, mayroong mga talahanayan ng mga halaga para sa plunge path at overrun ng mga cutter.
Ang diameter ng pamutol ay nakakaapekto sa halaga metalikang kuwintas: mas maliit ang diameter ng cutter, mas kaunting torque ang dapat ibigay sa spindle ng makina.
Kaya, ang pagpili ng isang pamutol na may mas maliit na diameter ay tila mas angkop. Gayunpaman, na may pagbaba sa diameter ng pamutol, kinakailangan na pumili ng isang thinner, ibig sabihin, hindi gaanong matibay na milling mandrel, kaya kinakailangan upang bawasan ang pagkarga sa mandrel, ibig sabihin, upang mabawasan ang cross section ng cut layer.
Innings
Pakanin sa magaspang depende sa materyal na pinoproseso, ang materyal ng pagputol na bahagi ng pamutol, ang lakas ng drive ng makina, ang katigasan ng makina ng system - kabit - tool - bahagi, mga sukat ng pagproseso at mga anggulo ng pagpapatalas ng pamutol.
Pakanin sa pagtatapos depende sa klase ng kalinisan sa ibabaw na ipinahiwatig sa pagguhit ng detalye.
Ang pangunahing input kapag pumipili ng feed para sa rough milling ay ang feed s ngipin.
Para sa mga face mill na may pagpili ng feed s ang ngipin ay nagbibigay ng isang paraan upang i-install ang cutter na may kaugnayan sa workpiece, na tumutukoy sa anggulo ng cutter tooth meeting sa workpiece at ang kapal ng cut chips sa pagpasok at paglabas ng cutter tooth mula sa contact sa workpiece. Ito ay itinatag na para sa isang pamutol ng karbid ng mukha, ang pinaka-kanais-nais na mga kondisyon para sa pagputol ng isang ngipin sa isang workpiece ay nakamit kapag ang pamutol ay matatagpuan na may kaugnayan sa workpiece, tulad ng sa Fig. 324, c, ibig sabihin, kapag ang pamutol ay na-offset na may kaugnayan sa workpiece sa pamamagitan ng isang halaga SA = (0,03 - 0,05)D. Ang ganitong offset ng cutter axis ay ginagawang posible upang madagdagan ang feed sa bawat ngipin laban sa feed sa panahon ng simetriko na paggiling (Fig. 324, a) ng cast iron at steel sa pamamagitan ng isang kadahilanan na dalawa o higit pa.
Sa mesa. Ipinapakita sa talahanayan 44 ang mga inirerekomendang feed para sa magaspang na paggiling na may carbide face mill para sa dalawang kaso na ito.

Mga Tala. 1. Ang roughing feed rate na ipinapakita ay batay sa mga karaniwang milling cutter. Kapag nagtatrabaho sa hindi karaniwang mga cutter na may mas mataas na bilang ng mga ngipin, ang mga halaga ng feed ay dapat bawasan ng 15 - 25%.
2. Sa paunang panahon ng pagpapatakbo ng pamutol hanggang sa pagsusuot ng katumbas ng 0.2-0.3 mm, ang kalinisan ng machined surface sa panahon ng fine milling ay nababawasan ng halos isang klase.

Tandaan. Kumuha ng malalaking feed para sa mas maliliit na lalim ng hiwa at lapad ng pagproseso, mas maliliit na feed para sa malalaking lalim at lapad ng pagproseso.

Tandaan. Ang mga feed ay ibinibigay para sa isang matibay na sistema ng makina - kabit - kasangkapan - bahagi.
Sa paggiling ng mukha gamit ang mga carbide cutter, ang anggulo ng lead φ ay nakakaapekto rin sa rate ng feed. Ang mga isinumite ay ibinigay sa talahanayan. Ang 44 ay idinisenyo para sa mga cutter na may φ = 60 - 45°. Ang pagbabawas ng anggulo ng lead φ hanggang 30° ay nagbibigay-daan sa iyong dagdagan ang feed ng 1.5 beses, at ang pagtaas ng anggulo φ hanggang 90° ay nangangailangan ng 30% na pagbawas sa feed.
Mga feed para sa pagtatapos gamit ang mga carbide cutter na ibinigay sa Table. 44 ay ibinibigay para sa isang rebolusyon ng cutter, dahil ang mga feed sa bawat ngipin ay masyadong maliit. Ang mga feed ay ibinibigay depende sa klase ng kalinisan ng ginagamot na ibabaw alinsunod sa GOST 2789-59.
Sa mesa. 45 ay nagpapakita ng inirerekomendang feed sa bawat cutter tooth para sa magaspang na paggiling ng mga eroplano na may cylindrical, mukha at disk tatsulok na pamutol mula sa high-speed steel R18.
Sa mesa. 46 ay nagpapakita ng mga feed habang tinatapos ang paggiling ng mga eroplano na may mga cylindrical cutter na gawa sa P18 high-speed na bakal, at nasa mesa. 47 - kapag tinatapos ang paggiling ng mga eroplano na may mukha at disk na may tatlong panig na mga cutter na gawa sa P18 high-speed na bakal. Dahil sa maliit na halaga ng feed sa bawat ngipin ng cutter, na nakuha sa panahon ng pinong paggiling, sa talahanayan. Ang 46 at 47 ay mga feed sa bawat rebolusyon ng cutter.
Dapat tandaan na gumagana sa mga feed na nakasaad sa Talahanayan. 44-47, naglalagay ng isang kailangang-kailangan na kondisyon para sa pagkakaroon ng isang minimum na runout ng mga ngipin ng cutter (tingnan ang talahanayan. 50).

Tandaan. Ang mga feed ay ibinibigay para sa isang matibay na sistema ng makina - kabit - kasangkapan - bahagi kapag nagpapaikut-ikot gamit ang mga milling cutter na may pantulong na anggulo sa plano φ 1 = 2 °; para sa mga cutter na may φ 1 = 0 feed ay maaaring tumaas ng 50 - 80%.