بهدسته بندی:
کار آسیاب
انتخاب حالت های آسیاب منطقی
انتخاب حالت فرز منطقی در یک ماشین معین به این معنی است که برای شرایط پردازش داده شده (مواد و درجه قطعه کار، مشخصات و ابعاد آن، هزینه پردازش)، لازم است نوع و اندازه بهینه برش، درجه مواد انتخاب شود. و پارامترهای هندسی قسمت برش کاتر، مایع روان کننده و خنک کننده و تعیین مقادیر بهینه برای پارامترهای حالت برش زیر: B, t, sz. v، p، Ne، Tm.
از فرمول (32) نتیجه می شود که پارامترهای B، t، sz و v تأثیر یکسانی بر بهره وری آسیاب حجمی دارند، زیرا هر یک از آنها تا درجه اول در فرمول گنجانده شده است. این بدان معنی است که اگر هر یک از آنها مثلاً با ضریب دو افزایش یابد (در حالی که سایر پارامترها بدون تغییر باقی می مانند) بهره وری حجمی نیز دو برابر می شود. با این حال، این پارامترها تأثیر یکسانی بر عمر ابزار ندارند (به بند 58 مراجعه کنید). بنابراین، با در نظر گرفتن عمر ابزار، قبل از هر چیز، سودآورتر است که حداکثر مقادیر مجاز آن دسته از پارامترها را انتخاب کنید که تأثیر کمتری بر عمر ابزار دارند، یعنی به ترتیب زیر: عمق برش، تغذیه در هر دندان و سرعت برش بنابراین، انتخاب این پارامترهای حالت برش هنگام فرز بر روی این دستگاه باید به همان ترتیب شروع شود، یعنی:
1. عمق برش بسته به کمک هزینه پردازش، الزامات برای زبری سطح و قدرت ماشین اختصاص داده می شود. توصیه می شود با در نظر گرفتن قدرت دستگاه، کمک هزینه پردازش را در یک گذر حذف کنید. به طور معمول، عمق برش در طول فرز خشن از 4-5 میلی متر تجاوز نمی کند. هنگام خشن کردن با فرز صورت برش کاربید(سر) در ماشین های فرز قدرتمند می تواند به 20-25 میلی متر یا بیشتر برسد. هنگام اتمام فرز، عمق برش از 1-2 میلی متر تجاوز نمی کند.
2. حداکثر خوراک مجاز تحت شرایط پردازش اختصاص داده شده است. هنگام تعیین حداکثر خوراک های مجاز، باید از خوراک های هر دندان که نزدیک به "شکستن" هستند استفاده شود.
آخرین فرمول وابستگی خوراک به ازای هر دندان را به عمق آسیاب و قطر کاتر بیان می کند. مقدار حداکثر ضخامت برش، یعنی مقدار ضریب ثابت Ic در فرمول (21)، به خواص فیزیکی و مکانیکی ماده در حال پردازش بستگی دارد (برای یک نوع و طراحی معین از برش). مقادیر حداکثر خوراک های مجاز توسط عوامل مختلفی محدود می شود:
الف) در هنگام خشن کردن - سفتی و مقاومت در برابر لرزش ابزار (با سفتی و مقاومت کافی در برابر لرزش دستگاه)، سفتی قطعه کار و استحکام قسمت برش ابزار، به عنوان مثال، دندان برش، حجم ناکافی. فلوت های تراشه ای، به عنوان مثال، برای برش های دیسک و غیره. بنابراین، تغذیه به ازای هر دندان هنگام آسیاب کردن فولاد خشن با برش های استوانه ای با چاقوهای داخلی و دندانه های بزرگ در محدوده 0.1-0.4 میلی متر بر دندان انتخاب می شود، و هنگام پردازش چدن. تا 0.5 میلی متر / دندان؛
ب) در طول پردازش تکمیل - زبری سطح، دقت ابعاد، وضعیت لایه سطحی، و غیره. هنگام تکمیل فرز فولاد و چدن، تغذیه نسبتا کمی برای هر دندان کاتر اختصاص داده می شود (0.05-0.12 میلی متر / دندان).
3. سرعت برش تعیین می شود. از آنجایی که او بیشترین را دارد نفوذ بزرگدر مورد دوام ابزار، سپس بر اساس استاندارد دوام پذیرفته شده برای این ابزار انتخاب می شود. سرعت برش با فرمول (42) یا از جداول استانداردهای حالت برش بسته به عمق و عرض فرز، تغذیه در هر دندان، قطر برش، تعداد دندانه ها، شرایط خنک کننده و غیره تعیین می شود.
4. توان برش موثر Ne برای حالت انتخاب شده با استفاده از جداول استانداردها یا فرمول (39a) تعیین و با توان دستگاه مقایسه می شود.
5. توسط سرعت را تنظیم کنیدبرش (i، یا i^)، نزدیکترین سطح سرعت اسپیندل ماشین از میان سطوح موجود در یک ماشین معین با استفاده از فرمول (2) یا مطابق نمودار (شکل 174) تعیین می شود. از نقطه مربوط به سرعت برش پذیرفته شده (مثلاً 42 متر در دقیقه) انجام دهید خط افقی، و از نقطه ای با علامت قطر برش انتخاب شده (به عنوان مثال، 110 میلی متر) - عمودی. در نقطه تلاقی این خطوط، نزدیکترین سطح سرعت اسپیندل تعیین می شود. بنابراین، در مثال نشان داده شده در شکل. 172، هنگام فرزکاری با کاتر به قطر D = 110 میلی متر با سرعت برش 42 متر در دقیقه، سرعت چرخش دوک برابر با 125 دور در دقیقه خواهد بود.
شکل 174 نوموگرام سرعت چرخش کاتر
6. خوراک دقیقه با استفاده از فرمول (4) و یا بر اساس برنامه (شکل 175) تعیین می شود. بنابراین، هنگام آسیاب با کاتر D = 110 میلی متر، z = 10 در sz = 0.2 میلی متر / دندان و n = 125 دور در دقیقه، تغذیه دقیقه طبق برنامه به شرح زیر تعیین می شود. از نقطه مربوط به تغذیه به ازای هر دندان sg = 0.2 میلی متر / دندان، رسم می کنیم خط عمودیتا زمانی که با یک خط شیبدار مطابق با تعداد دندانه های برش r = 10 قطع شود. از نقطه به دست آمده یک خط افقی ترسیم می کنیم تا با یک خط شیبدار مطابق با سرعت دوک پذیرفته شده l = 125 rpm قطع شود. سپس یک خط عمودی از نقطه به دست آمده بکشید. نقطه تلاقی این خط با مقیاس پایینتر تغذیههای دقیقهای موجود در یک ماشین مشخص، نزدیکترین مرحله تغذیه دقیقهای را تعیین میکند.
7. زمان ماشین تعیین می شود.
زمان ماشین. زمانی که فرآیند براده برداری بدون مشارکت مستقیم کارگر انجام می شود، زمان ماشین نامیده می شود (به عنوان مثال، برای آسیاب کردن صفحه قطعه کار از لحظه روشن شدن تغذیه طولی مکانیکی تا خاموش شدن آن).
برنج. 1. نوموگرام خوراک دقیقه
افزایش بهره وری در هنگام پردازش در ماشین های برش فلز توسط دو عامل اصلی محدود می شود: قابلیت های تولید دستگاه و ویژگی های برش ابزار. اگر قابلیت های تولید دستگاه کم باشد و اجازه استفاده کامل از خواص برشی ابزار را ندهد، بهره وری چنین دستگاهی تنها بخش کوچکی از بهره وری ممکن با حداکثر استفاده از ابزار خواهد بود. در شرایطی که قابلیت های تولید دستگاه به طور قابل توجهی از خواص برش ابزار فراتر رود، حداکثر بهره وری ممکن با یک ابزار معین را می توان بر روی دستگاه به دست آورد، اما از قابلیت های دستگاه به طور کامل استفاده نخواهد شد، یعنی قدرت ماشین، حداکثر نیروهای برش مجاز و غیره د. بهینه از نظر بهره وری و استفاده اقتصادی از ماشین و ابزار مواردی خواهد بود که ظرفیت تولید ماشین و خواص برش ابزار با هم منطبق باشند یا نزدیک به هم.
این شرط مبنایی برای به اصطلاح ویژگی های تولید ماشین ها است که توسط پروفسور پیشنهاد و توسعه داده شد. A.I. کاشیرین. مشخصه تولید یک ماشین نموداری از قابلیت های ماشین و ابزار است. ویژگی های تولید، تعیین شرایط بهینه برش را در هنگام پردازش در یک ماشین مشخص آسان تر و ساده تر می کند.
ویژگی های برش یک ابزار خاص با حالت های برش مجاز در طول فرآیند پردازش مشخص می شود. سرعت برش در شرایط پردازش داده شده را می توان با فرمول (42، a) تعیین کرد. در عمل، آن را از جدول حالت های برش، که در کتاب های مرجع استانداردساز یا فناور آورده شده است، پیدا می کنیم. با این حال، باید توجه داشت که استانداردهای حالت های برش هم برای آسیاب و هم برای انواع دیگر پردازش بر اساس خواص برش ابزار برای موارد مختلففرآوری (نوع و اندازه ابزار، نوع و درجه مواد قطعه برش، مواد در حال پردازش و غیره)، و مربوط به ماشین هایی که فرآوری بر روی آنها انجام می شود نیست. از آنجایی که قابلیتهای تولید ماشینهای مختلف متفاوت است، حالت پردازش بهینه عملاً عملی در ماشینهای مختلف برای شرایط پردازش یکسان متفاوت خواهد بود. قابلیت های تولید ماشین ابزار در درجه اول به قدرت موثر ماشین، سرعت چرخش، تغذیه و غیره بستگی دارد.
برنج. 2. غوطه ور شدن و سفر بیش از حد
مشخصات تولید فرز برش برای مورد برش فرز توسط پروفسور A. I. Kashirin و نویسنده توسعه داده شد.
اصل ساخت مشخصات تولید ماشین های فرز (نوموگرام) برای کار با آسیاب های انتهایی بر اساس یک اتصال است. راه حل گرافیکیدو معادله که وابستگی سرعت برش vT را طبق فرمول (42) در -Bz' = const از یک سو و سرعت برش و توان مجاز دستگاه از سوی دیگر مشخص میکند. سرعت برش vN را می توان با فرمول تعیین کرد
برنج. 3. مشخصات تولید دستگاه فرز کنسول 6P13
حالت های برش
برش های دست چپ
چرا در مقابل آسیاب خوراک بهتر است.مسئله:کاتر 2 فلوت فوم پی وی سی را ذوب می کند.
راه حل:تعداد دور کمتری را انتخاب کنید یا با یک برش تک رشته آسیاب کنید. (تصویر)
1. شیرجه:
کاتر باید بتواند با انتهای خود به مواد نفوذ کند (عملکرد حفاری).
2. لبه برش:
به عنوان یک قاعده، لبه های گذرگاه با یکدیگر متفاوت هستند. طرف مقابل حرکت "زیباتر" از سمت همزمانی است. این امر به ویژه هنگام استفاده از کاتر 1 فلوت و همچنین هنگام آسیاب آلومینیوم قابل توجه است.
مشاوره؛خطوط داخلی را در جهت عقربه های ساعت آسیاب کنید، خطوط بیرونی را در خلاف جهت عقربه های ساعت. بنابراین طرف "بد" به تراشه ها ختم می شود
3. حذف تراشه:
تراشه ها باید به سرعت تخلیه شوند تا حفره های کاتر پر نشود و باعث شکستن کاتر شود. هر چه فرز عمیق تر و سریعتر اتفاق بیفتد، برداشتن تراشه ها دشوارتر می شود. دستور العمل: قطر برش را بیشتر از دو یا سه برابر نکنید. در چندین گذر از شیارهای عمیق تر عبور کنید. هنگام آسیاب پلی استایرن و سایر پلاستیک ها، استفاده از برش هایی با شیارهای صیقلی برای خروجی بهتر منطقی است.
4. اتلاف گرما/روغنکاری:
برش نباید خیلی داغ شود: از یک طرف، ابزاری با دمای خیلی بالا خواص خود را از دست می دهد، از طرف دیگر - حتی مهم تر - تراشه های پلاستیکی و آلومینیومی می توانند در شیارها "چسبیده" شوند و از برداشتن تراشه ها جلوگیری کنند. و در نتیجه منجر به شکستن کاتر می شود. هنگام پردازش فلزات، توصیه یک روان کننده ضروری است. توجه: آلومینیوم و فلزات غیرآهنی را می توان با الکل یا امولسیون های مخصوص آسیاب کرد؛ هنگام پردازش پلکسی می توان از آب صابون استفاده کرد.
5. خطر شکستگی:
با افزایش خوراک و افزایش عمق غوطه وری به صورت خطی رشد می کند: تغذیه مضاعف به معنای خطر کسری مضاعف است، عمق غوطه وری مضاعف به معنای خطر کسری هشت برابری است.
جهت ها:
بهتر است آسیاب در چند پاس در عمق کمتر و با سرعت تغذیه بالاتر انجام شود. از یک بیت روتر با کوتاه ترین طول برش ممکن استفاده کنید. تا حد امکان آن را سفت کنید. قانون کلی: یک سوم در چاک گیره می شود (چک کولت) طول کلبرش دهنده ها
برش سمت راست تراشه ها را به بالا می آورد.
کاتر دست راست برداشتن تراشه ها را به سمت بالا تسهیل می کند، که برای برداشتن مداوم خوب است؛ با این حال، این عیب را دارد که کاتر، مانند یک پیچ چوب پنبه، مواد پایه (قطعه کار) را به سمت بالا حرکت می دهد، هنگام آسیاب می چرخد. چوب یا "دفن" در هنگام پردازش مواد ورق نازک (به عنوان مثال قلع). از طرف دیگر یک کاتر با مارپیچ سمت چپ، مواد را به سمت پایین فشار میدهد و هنگام مسیریابی مواد الیافی مانند چوب یا مقوا، به لبه بالایی صافتری دست مییابید (الیاف بلند نمیشوند، بلکه به مواد پایه فشار داده میشوند). اما در اینجا عامل منفی دشواری حذف تراشه ها است.
توجه داشته باشید:
در موارد استاندارد از کاتر دست راست استفاده کنید.
برش های دست چپ برای برش های کم عمق مفید هستند مواد نازک، جایی که خطر "دفن کردن" و تکان دادن قطعه کار نخ سمت راست به سمت بالا زیاد است. با این حال، هر چه موادی که استفاده می کنید سخت تر باشد، زودتر می توانید کاتر مارپیچ سمت چپ را رها کنید.
الف. برش دست راست (شکل معمولی):
براده ها را به بالا بیاورید. کاتر تمایل به "نقف کردن" و بلند کردن مواد پایه دارد.
"اثر پیچ چوب پنبه"
ب. مارپیچ سمت چپ (شکل خاص): تراشه ها را هنگام ماشینکاری از انتها به سمت پایین هدایت می کند، یا هنگام کار در حفره ای که قبلا آسیاب شده استفاده می شود. کاتر مواد پایه را فشار می دهد (برعکس "اثر چوب پنبه").
برای آسیاب عمیق مناسب نیست.
نوع کاتر: 1 یا 2 تیغه؟
تعداد بی نهایت کاتر وجود دارد، اما اساساً ما بین تیز و کسل کننده تمایز قائل می شویم. هرچه تیغه تیزتر باشد، نوک آن سریعتر فرسوده می شود.قانون کلی:هر چه استحکام مواد بیشتر باشد، تیغه باید صاف تر باشد. این تیز کردن برای فلزات سخت (مثلاً برنج) مناسب است. تیزتر دم ماهی برای پلاستیک، چوب و آلومینیوم نرم. تیغه ها قسمت های سایش کاتر هستند. در کاترهای با بیش از یک تیغه، بار توزیع شده و دوام افزایش می یابد. این کاترها در مواد سخت (مثلاً فولاد ضد زنگ) سریعتر کار می کنند و لرزش کمتری دارند. تیغه های متعدد - تحت شرایط آسیاب یکسان - براده های نازک تری تولید می کنند که در نتیجه سطح صاف تری ایجاد می شود.
انتخاب نوع "ایده آل" برش همیشه به مواد در حال پردازش بستگی دارد:
هنگام آسیاب کردن مواد "نرم":پلاستیک های نرم (PVC، پلکسی گلاس، فوم پلی استایرن)، مواد چوبی (چوب، تخته فیبر، تخته سه لا، نئوپان)، گریدهای نرم آلومینیوم و ساندویچ ها (آلومینیوم / پلاستیک) از برش های تیز 1 فلوت بهره می برند. از آنجایی که در اینجا مشکل مات شدن سریعتر به خطر گرفتگی و شکستگی کاتر ارجحیت دارد.
برای پلاستیک های سختتیزی های دو طرفه با پروفیل دم ماهی مناسب هستند.
هنگام ماشینکاری فلزات سخت ترمانند برنج، ما می توانیم کاترهای 2 فلوت را با آسیاب صاف توصیه کنیم.
هنگام آسیاب کردن فولاد ساختاری بسیار سفت و سختیا فولاد بسیار مرغوب، از سه یا چهار کاتر ورودی استفاده کنید.
تک برش در مقطع
یک چاقو یک فضای باز بزرگ را ترک می کند
برای حذف تراشه ها
کاتر سه فلوت در مقطع
سه تیغه به طور قابل توجهی فضا را کاهش می دهد
برای حذف تراشه ها
تفاوت بین کاتر و حکاکی
بسیاری از مردم از اصطلاحات "کاتر" و "حکاک" به جای یکدیگر استفاده می کنند. با این حال، ما در مورد دو ابزار متفاوت صحبت می کنیم.
حکاکی ابزار ساده ای است که یک استوانه را به دو نیم می کند و به دنبال آن یک ساییدن پشتی انجام می شود.
شکل ممکن است متفاوت باشد. رایج ترین آنها مثلثی هستند. بر خلاف فرزها، آنها لوله مارپیچ برای تخلیه تراشه ندارند.
مواد برش: HSS یا کاربید؟
در فناوری تبلیغات، برش کاربید عمدتا استفاده می شود.
کاربید (HM) یک محصول گران قیمت و ساخته دست بشر است که از پودرهای ریز (به عنوان مثال Wolfram-Carbid) آگلومره شده است. در طی فرآیند تراکم، شکل کاتر بلافاصله ایجاد می شود و متعاقباً تغییر نمی کند (فقط تیز می شود). کاربید بسیار سخت و مقاوم در برابر سایش است، با این حال، مستعد لرزش و ضربه است. هنگام استفاده از برشهای HM داشتن یک دستگاه پایدار، احتمالاً سنگینتر و حجیمتر، یک دوک با چرخش دقیق و کلتهای گیره با کیفیت بالا مهم است. ماده ای که قرار است آسیاب شود باید به طور صلب و بدون حرکت روی دستگاه ثابت شود.
فولاد سرعت بالا (HSS) عمدتاً در مواردی استفاده می شود که کاربید بسیار حساس است: هنگام آسیاب ورق های فولادی ضد زنگ، در ماشین های لرزان، یا در مواردی که سفتی گیره به اندازه کافی تضمین نمی شود. HSS خیلی سریعتر فرسوده می شود، اما به دلیل ویسکوزیته، خطر خرابی زودرس کمتری وجود دارد.
عمر یک برش HSS روکش شده به طور قابل توجهی افزایش می یابد. به عنوان مثال، نیترید تیتانیوم (TiN) عمر مفید را شش برابر افزایش می دهد.
Titan-Nitrid به طور قابل توجهی سفت تر از HSS و همچنین سخت تر از HM است. با پوشش Titan-Nitrid، ابزار HM نیز دوام بیشتری دارند، اگرچه تفاوت در سختی ناچیز است.
پوشش تاثیر مهم تری بر تعداد دور و تغذیه دارد. می توان آن را افزایش داد و در نتیجه زمان پردازش را می توان کوتاه کرد. هنگام آسیاب آلومینیوم، TiN از پخت وحشتناک آلومینیوم در کاتر جلوگیری می کند. روکش مانند تفلون در ماهیتابه عمل می کند (چیپس ها کشویی می شوند)
سرعت و تغذیه بهینه
مهمترین پارامتر در هنگام آسیاب تعداد دور و تغذیه است. داده های جدول با اکثر توصیه های تولید کنندگان برش مطابقت دارد. (اگر شک دارید، از تامین کننده خود بپرسید که چه حالت هایی را برای محصول خود توصیه می کنند.)ابتدا سرعت برش توصیه شده برای ماده در حال پردازش را در نظر بگیرید و آن را در فرمول برای محاسبه تعداد دور اعمال کنید.
اگر از یک ماشین نه چندان سفت استفاده شود، تعداد دورها در ناحیه بالا و تغذیه در ناحیه پایین تعیین می شود. اگر تعداد دورها مشخص باشد، تغذیه با استفاده از فرمول محاسبه می شود.
اساساً در نظر گرفته می شود: هر چه سرعت برش بیشتر باشد (vc = p * d * n)، سطح صاف تر خواهد بود. اما با افزایش سرعت برش، تیرگی کاتر نیز افزایش می یابد.
روش محاسبه:
1. تعداد انقلاب n:
سرعت برش را انتخاب کنید vcاز روی میز (اگر سرعت برش مواد بسیار متفاوت است، با کتاب های مرجع بررسی کنید).
بر اساس داده ها، سرعت اسپیندل را محاسبه کنید
N = (vc *1000) / (3.14 * d)
F = n * fz * z
fz = تغذیه برای هر دندان
z = تعداد تیغه ها
مثال:
شما می خواهید آلومینیوم سخت را با یک بیت روتر 2 فلوت به قطر 3 میلی متر روت کنید. از جدول پیدا می کنید: vc = 100 ... 200 m/min. از این رو شما محاسبه می کنید:حداکثر تعداد دور: n = (200 * 1000) / (3.14 * 3) = 200000 / 9.42 = 21.230 U/min
خوراک مربوطه: f = 21230 * 0.04 * 2 = 1698 میلی متر در دقیقهنرخ تغذیه بالا - به ویژه در فلزات - نیاز به یک دستگاه پایدار و بی صدا دارد. علاوه بر این، عمق شیار نباید خیلی زیاد باشد (حدود 1 * d 1).
برای ماشینهای با ثبات کمتر یا با افزایش عمق فرز، حالت به صورت زیر محاسبه میشود:حداکثر سرعت:
n = (200 * 1000) / (3.14 * 3) = 200000 / 9.42 = 21.230 U/min(مانند بالا)
کمترین تعداد دور: n = (100 * 1000) / (3.14 * 3) = 100000 / 9.42 = 10.615 U/min
خوراک مربوطه (حداقل): f = 10615 * 0.04 * 2 = 849 میلی متر در دقیقهشما n=21230 U/min و f=849mm/min را ترکیب می کنید.
حرکت متقابل و حرکت همزمان
چگونه لبه های برش متفاوت به وجود می آیند:تیغه از سمت باد وارد مواد می شود. در ناحیه ضد حرکت، کاتر در برابر مواد قرار می گیرد. ضخامت تراشه ها بر اساس تغذیه مواد به طور مداوم بزرگتر خواهد بود. در منطقه همزمانی، برش با مواد اجرا می شود، ضخامت تراشه قبل از خروج کاهش می یابد. ناحیه سایه دار ضخامت نسبی تراشه را در هر موقعیت تراشه در هر دور نشان می دهد. تیغه در حرکت متقابل دائماً در حال "گرفتن" مواد است، در حالی که در حرکت همزمان فقط مقدار کمی درست قبل از اینکه تیغه به هوا برود وارد می شود. بنابراین، آخرین قطعه اغلب به نظر می رسد "شکستن". به همین دلیل است که طرف مقابل حرکت همیشه صاف تر از سمت همزمانی است.
کدام کاتر برای کدام ماده | 1-شروع | 2-شروع | 3 طرفه | |||
خشن | صرفا | خشن | صرفا | خشن | صرفا | |
مواد چوبی | ||||||
چوب نرم (کاج) | ++ | 0 | +(+) | 0 | 0 | - |
جامد (بلوط، راش)، تخته سه لا، ام دی اف | +(+) | 0 | ++ | 0 | +(-) | - |
پلاستیک ها | ||||||
پی وی سی، پلی استایرن، تفلون، فوم | ++ | + | + | 0 | - | -- |
Duroplast، مواد با باکلیت (نئوپان) | + | + | ++ | + | + | - |
پلکسی گلاس ریخت | ++ | + | +(+) | - | 0 | - |
فلزات | ||||||
آلومینیوم نرم (Alucobond) | ++ | + | + | 0 | - | -- |
آلومینیوم سخت (فلوکسال) | 0 | + | + | ++ | 0 | + |
آلیاژهای برنج، برنز، مس | -- | - | 0 | +(-) | + | ++ |
فولاد سازه | -- | -- | - | + | - | ++ |
فولاد با کیفیت بالا | -- | -- | -- | - | -- | + |
++ خیلی خوبه + خوبه 0 رضایت بخش |
- بدجوری -- مناسب نیست |
هنگام پردازش فولادهای سخت، از 4 تیغه یا بیشتر استفاده می شود.
استفاده جزئی یا کامل از این موادفقط با توافق و با ذکر منبع الزامی است
در شرکت هایی که دارای بخش هایی هستند که به پردازش سطحی قطعات کار می پردازند، بر اساس اسناد نظارتینقشه های خاصی تهیه می شود که اپراتور را در ساخت یک قطعه خاص راهنمایی می کند. اگر چه در برخی موارد (به عنوان مثال، تجهیزات جدید، ابزار)، اپراتور فرز باید تفاوت های ظریف عملیات فن آوری را به طور مستقل تعیین کند. اگر یک دستگاه کم مصرف در خانه کار می کند، به خصوص که، به عنوان یک قاعده، هیچ راهنمایی رسمی در دسترس نیست.
این مقاله نه تنها به درک مبنای محاسبه حالت برش در هنگام فرزکاری و انتخاب ابزار مناسب کمک می کند، بلکه به شما کمک می کند. توصیه های عملیکه برای پردازش قطعات در سطح خانوار کافی است.
به کسانی که به میزان بیشتریبا فلزات مرتبط است، برای آشنایی دقیق تر با تفاوت های ظریف آسیاب، باید به کتاب درسی "ماشین های برش فلز" مراجعه کنید - 2003، Cherpakov B.I.، Alperovich T.A. روش محاسبه شرایط برش نیز در کتابچه های مختلف به خوبی توضیح داده شده است. به عنوان مثال، در توصیه های روش شناختیاز سال 2000 (MSAU - Kolokatov A.M.، Bagramov L.G.).
ویژگی فرزکاری این است که لبه های برش فقط به صورت دوره ای در تماس مستقیم با مواد قرار می گیرند. نتیجه ارتعاشات، بارهای ضربه ای و افزایش سایش برش ها است. موثرترین حالت حالتی است که در آن پارامترهای زیر به طور بهینه ترکیب شوند - عمق، تغذیه و سرعت برش بدون به خطر انداختن دقت و کیفیت پردازش. این همان چیزی است که امکان کاهش قابل توجه هزینه یک عملیات تکنولوژیکی و افزایش بهره وری را فراهم می کند.
پیش بینی به معنای واقعی کلمه تمام تفاوت های ظریف آسیاب غیرممکن است. قطعات کار مورد پردازش در ساختار، ابعاد و شکل متفاوت است. ابزارهای برش - با هندسه، طراحی، وجود یا عدم وجود لایه محافظ و غیره. هر آنچه در زیر در مورد حالت های برش بیان می شود باید فقط به عنوان یک راهنما در نظر گرفته شود. برای روشن شدن پارامترهای خاص آسیاب، باید از جداول خاص و داده های مرجع استفاده کنید.
انتخاب ابزار
این عمدتا به قطر آن مربوط می شود. انتخاب کاتر () بر اساس این پارامتر چه ویژگی خاصی دارد؟
- افزایش قطر به طور خودکار منجر به افزایش هزینه ابزار می شود.
- وابستگی متقابل دو نشانگر - اگر خوراک افزایش یابد، سرعت برش کاهش می یابد، زیرا توسط ساختار قطعه کار محدود می شود (به زیر مراجعه کنید).
قطر بهینه کاتر به گونه ای در نظر گرفته می شود که مقدار آن مطابق (یا کمی بیشتر از) عمق برش مورد نیاز باشد. در برخی موارد، در یک مرحله می توانید تراشه های ضخیم تر را انتخاب کنید، اما این فقط در مورد موادی که با چگالی کم مشخص می شوند اعمال می شود. مثلا فوم پلی استایرن یا برخی از انواع چوب.
سرعت برش
بسته به مواد نمونه، می توانید روی شاخص های زیر (m/min) تمرکز کنید:
- چوب، ترموپلاستیک – 300 – 500;
- پی وی سی – 100 – 250;
- فولاد ضد زنگ - 45 - 95;
- برنز – 90 – 150؛
- برنج – 130 – 320;
- باکلیت - 40 - 110؛
- آلومینیوم و آلیاژهای آن – 200 – 420.
سرعت چرخش کاتر
ساده ترین فرمول به صورت زیر است:
N (تعداد دور) = 1000 Vc (سرعت برش مطلوب) / π D (قطر برش).
از نظر ایمنی، نباید اسپیندل را با حداکثر سرعت برانید. این بدان معنی است که فقط به این دلیل سرعت برش تقریباً 10 - 15٪ کاهش می یابد. این "ضرر" را می توان تا حدی با نصب برش با قطر بزرگتر جبران کرد. این سرعت را کمی افزایش می دهد. اگر یک مورد مناسب در دسترس ندارید، باید تصمیم بگیرید که آیا پول خرج کنید یا خیر ابزار جدیدیا به قابلیت هایی که دستگاه فرز دارد راضی باشد. باز هم، همه اینها فقط با تمرین کار بر روی تجهیزات خاص قابل تأیید است، اما معنی کلیتوصیه ها واضح است.
اینینگ ها
شما باید به این پارامتر فرز دقت کنید!
دوام کاتر و کیفیت پردازش قطعه کار به میزان ضخامت لایه در یک پاس، یعنی با هر چرخش دوک، بستگی دارد. در این مورد، آنها بسته به نوع ابزار (برش تک، دو یا سه شروع) در مورد تغذیه در هر 1 (2.3) دندان صحبت می کنند.
مقادیر خوراک توصیه شده برای هر دندان توسط سازنده ابزار مشخص شده است. آسیاب در این مرحله از رژیم برش اگر با برشهای «ساخت چین» یا با منشأ مشکوک (ناشناخته) کار کند، با مشکلاتی مواجه میشود. در بیشتر موارد، می توانید روی محدوده تغذیه (میلی متر) 0.1 - 0.25 تمرکز کنید. این حالت تقریباً برای تمام مواد معمولی که در معرض فرز قرار می گیرند مناسب است. در طول فرآیند برش، مشخص خواهد شد که آیا کافی است کمی "افزودن" را انجام دهید (اما نه زودتر از اولین پاس). اما نباید کمتر از 0.1 را امتحان کنید، مگر زمانی که کار جواهرات را با استفاده از میکرو آسیاب انجام می دهید.
آسیاب باید با حداقل تغذیه 0.1 شروع شود. در طول فرآیند، مشخص خواهد شد که مواد مورد پردازش قبل از یک برش خاص چقدر چکشخوار است. این امر امکان شکستن لبه برش (دندان) را از بین می برد و امکان "تشخیص" دقیق از قابلیت های ماشین و ابزار را فراهم می کند، به خصوص اگر تجهیزات "خارجی" باشد.
- تجاوز از مقدار بهینه خوراک مملو از افزایش دما در منطقه کار، تشکیل تراشه های ضخیم و شکستن سریع برش است. برای ابزارهایی با قطر بیش از 3 میلی متر، باید با 0.15 شروع کنید، نه بیشتر
- در صورتی که با استفاده بهینه از قابلیت های دستگاه نمی توان سرعت فرزکاری قطعه را افزایش داد، می توانید یک کاتر دو فلوت نصب کنید.
- هنگام انتخاب ابزار، باید در نظر داشته باشید که افزایش طول قسمت برش منجر به کاهش تغذیه و افزایش ارتعاش می شود.
- شما نباید با تعویض کاتر با کاتر مشابه، اما با دندانه های بیشتر، سعی کنید سرعت پردازش را افزایش دهید. تراشه های چنین ابزاری به خوبی حذف نمی شوند و بنابراین اغلب منجر به کاهش شدید کیفیت فرز می شوند. در برخی موارد، هنگامی که شیارها کاملاً مسدود می شوند، کاتر شروع به بیکار می کند. چنین جایگزینی معنایی ندارد.
نتیجه
فرز با کیفیت بالا فقط از طریق تجربه به دست می آید. ماشین بتن + ابزار + تجربه عملی، مهارت ها. بنابراین، شما نباید کورکورانه حتی به داده های جدولی اعتماد کنید. مثلاً میزان سایش کاتری که قرار است با آن کار شود را در نظر نمی گیرند. نیازی به ترس از آزمایش نیست، اما همیشه باید با حداقل مقادیر پارامتر شروع کنید. وقتی استاد ماشین، کاتر و مواد در حال پردازش را "احساس" کند، خودش تعیین می کند که در چه حالتی باید کار کند.
چرا کاتر زود کدر می شود؟ چه چیزی باعث زغال شدن مواد فرآوری شده (نئوپان، ام دی اف یا چوب) پس از فرآوری با فرز می شود؟ چرا کاتر می سوزد؟ چگونه از چسبیدن رزین ها به لبه های برش کاتر جلوگیری کنیم؟ تنها یک پاسخ برای سوالات فوق وجود دارد - سرعت (فرکانس) چرخش برش به اشتباه انتخاب شده است.
تجهیزات فرز مدرن برای پردازش مواد تخته نئوپان چند لایه یا تخته ام دی اف مجهز به موتورهایی هستند که امکان دستیابی به سرعت دوک بیش از 20000 دور در دقیقه را فراهم می کنند. از یک طرف، این بر بهره وری تجهیزات تأثیر می گذارد، زیرا سرعت حرکت ابزار یا نرخ تغذیه قطعه کار افزایش می یابد. از سوی دیگر، کیفیت پردازش افزایش می یابد: احتمال بالا آمدن شمع روی ام دی اف، خراشیدگی روی چوب و خرد شدن روی تخته نئوپان چند لایه کاهش می یابد.
از روی عادت، از روی ناآگاهی، یا صرفاً از روی تنبلی، برای اینکه سر خود را با انواع دستورالعمل های عملیاتی، حالت های پردازش و سایر پیچیدگی ها اذیت نکنید، سرعت چرخش کاتر به حداکثر سطح تنظیم می شود که در آن همه مواد با استفاده از تمام برش های موجود پردازش می شوند. این همان جایی است که نهفته است دلیل اصلیتمام مشکلات
واقعیت این است که در سرعت بالا (فرکانس) چرخش کاتر و سرعت پایین تغذیه قطعه کار، لبه برش کاتر اکثربرای مدتی بیکار عمل می کند و به جای اینکه تراشه بعدی را از مواد در حال پردازش جدا کند، بیهوده به آن ساییده می شود. همه می دانند که در نتیجه اصطکاک - گرمایش چه اتفاقی می افتد. علاوه بر این، هر چه سرعت چرخش کاتر بیشتر باشد، اصطکاک شدیدتر است و کاتر بیشتر گرم می شود.
به نظر می رسد، چه چیزی در اینجا خاص است؟ خب داره گرم میشه اگر آن را در کف دست خود بگیرید، دست شما تحمل می کند. تکلیف فلز چه می شود؟! اما هنوز…
چرا کاتر می سوزد و به سرعت کدر می شود؟
گرمای حاصل از اصطکاک کاترهای برش در برابر مواد به تدریج به طور یکنواخت در کل بدنه آن توزیع می شود. بنابراین، در طول عملیات کوتاه مدت، گرمایش عملا احساس نمی شود. با این حال، در طول پردازش مواد، در لبه های برش است که درجه حرارت به حداکثر سطوح می رسد. و هر چه سرعت چرخش کاتر بیشتر باشد، اصطکاک و گرم شدن لبه ها قوی تر می شود.
این امر به ویژه در برش های با قطر بزرگ قابل توجه است. اینجا سرعت خطیحرکت قسمت بیرونی لبه برش نسبت به مواد بسیار بیشتر است. در نتیجه لبه های کاتر گرم می شوند و پس از سرد شدن با رنگ مایل به آبی تیره می شوند و این نشانه مطمئنی از گرم شدن فلز به حدی است که شروع به تغییر خواص خود می کند. از نظر علمی، جزء کربن در فلز می سوزد که به آن خاصیت سفتی می دهد. اگر به یاد داشته باشید که یک میخ معمولی وقتی در ذغال داغ اجاق گاز یا آتش قرار می گیرد چقدر نرم و انعطاف پذیر می شود، به راحتی می توان تصور کرد که یک کاتر در نتیجه گرمای بیش از حد چه ویژگی های جدیدی به دست می آورد.
شایان ذکر است که هنگام تیز کردن یک برش، سرعت چرخش چرخ یا دیسک سنگ زنی و درجه فشار ابزار مستقیماً بر گرم شدن لبه های تیز شده تأثیر می گذارد. اگر از خنک کننده استفاده نکنید، هر فلز کاربید به یک قطعه آهن معمولی تبدیل می شود که می تواند پس از تغییر شکل بار سبک. به هر حال، به همین دلیل است که عمر کاری برش، مته و اره پس از تیز کردن به میزان قابل توجهی کاهش می یابد.
چرا مواد می سوزد؟
همه چیز در اینجا بسیار واضح است: در نتیجه اصطکاک برش در برابر مواد ، دمای بالایی تشکیل می شود که تحت تأثیر آن چوب شروع به سوختن می کند. برای جلوگیری از این پدیده باید سرعت (فرکانس) چرخش کاتر را کاهش داد و نرخ تغذیه قطعه کار را افزایش داد. اما این اقدامات باید به شرطی انجام شود که کاتر تیز بودن خود را حفظ کرده باشد. که در در غیر این صورت، بار روی آن یا واحد برق به میزان قابل توجهی افزایش می یابد که می تواند منجر به خرابی آنها شود.
چسبیدن رزین به کاتر
بسیاری از چوب ها حاوی رزین هستند. در ساخت مواد پانل چوب مانند تخته نئوپان و ام دی اف از رزین های فرمالدئید نیز استفاده می شود. در حین پردازش مکانیکی این مواد که در اثر اصطکاک گرم می شوند، ذرات رزین می جوشند، روی دندانه های ابزار برش می افتند و همراه با گرد و غبار به آنها می چسبند. معمولاً اگر حالت تغذیه قطعه کار و سرعت برش ابزار به درستی انتخاب شود، این امر باعث ایجاد مشکلات قابل توجهی نمی شود. در غیر این صورت، هنگامی که یکی از پارامترها به اشتباه محاسبه می شود، سرعت چرخش کاتر بسیار زیاد است و پردازش با سرعت کم انجام می شود، یک پوشش رزین تیره روی برش ابزار ظاهر می شود. علاوه بر این، هر چه این اختلاف قوی تر باشد، سریعتر شکل می گیرد. در همان زمان، کیفیت پردازش کاهش می یابد، تراشه ها روی سطوح چند لایه ظاهر می شوند، چوب شروع به سوزاندن می کند، ابزار استرس اضافی دریافت می کند، به سرعت بیش از حد گرم می شود و از کار می افتد. بنابراین، انتخاب سرعت چرخش برش و سرعت تغذیه مواد بسیار مهم است.
علاوه بر محاسبه صحیح حالت پردازش مواد، لازم است به مراقبت از ابزار برش نیز توجه کنید، یعنی به سرعت پوشش رزین حاصل را تمیز کنید یا آن را با آب گرم معمولی بشویید.
محاسبه سرعت (فرکانس) چرخش کاتر
برای محاسبه صحیح سرعت چرخش کاتر و سرعت حرکت آن، باید عوامل زیادی از جمله خواص فیزیکی و مکانیکی ماده و ابزار، عمق و عرض پردازش و غیره را در نظر گرفت.
از طرف دیگر، موادی مانند ام دی اف و نئوپان در مقایسه با فلزات مختلف، بسیار راحت تر پردازش می شوند. بنابراین، ما می توانیم صرفاً شاخص کیفیت پردازش، یعنی وجود زبری، برآمدگی، براده ها و فرزها را روی سطح تحت درمان قرار دهیم.
برای پردازش کم و بیش با کیفیت تخته نئوپان لمینت شده، لازم است که نرخ تغذیه به ازای هر دندان کاتر (یا به عبارت ساده، ضخامت براده هایی که از زیر کاتر خارج می شوند) 0.05 - 0.15 میلی متر باشد. بنابراین، یک فرز دو برش معمولی باید 0.1 - 0.3 میلی متر در هر دور و 1500 - 4500 میلی متر در هر 15000 دور برش دهد. یعنی سرعت تغذیه مواد به کاتر، در 15000 دور در دقیقه، باید 1.5 - 4.5 متر در دقیقه یا 25 -75 میلی متر در ثانیه باشد.
اگر ماشینکاری با نرخ تغذیه پایین مورد نیاز باشد، به عنوان مثال. روتر دستی، سپس محاسبه سرعت چرخش کاتر را می توان بر اساس سرعت حرکت کاتر با انجام محاسبات به صورت معکوس انجام داد. فرض کنید این ماده با سرعت 10 میلی متر در ثانیه یا 600 میلی متر در دقیقه پردازش می شود. با نرخ تغذیه به ازای هر دندان معادل 0.1 میلی متر و کار با کاتر دو برش، سرعت چرخش مورد نیاز کاتر 600/(0.1) خواهد بود.× 2) = 3000 دور در دقیقه.
نکات ایمنی هنگام کار با برش
به عنوان یک قاعده، سازندگان تجهیزات و ابزار فرز، دستورالعمل های ایمنی را به محصولات خود متصل می کنند و حالت های عملکرد توصیه شده را برای برش ها نشان می دهند. جدول زیر پارامترهای ایمن برای سرعت چرخش کاتر بسته به قطر را نشان می دهد.
قطر برش، میلی متر |
حداکثر سرعت چرخش کاتر، دور در دقیقه |
تا 25 |
24000 |
26 – 50 |
18000 |
51 – 63 |
16000 |
64 – 75 |
14000 |
76 – 87 |
12000 |
انتخاب حالت برش هنگام آسیاب
§ 78. شرایط تعیین کننده انتخاب حالت برش
مفهوم سودمندترین حالت برش
این حالت برش باید هنگام کار بر روی آن سودمندترین حالت در نظر گرفته شود آسیاب، که در آن سرعت برش، تغذیه و عمق لایه برش با موفقیت در این شرایط خاص (یعنی با در نظر گرفتن بهترین استفاده از خواص برش ابزار، سرعت و توان دستگاه) فراهم می شود. بالاترین بهره وری نیروی کار و کمترین هزینه عملیات با رعایت شرایط فنی مشخص شده در خصوص دقت و خلوص پردازش.
موسسه تحقیقات علمی کار کمیته دولتی شورای وزیران اتحاد جماهیر شوروی در مورد کار و دستمزدبا در نظر گرفتن مشارکت دانشمندان برجسته داخلی توسعه یافته است کاربرد عملیدر شرایط تولید، حالت های برش هنگام آسیاب با ابزارهای ساخته شده از فولاد پرسرعت و آلیاژهای سخت. آنها می توانند به عنوان داده های ورودی هنگام تخصیص سرعت های برش و تغذیه های دقیقه ای استفاده کنند.
این استانداردها در هر کارخانه موجود است و به عنوان راهنمایی برای توسعه عمل می کند فرآیند تکنولوژیکیو ترسیم نمودارهای عملیاتی مانند آنچه در صفحات 204-205 نشان داده شده است. با این حال، سرعت های برش و تغذیه دقیقه داده شده در آنها حداکثر نیست و در برخی موارد می تواند توسط اپراتورهای فرز در صورت استفاده از ابزارهای مولدتر یا کار بر روی ماشین های قوی تر و سفت تر از آن فراتر رود.
از طرف دیگر، اپراتورهای فرزکاری جوان، یعنی مبتدیان و کسانی که تجربه کافی ندارند، همیشه نمی توانند در شرایط برش شدید کار کنند، بنابراین، شرایط برش کمتر سخت تری برای آنها در "راهنمای اپراتور جوان آسیاب" ارائه شده است، که از آنجا شروع می شود. لازم است، به عنوان آموزش پیشرفته، به سراغ آموزش های سخت تر بروید.
برای اینکه خودتان حالت های جدید را معرفی کنید، باید ترتیب و ترتیب ایجاد حالت های فرز را بدانید.
مواد فرز برش
عامل تعیین کننده سطح حالت برش، جنس قسمت برش کاتر است. همانطور که در بالا ذکر شد، استفاده از برش با درج کاربید به شما این امکان را می دهد که در مقایسه با برش های ساخته شده از فولاد پر سرعت، با سرعت برش بالا و تغذیه بالا کار کنید. همانطور که در ادامه خواهیم دید، برش های کاربید امکان افزایش بهره وری را دو تا سه برابر در مقایسه با برش های پرسرعت فراهم می کنند. بنابراین، استفاده از برش های کاربید برای تقریباً همه انواع آسیاب توصیه می شود. یک مانع برای استفاده از آنها ممکن است قدرت ناکافی تجهیزات یا خواص خاص مواد قطعه کار در حال پردازش باشد.
با این حال، در تعدادی از موارد، استفاده از کربن، ابزار آلیاژی و فولادهای پرسرعت برای قسمت برش کاترها منطقی است، به ویژه زمانی که تمیزی سطح ماشینکاری شده و دقت سطح حاصل از قطعه اهمیت بیشتری دارد. از سرعت کار
پارامترهای هندسی قطعه برش
یک عامل به همان اندازه مهم در انتخاب حالت های برش، پارامترهای هندسی قسمت برش کاتر (زوایای برش، ابعاد و شکل دندان) است که اغلب به آن گفته می شود. هندسه کاتر. پیش از این، در § 7، اهمیت و تأثیر هر یک از عناصر هندسه دندان برش در طول فرآیند برش در نظر گرفته شد. در اینجا ما پارامترهای هندسی توصیه شده قسمت برش فرزهای ساخته شده از فولاد پرسرعت R18 و با درج کاربید را در نظر خواهیم گرفت.
روی میز 35 و 36 مقادیر توصیه شده پارامترهای هندسی فرزهای استوانه ای، انتهایی، دیسکی، برشی، انتهایی و شکل دار ساخته شده از فولاد پرسرعت را نشان می دهد.
جدول 35
پارامترهای هندسی قسمت برش فرزهای ساخته شده از فولاد پرسرعت P18
I. گوشه های جلو

II. گوشه های پشتی

III. زوایای لبه پیشرو و انتقالی

یادداشت 1. برای برش های استوانه ای با زاویه شیب دندانی بیش از 30 درجه، زاویه چنگک γ هنگام پردازش فولاد σ b کمتر از 60 است. کیلوگرم بر میلی متر 2 برابر با 15 درجه در نظر گرفته شده است.
2. برای برش های شکل دار با زاویه چنگک بیشتر از 0 درجه، اصلاح کانتور هنگام پردازش پروفیل های دقیق ضروری است.
3. هنگام پردازش فولادهای مقاوم در برابر حرارت با آسیاب انتهایی، مقادیر بالای زوایای چنگک و در آسیاب های انتهایی و استوانه ای، مقادیر پایین و میانی را در نظر بگیرید.
4. هنگام تیز کردن، یک نوار سنباده دایره ای با عرض حداکثر 0.1 در سطح پشتی کاترها بگذارید. میلی متر. دندانه های برش های شکاف دار (شاخ دار) و برش (اره دایره ای) بدون باقی ماندن نوار تیز می شوند.

روی میز 37 - 40 مقادیر توصیه شده زوایای جلو و عقب، زوایای اصلی، کمکی و انتقالی در پلان، زوایای شیب لبه برش و شیارهای مارپیچ، شعاع راس صورت، استوانه، فرز انتهایی و دیسکی را نشان می دهد. برش با درج کاربید.
کاترهایی که برای پردازش بیشتر قطعات کار استفاده می شوند معمولاً توسط کارخانه های ابزارسازی با پارامترهای هندسی مربوط به GOST عرضه می شوند و تقریباً غیرممکن است که آسیاب برخلاف تراش و رنده، زوایای برش کاترها را با تیز کردن تغییر دهد. در نتیجه، مواردی که در جدول آورده شده است. 35 - 40 پارامتر هندسی قسمت برش کاترها به اپراتور فرز کمک می کند تا به درستی کاتر مناسب برای یک پردازش معین را از کاترهای استاندارد موجود در فروشگاه ابزار کارگاه آموزشی و تولیدی انتخاب کند. با این حال، هدف اصلی این جداول ارائه توصیههایی در صورتی است که اپراتور ماشین فرز بخواهد برشهای استاندارد یا ویژه را از بخش ابزار با پارامترهای هندسی بهینه برای یک پردازش خاص سفارش دهد.
جدول 37
پارامترهای هندسی قسمت برش آسیاب های انتهایی با درج کاربید

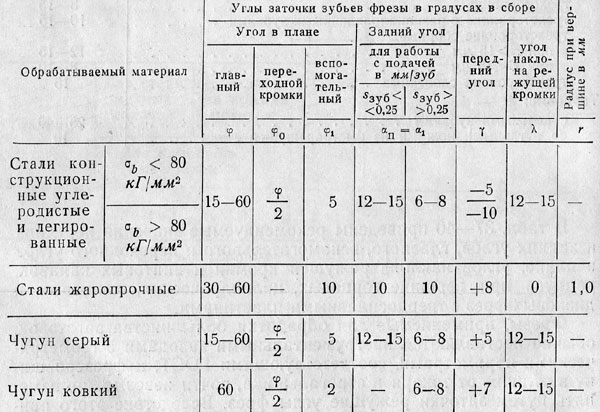
توجه داشته باشید: زوایای ورودی کوچک φ = 15 - 30 درجه باید هنگام پردازش بر روی ماشینهای صلب برای گذرگاههای خشن با عمق برش کوچک یا گذرگاههای تکمیلی با نیاز کم برای تمیزی و دقت سطح ماشینکاری شده استفاده شود.
جدول 38
پارامترهای هندسی قسمت برش فرزهای استوانه ای با درج های پیچ ساخته شده از آلیاژ سخت


توجه داشته باشید: در سطح پشتی دندان در امتداد لبه برش، یک روبان با عرض بیش از 0.1 مجاز است. میلی متر.
جدول 39
پارامترهای هندسی قسمت برش آسیاب های انتهایی با درج های کاربید هنگام پردازش فولادهای کربنی و آلیاژی ساختاری


* با سفتی کم دستگاه - فیکسچر - ابزار - سیستم قطعه کار و با مقاطع تراشه بزرگ ( که دربیشتر دی; تیبیش از 0.5 دی) و همچنین هنگام کار با سرعت های پایینبرش با سرعت اسپیندل ناکافی ( vکمتر از 100 متر در دقیقه) زاویه جلو γ مثبت + از 0 تا +8 درجه است.
** مقادیر بزرگتر برای فولادهای نرم، مقادیر کوچکتر برای فولادهای سخت.
عرض و عمق فرز
عرض فرزدر نقشه قطعه مشخص شده است. در صورت پردازش چندین قطعه کار که به طور موازی در یک دستگاه گیره گیره شده اند، عرض فرز برابر با عرض تمام قطعات کار است. در مورد پردازش با مجموعه ای از برش ها، عرض فرز برابر با عرض کل تمام سطوح جفت گیری است.
عمق آسیاب(عمق برش، ضخامت لایه برش) به عنوان فاصله بین سطوح ماشینکاری شده و ماشینکاری شده داده می شود. برای کاهش زمان پردازش، توصیه می شود فرز را در یک پاس انجام دهید. با افزایش نیاز به دقت و تمیزی سطح ماشینکاری شده، فرز در دو مرحله - خشن و تکمیل انجام می شود. در برخی موارد، هنگام حذف مقادیر زیاد یا هنگام فرز بر روی ماشین هایی با توان ناکافی، پردازش در دو پاس زبر امکان پذیر است.
جدول 40
پارامترهای هندسی قسمت برش کاترهای دیسکی با درج کاربید


هنگام آسیاب آهنگری فولادی، ریخته گری فولادی و چدنی پوشیده از فلس، پوسته ریخته گری یا آلوده به ماسه ریخته گری، عمق آسیاب باید بیشتر از ضخامت لایه آلوده باشد تا دندان های برش روی سطح ماشینکاری شده زبرها باقی نماند. از آنجایی که لغزش روی پوسته بر روی کاتر اثر منفی می گذارد و سایش لبه برش را تسریع می کند.
برای رایج ترین موارد آسیاب، انجام زبری روی فولاد با عمق برش 3-5 توصیه می شود. میلی متر، و برای فولاد و ریخته گری آهن- با عمق برش 5-7 میلی متر. برای تکمیل فرز، عمق برش 0.5-1.0 را در نظر بگیرید میلی متر.
قطر برش
قطر برش عمدتا بسته به عرض فرز انتخاب می شود که درو عمق برش تی. روی میز 41 داده هایی را برای انتخاب برش های استوانه ای، جدول نشان می دهد. 42 - آسیاب های انتهایی و در جدول. 43 - برش دیسک.

* از برش های کامپوزیت پیش ساخته مطابق با GOST 1979-52 استفاده کنید.


بیایید تأثیر قطر برش را بر عملکرد فرز در نظر بگیریم.
قطر برش استوانه ای بر ضخامت برش تأثیر می گذارد: هر چه قطر برش بزرگتر باشد دیهر چه برش نازک تر باشد. با همان خوراک سدندانه و عمق فرز تی.
در شکل شکل 327 برش به دست آمده در همان عمق فرز را نشان می دهد تیو تسلیم سدندان، اما با قطرهای مختلف برش. برش به دست آمده با قطر برش بزرگتر (شکل 327، الف) ضخامت کمتری نسبت به برش با برش کوچکتر دارد. قطر برش (شکل 327، ب).

از آنجایی که با کاهش ضخامت لایه برش فشار ویژه افزایش می یابد آ Naib (به جدول 38 مراجعه کنید)، کار با مقاطع ضخیم تر، یعنی همه چیزهای دیگر یکسان، با قطر برش کوچکتر، سودآورتر است.
قطر کاتر روی مسافتی که کاتر باید برای یک پاس طی کند تاثیر می گذارد.
در شکل 328 مسیری را که کاتر هنگام پردازش بخشی از طول باید طی کند را نشان می دهد L; در شکل 329 - مسیری که آسیاب صورت باید هنگام آسیاب نامتقارن قطعه کار به طول طی کند L; در شکل 330 - مسیری که یک کیک برش هنگام آسیاب متقارن قطعه کار با طول باید طی کند. L.

اندازه خوراک l(مسیر برش):
هنگام کار با کاترهای استوانه ای، دیسکی، برش و شکل به قطر کاتر بستگی دارد دیاعماق آسیاب تیو با فرمول بیان می شود
هنگام کار با آسیاب های صورت و انتهایی برای فرز نامتقارن، به قطر برش بستگی دارد دیعرض فرز که درو با فرمول بیان می شود
هنگام کار با آسیاب های صورت برای فرز متقارن، به قطر برش بستگی دارد دیعرض فرز که درو با فرمول بیان می شود
ارزش اضافه سفر l 1 بسته به قطر برش در 2-5 انتخاب می شود میلی متر.
بنابراین، برای کاهش مسیر برش و رفت و آمد بیش از حد برش، یعنی برای کاهش سرعت بیکاری دستگاه، توصیه می شود قطر کاتر کمتری را انتخاب کنید.
در انتهای کتاب در پیوست های 2 و 3 جداولی برای مقادیر مسیرهای ورودی و سرگذر کاترها آورده شده است.
قطر برش بر روی مقدار تأثیر می گذارد گشتاور: هرچه قطر کاتر کمتر باشد، گشتاور کمتری باید به دوک ماشین وارد شود.
بنابراین، انتخاب یک برش با قطر کمتر مناسب تر به نظر می رسد. با این حال، با کاهش قطر برش، لازم است یک سنبه فرز نازک تر، یعنی سنبه فرز سفت تر انتخاب شود، بنابراین لازم است بار روی سنبه کاهش یابد، یعنی سطح مقطع لایه برش را کاهش دهید. .
اینینگ ها
تغذیه در خشن کردنبستگی به مواد در حال پردازش، مواد قسمت برش کاتر، قدرت محرک دستگاه، استحکام دستگاه - فیکسچر - ابزار - سیستم قطعه، ابعاد پردازش و زوایای تیز کردن کاتر دارد.
تغذیه در به پایان رساندنبستگی به کلاس تمیزی سطح نشان داده شده در نقشه قطعه دارد.
مقدار اولیه اصلی هنگام انتخاب خوراک برای آسیاب خشن، خوراک است سدندان
برای فرزهای صورت، خوراک قابل انتخاب سدندان روشی برای نصب کاتر نسبت به قطعه کار دارد که زاویه برخورد دندانه کاتر با قطعه کار و ضخامت براده های برش خورده را در هنگام ورود و خروج دندانه کاتر با قطعه کار تعیین می کند. مشخص شده است که برای آسیاب انتهایی کاربید، مطلوب ترین شرایط برای برش دندان در قطعه کار زمانی حاصل می شود که برش نسبت به قطعه کار قرار گیرد، مانند شکل 1. 324، در، یعنی زمانی که کاتر نسبت به قطعه کار به مقداری جابجا می شود با = (0,03 - 0,05)دی. این جابجایی محور کاتر باعث می شود که در هنگام آسیاب متقارن (شکل 324، الف) چدن و فولاد، خوراک هر دندان در برابر خوراک را به میزان دو یا بیشتر افزایش دهیم.
روی میز شکل 44 نرخ خوراک توصیه شده برای آسیاب خشن با آسیاب انتهایی کاربید را برای این دو مورد نشان می دهد.

یادداشت 1. مقادیر داده شده خوراک های زبر برای کار با برش های استاندارد محاسبه می شود. هنگام کار با برش های غیر استاندارد با تعداد دندان های افزایش یافته، مقادیر خوراک باید 15 تا 25٪ کاهش یابد.
2. در طول دوره اولیه کار کاتر، تا زمانی که سایش برابر 0.2-0.3 شود میلی مترتمیزی سطح ماشینکاری شده در حین آسیاب ریز تقریباً یک کلاس کاهش می یابد.

توجه داشته باشید. از فیدهای بزرگتر برای عمق برش و عرض پردازش کوچکتر، از خوراکهای کوچکتر برای عمق و عرض پردازش بزرگتر استفاده کنید.

توجه داشته باشید. تغذیه برای دستگاه سیستم سفت و سخت - فیکسچر - ابزار - قطعه داده شده است.
هنگام آسیاب صورت با کاترهای کاربید، نرخ تغذیه نیز تحت تاثیر زاویه فسفر قرار می گیرد. فیدهای ارائه شده در جدول 44، طراحی شده برای برش با φ = 60 - 45 درجه. کاهش زاویه φ به 30 درجه به شما این امکان را می دهد که تغذیه را 1.5 برابر افزایش دهید و افزایش زاویه φ به 90 درجه مستلزم کاهش 30 درصدی تغذیه است.
نرخ خوراک برای تکمیل با برش کاربید، در جدول آورده شده است. 44، برای یک دور کاتر داده می شود، زیرا تغذیه در هر دندان بسیار کوچک است. بسته به کلاس تمیزی سطح تحت درمان طبق GOST 2789-59، خوراک ها داده می شود.
روی میز شکل 45 خوراک توصیه شده به ازای هر دندان کاتر را برای فرز خشن صفحات با استوانه، صورت و دیسک نشان می دهد. برش های سه طرفهساخته شده از فولاد پرسرعت R18.
روی میز شکل 46 نرخ خوراک برای تکمیل فرز هواپیماها با برش های استوانه ای ساخته شده از فولاد پرسرعت P18 و در جدول را نشان می دهد. 47 - برای تکمیل فرز هواپیماها با کاترهای سه طرفه صورت و دیسکی ساخته شده از فولاد پرسرعت P18. با توجه به نرخ تغذیه پایین به ازای هر دندان کاتر به دست آمده در هنگام فرزکاری نهایی، در جدول. 46 و 47 تغذیه در هر دور کاتر را نشان می دهد.
باید در نظر داشت که کار با فیدهای نشان داده شده در جدول. 44-47، آن را به شرطی ضروری برای وجود حداقل ریزش دندان های برش می کند (جدول 50 را ببینید).

توجه داشته باشید. هنگام ماشینکاری با کاترها با زاویه ورودی کمکی φ 1 = 2، تغذیه برای یک دستگاه سیستم سفت و سخت - فیکسچر - ابزار - قطعه کار داده می شود. برای برش های با φ 1 = 0، تغذیه را می توان 50 - 80٪ افزایش داد.