Til Kategori:
Fresearbeid
Valg av rasjonelle fresemoduser
Å velge en rasjonell fresemodus på denne maskinen betyr at for de gitte bearbeidingsforholdene (materiale og merke på arbeidsstykket, dets profil og dimensjoner, bearbeidingsgodtgjørelse), er det nødvendig å velge den optimale typen og størrelsen på kutteren, materialkvaliteten og de geometriske parameterne til skjæredelen av kutteren, smørende og kjølende skjærevæske og tilordne de optimale verdiene for følgende skjæremodusparametere: B, t, sz. v, n, Ne, Tm.
Fra formel (32) følger det at parameterne B, t, sz og v har samme effekt på den volumetriske produktiviteten til fresing, siden hver av dem går inn i formelen i første grad. Dette betyr at med en økning i noen av dem, for eksempel med en faktor på to (med andre parametere uendret), vil den volumetriske produktiviteten også øke med en faktor på to. Disse parameterne har imidlertid ikke samme effekt på verktøyets levetid (se § 58). Derfor, med tanke på verktøyets levetid, er det mer fordelaktig først og fremst å velge de maksimalt tillatte verdiene for de parameterne som har en mindre effekt på verktøyets levetid, dvs. i følgende rekkefølge: skjæredybde, mating per tann og kuttehastighet. Derfor bør valget av disse parametrene for skjæremodus under fresing på denne maskinen startes i samme sekvens, nemlig:
1. Kuttdybden tilordnes avhengig av bearbeidingsgodtgjørelse, kravene til overflateruhet og maskinens kraft. Det er ønskelig å fjerne godtgjørelsen for behandling i ett pass, under hensyntagen til maskinens kraft. Vanligvis overstiger ikke skjæredybden for grovfresing 4-5 mm. For grovfresing med flate karbidkuttere(hoder) på kraftige fresemaskiner kan den nå 20-25 mm eller mer. Ved ferdigfresing overstiger ikke skjæredybden 1-2 mm.
2. Maksimalt tillatt fôr i henhold til bearbeidingsforholdene er tildelt. Når du stiller inn maksimalt tillatte fôringer, bør fôringer per tann som er nær "bryte" brukes.
Den siste formelen uttrykker avhengigheten av matingen per tann av fresedybden og diameteren til kutteren. Verdien av den maksimale kuttetykkelsen, dvs. verdien av den konstante koeffisienten Ic i formel (21), avhenger av de fysiske og mekaniske egenskapene til materialet som behandles (for en gitt type og utforming av kutteren). Verdiene for de maksimalt tillatte feedene er j begrenset av forskjellige faktorer:
a) under grovbearbeiding - stivheten og vibrasjonsmotstanden til verktøyet (med tilstrekkelig stivhet og vibrasjonsmotstand til maskinen), stivheten til arbeidsstykket og styrken til den skjærende delen av verktøyet, for eksempel en kuttertann, utilstrekkelig volum av sponspor f.eks for skivekuttere etc. Altså, mating per tann ved grovfresing av stål med sylindriske freser med innsatskniver og stor tann velges innenfor 0,1-0,4 mm/tann, og ved bearbeiding av støpejern opp til t.o.m. 0,5 mm / tann;
b) ved etterbehandling - overflateruhet, dimensjonsnøyaktighet, tilstanden til overflatelaget osv. Ved etterbehandling av fresing av stål og støpejern tildeles en relativt liten mating per skjæretann (0,05-0,12 mm / tann).
3. Kuttehastigheten bestemmes; slik hun gjengir mest stor innflytelse på verktøyets holdbarhet, så velges det basert på holdbarhetsstandarden som er vedtatt for dette verktøyet. Skjærehastigheten bestemmes av formelen (42) eller i henhold til tabellene med standarder for skjæreforhold, avhengig av dybde og bredde på fresing, mating per tann, kutterdiameter, antall tenner, kjøleforhold, etc.
4. Den effektive skjærekraften Ne bestemmes i valgt modus i henhold til tabellene over standarder eller i henhold til formelen (39a) og sammenlignes med maskinens kraft.
5. Av angi hastighet kutting (u, eller i ^) det nærmeste trinnet i maskinens spindelhastighet bestemmes blant de som er tilgjengelige på denne maskinen i henhold til formelen (2) eller i henhold til planen (fig. 174). Fra punktet som tilsvarer den aksepterte skjærehastigheten (for eksempel 42 m / min), utfør horisontal linje, og fra et punkt med et merke av den valgte kutterdiameteren (for eksempel 110 mm) - vertikal. Ved skjæringspunktet mellom disse linjene bestemmes det nærmeste trinnet i spindelhastigheten. Så, i eksemplet vist i fig. 172, ved fresing med en kutter med diameter D = 110 mm ved en skjærehastighet på 42 m/min vil spindelhastigheten være 125 rpm.
Fig.174 Nomogram for freserhastighet
6. Minuttmatingen bestemmes av formelen (4) eller i henhold til tidsplanen (fig. 175). Så når du freser med en kutter D = 110 mm, z = 10 ved sz = 0,2 mm/tann og n = 125 rpm, bestemmes minuttmatingen i henhold til skjemaet som følger. Fra punktet som tilsvarer matingen per tann sg = 0,2 mm / tann, tegner vi vertikal linje til den skjærer med en skrå linje som tilsvarer antall kuttertenner r = 10. Fra det oppnådde punktet tegner vi en horisontal linje til den skjærer en skrå linje som tilsvarer den aksepterte spindelhastigheten l = 125 rpm. Tegn deretter en vertikal linje fra det resulterende punktet. Skjæringspunktet for denne linjen med den nedre skalaen for minuttmatinger som er tilgjengelig på denne maskinen, bestemmer det nærmeste trinnet med minuttmatinger.
7. Maskintid bestemmes.
maskin tid. Tiden hvor prosessen med fjerning av spon finner sted uten direkte deltakelse fra arbeideren kalles maskintid (for eksempel for fresing av arbeidsstykkeplanet fra det øyeblikket den mekaniske langsgående matingen slås på til den slås av).
Ris. 1. Nomogram for minuttmating
Produktivitetsgevinster ved maskinering på metallskjæremaskiner begrenses av to hovedfaktorer: maskinens produksjonsevne og verktøyets skjæreegenskaper. Hvis produksjonsevnen til maskinen er liten og ikke tillater full bruk av verktøyets kutteegenskaper, vil produktiviteten til en slik maskin bare være en brøkdel av den mulige produktiviteten med maksimal bruk av verktøyet. I tilfelle maskinens produksjonsevne overskrider verktøyets skjæreegenskaper betydelig, kan maksimalt mulig produktivitet med dette verktøyet oppnås på maskinen, men maskinens evner, dvs. maskinens kraft, er maksimalt. tillatte skjærekrefter etc. vil ikke bli utnyttet fullt ut e. Optimalt sett med tanke på produktivitet og økonomi ved bruk av maskinen og verktøyet vil være slike tilfeller når maskinens produksjonskapasitet og verktøyets kutteegenskaper vil matche eller er nær hverandre.
Denne tilstanden er grunnlaget for de såkalte produksjonsegenskapene til verktøymaskiner, som ble foreslått og utviklet av prof. A. I. Kashirin. Maskinens produksjonskarakteristikk er en graf over avhengigheter mellom egenskapene til maskinen og verktøyet. Produksjonsegenskaper gjør det enklere og enklere å bestemme de optimale skjæreforholdene ved bearbeiding på en gitt maskin.
Kutteegenskapene til et bestemt verktøy er preget av skjæreforhold som er tillatt under bearbeiding. Kuttehastigheten under gitte bearbeidingsbetingelser kan bestemmes med formelen (42, a). I praksis er det funnet i henhold til tabellen over skjæreforhold, som er gitt i referansebøkene til vurdereren eller teknologen. Det skal imidlertid bemerkes at standardene for skjæreforhold for både fresing og andre typer bearbeiding er utviklet basert på skjæreegenskapene til verktøyet for ulike anledninger bearbeiding (type og størrelse på verktøyet, type og merke av materiale til skjæredelen, materiale som bearbeides osv.), og er ikke knyttet til maskinene som bearbeidingen skal utføres på. Siden produksjonskapasiteten til forskjellige maskiner er forskjellige, vil den praktisk mulige optimale prosesseringsmodusen på forskjellige maskiner være forskjellig for de samme prosessforholdene. Produksjonsevnen til maskinverktøy avhenger først og fremst av maskinens effektive kraft, hastighet, fôring osv.
Ris. 2. Stup og overkjør
Produksjonsegenskapene til freser for skjæring med tunge kuttere ble utviklet av prof. A. I. Kashirin og forfatteren.
Prinsippet for å konstruere produksjonsegenskapene til fresemaskiner (nomogrammer) for arbeid med flatfreser er basert på skjøten grafisk løsning to ligninger som karakteriserer avhengigheten av skjærehastigheten vT i henhold til formelen (42) med -Bz' = const, på den ene siden, og skjærehastigheten id„, den tillatte kraften til maskinen, på den andre. Kuttehastigheten vN kan bestemmes fra formelen
Ris. 3. Produksjonsegenskaper til konsollfresemaskinen 6P13
Kutteforhold
Venstre håndskjærere
Hvorfor fresing mot fôr er bedre.Problem: 2-starts kutteren smelter PVC-skummet.
Løsning: velg et mindre antall omdreininger eller fres med en entråds kutter. (Bilde)
1. Nedsenking:
Kutteren skal kunne trenge endeflaten inn i materialet (borefunksjon).
2. Skjærkant:
Som regel skiller kantene på passasjen seg fra hverandre. Motsiden av bevegelse er "vakkere" enn siden av synkronisitet. Dette er spesielt tydelig ved bruk av en 1-starts kutter, samt ved fresing av aluminium.
Råd; Fres de indre konturene med klokken, de ytre mot klokken. Dermed er den "dårlige" siden i sjetongene
3. Fjerning av brikker:
Flisen må evakueres raskt slik at hulrommene i kutterne ikke fylles, og som et resultat av at kutteren ikke går i stykker. Jo dypere og raskere fresingen skjer, desto vanskeligere er det å evakuere flisene. Veibeskrivelse: Ikke fres dypere enn dobbel eller tredoble kutterdiameteren. Gå dypere riller i flere omganger. Når du freser polystyren og annen plast, er det fornuftig å bruke kuttere med polerte riller for bedre ytelse.
4. Varmespredning / smøring:
Kutteren skal ikke bli for varm: På den ene siden mister verktøyet sine egenskaper ved for høy temperatur, på den andre siden, enda mer kritisk, kan plast- og aluminiumsspon "klistre" i sporene og hindre at sponene blir fjernet og som et resultat fører til brudd på kutteren. Ved bearbeiding av metaller er det viktig å anbefale et smøremiddel. Merk: Aluminium og ikke-jernholdige metaller kan males med alkohol eller spesielle emulsjoner, og såpevann kan brukes til plexiglass.
5. Fare for brudd:
øker lineært med økende matehastighet og med økende nedsenkingsdybde: Dobbel mating betyr dobbel fraksjonsrisiko, dobbel nedsenkingsdybde betyr åtte ganger fraksjonsrisiko.
Veibeskrivelse:
Det er bedre å frese i flere omganger mindre dypt og med høyere matehastighet. Bruk en kutter med kortest mulig klippelengde. Stram den så mye som mulig. Generell regel: klemt fast i chucken (chuck spennhylse) en tredjedel Total lengde kuttere.
Det riktige snittet bringer sjetongene til toppen.
Den riktige kutteren letter fjerning av spon opp, noe som er bra for kontinuerlig produksjon, men det har den ulempen at kutteren, som en korketrekker, også flytter grunnmaterialet (emnet) opp, "mohr" ved fresing av tre eller " huler" når du behandler tynt arkmateriale (for eksempel bevegelser). En kutter med venstre helix, motsatt, presser ned på materialet og ved kapping av fibermaterialer som tre eller papp oppnår man en jevnere toppkant (fibrene reiser seg ikke, men "presses" inn i grunnmaterialet). Men her er den negative faktoren vanskeligheten med å fjerne chip.
Merk:
I standardtilfeller, bruk en høyre kutter.
Venstrehåndsklippere er gunstige for grunne kutt i tynne materialer, hvor faren for å "grave" og rykke opp arbeidsstykket til høyre snitt er stor. Men jo hardere materialet du bruker, desto raskere kan du bli kvitt den venstre helix-kutteren.
A. Høyre kutt (normal form):
Trekk snoren opp. Kutteren har en tendens til å "grave" og løfte grunnmaterialet.
"korketrekkereffekt".
B. Venstre helix (spesiell form): Driver spon ned når den vender, eller brukes når du arbeider i et allerede frest hulrom. Kutteren presser på grunnmaterialet (det motsatte av en "korketrekkereffekt").
Ikke egnet for dypfresing.
Type kutter: 1 eller 2 kniver?
Det finnes et uendelig antall kuttere, men i hovedsak skiller vi mellom skarpe og stumpe. Jo skarpere bladet er, desto raskere slites tuppen ut.Generell regel: jo høyere styrke materialet har, desto flatere bør slipingen være ved bladet. Denne slipingen er egnet for harde metaller (f.eks. messing). Skarpere fiskehalesliping for plast, tre og mykt aluminium. Blader er slitesterke deler av kutteren. I kuttere med mer enn ett blad fordeles belastningen og verktøyets levetid økes. Disse kutterne går raskere, vibrerer mindre i vanskelige materialer som rustfritt stål. Med flere blader - under samme freseforhold - blir sponene tynnere, noe som gir en jevnere overflate til slutt.
Valget av den "ideelle" kuttertypen avhenger alltid av materialet som skal bearbeides:
Ved fresing av "myke" materialer: myk plast (PVC, pleksiglass, skum), trematerialer (tre, fiberplater, kryssfiner, sponplater), myk aluminium og sandwichmaterialer (aluminium/plast) drar nytte av skarpe 1-starts kuttere. Siden her er problemet med raskere sløving å foretrekke fremfor faren for tilstopping og brudd på kutteren.
For hardplast passende skarp 2-veis, med fiskehaleprofil.
Ved bearbeiding av hardere metaller som messing, 2-starts kuttere med flat mark kan anbefales.
Ved fresing av ekstremt hardt konstruksjonsstål eller stål av meget høy kvalitet, bruk tre eller fire blykuttere.
Enkelstartskutter i tverrsnitt
En kniv etterlater en stor åpen plass
for fjerning av brikker
Tre-starts kutter i tverrsnitt
Tre blader reduserer plassen betydelig
for fjerning av brikker
Forskjeller mellom en kutter og en gravør
Mange bruker konseptet "skjærer" og "gravør" som synonymer. Vi snakker imidlertid om to forskjellige verktøy.
En gravør er et enkelt verktøy, en sylinder delt i to, etterfulgt av baksliping.
Formen kan være annerledes; de vanligste er trekantede. I motsetning til freser, har de ikke en spiralformet sponrenne.
Verktøymateriale: HSS eller karbid?
Innen reklameteknologi brukes hovedsakelig karbidkuttere.
Karbid (HM) er et dyrt, kunstig produkt som er agglomerert fra fint pulver (f.eks. Wolfram-Carbid). Under agglomereringsprosessen blir formen på kutteren umiddelbart opprettet og endres deretter ikke (den blir bare skjerpet). Karbiden er ekstremt hard og slitesterk, men utsatt for vibrasjoner og støt. Det er viktig ved bruk av HM freser å ha en stabil, muligens tyngre og mer massiv maskin, en spindel med presis rotasjon og høykvalitets spennhylser. Materialet som skal freses må være fast og godt festet på maskinen.
Høyhastighetsstål (HSS) brukes først og fremst der karbiden er for følsom: ved fresing av rustfritt stål, på vinglete maskiner, eller i tilfeller hvor stivheten til festet ikke er tilstrekkelig sikret. HSS slites mye raskere, men det er mindre risiko for for tidlig svikt på grunn av dens seighet.
Levetiden til HSS-belagte kuttere økes kraftig. For eksempel, for titannitrid (TiN), økes levetiden med seks ganger.
Titan-Nitrid er betydelig stivere enn HSS og også tøffere enn HM. Med Titan-Nitrid-belegget varer HM-verktøy også lenger, selv om forskjellen i hardhet er ubetydelig.
Mer betydelig er dekningen reflektert i antall omdreininger og fôr. Det kan økes og forkortes på denne måten behandlingstiden. Ved fresing av aluminium forhindrer TiN den fryktinngytende bakingen av aluminiumet i kutteren. Belegget fungerer som teflon i en panne (sponene glir)
Hastighet og optimal fôring
De viktigste parametrene ved fresing er antall omdreininger og mate. Dataene i tabellen er i tråd med de fleste kutterprodusentenes anbefalinger. (Hvis du er i tvil, spør leverandøren hvilke moduser de anbefaler for produktet deres).Ta først den anbefalte kuttehastigheten for materialet som behandles og bruk den i formelen for å beregne antall omdreininger.
Hvis det brukes en maskin som ikke er veldig stiv, bestemmes antall omdreininger i det øvre området, og fôret i det nedre området. Hvis antall omdreininger er kjent, beregnes fôret ved hjelp av formelen.
I prinsippet vurderes det: Jo høyere skjærehastighet (vc = p * d * n), jo jevnere blir overflaten. Imidlertid øker også kutterens sløvhet med skjærehastigheten.
Beregningsprosedyre:
1. Antall omdreininger n:
Velg skjærehastighet vc fra bordet. (Hvis skjærehastigheten til materialet varierer mye, sjekk med manualene).
Basert på dataene, beregne antall spindelomdreininger
N = (vc *1000) / (3,14 * d)
F = n*fz*z
fz = mating per 1 tann
z = antall kniver
Eksempel:
Du ønsker å frese hardt aluminium, med en 3 mm diameter 2-starts kutter. Fra tabellen finner du: vc = 100...200 m/min. Fra dette regner du ut:Maks. antall omdreininger: n = (200 * 1000) / (3,14 * 3) = 200 000 / 9,42 = 21.230 U/min
Tilsvarende feed: f = 21230 * 0,04 * 2 = 1698 mm/minHøye matehastigheter - spesielt i metaller - krever en stabil og stillegående maskin. I tillegg bør ikke spordybden være for stor (ca. 1 * d 1).
For mindre stabile maskiner eller med økt fresedybde, beregnes modusen som følger:Maks. hastighet:
n = (200 * 1000) / (3,14 * 3) = 200 000 / 9,42 = 21.230 U/min(som ovenfor)
Min. antall omdreininger: n = (100 * 1000) / (3,14 * 3) = 100 000 / 9,42 = 10,615 U/min
Tilsvarende feed (minimum): f = 10615 * 0,04 * 2 = 849 mm/minDu kombinerer n=21230 U/min og f=849 mm/min.
Motbevegelse og synkronisert bevegelse
Slik lages de forskjellige kantene på kuttet:Bladet går inn fra vindsiden inn i materialet. Ved bevegelseskontrollområdet løper kutteren mot materialet. Tykkelsen på brikken vil være på grunnlag av maten inn i materialet er stadig større. I det synkrone området løper kutteren med materialet, spontykkelsen reduseres for å gå ut. Det skraverte området viser den relative spontykkelsen ved hver sponposisjon per omdreining. Bladet i motbevegelsen "tar" hele tiden materiale, mens det i den synkrone bevegelsen bare tas inn en liten mengde rett før bladet kommer ut i luften. Derfor «bryter» ofte det siste stykket så å si. Dette er grunnen til at den motsatte siden av bevegelsen alltid er jevnere enn den synkrone siden.
Hvilken kutter for hvilket materiale | 1-ledelse | 2-ledd | 3-veis | |||
ujevn | rent | ujevn | rent | ujevn | rent | |
trematerialer | ||||||
Bartre (furu) | ++ | 0 | +(+) | 0 | 0 | - |
Massiv (eik, bøk), kryssfiner, MDF | +(+) | 0 | ++ | 0 | +(-) | - |
plast | ||||||
PVC, polystyren, teflon, skum | ++ | + | + | 0 | - | -- |
Duroplast, Materialer med bakelitt (sponplater) | + | + | ++ | + | + | - |
Plexiglas helles | ++ | + | +(+) | - | 0 | - |
Metaller | ||||||
Myk aluminium (Alucobond) | ++ | + | + | 0 | - | -- |
Stivt aluminium (Floxal) | 0 | + | + | ++ | 0 | + |
Messing, bronse, kobberlegeringer | -- | - | 0 | +(-) | + | ++ |
Konstruksjonsstål | -- | -- | - | + | - | ++ |
stål av høy kvalitet | -- | -- | -- | - | -- | + |
++ Veldig bra + Bra 0 Tilfredsstillende |
- Dårlig -- Passer ikke |
Ved bearbeiding av harde stålkvaliteter brukes 4 eller flere blader.
Delvis eller full bruk dette materialet kun etter avtale, og med obligatorisk kildehenvisning
Ved virksomheter som omfatter underavdelinger som driver overflatebehandling av arbeidsstykker, på grunnlag av normative dokumenter Det utarbeides spesielle kart, som veileder operatøren i produksjonen av en bestemt del. Selv om i noen tilfeller (for eksempel nytt utstyr, verktøy), må freseoperatøren bestemme nyansene til teknologiske operasjoner på egen hånd. Hvis en laveffektsmaskin betjenes hjemme, desto mer er det som regel ingen offisielle tips tilgjengelig.
Denne artikkelen hjelper ikke bare med å forstå grunnlaget som skjæremodusen beregnes på under fresing og valget av passende verktøy, men gir også praktiske råd, som er tilstrekkelig for å behandle deler på husholdningsnivå.
Til de som mer assosiert med metaller, for en mer detaljert bekjentskap med nyansene til fresing, bør du referere til læreboken "Metal Cutting Machines" - 2003, Cherpakov B.I., Alperovich T.A. Fremgangsmåten for å beregne skjæreforhold er også godt beskrevet i ulike manualer. For eksempel i retningslinjer fra 2000 (MGAU - Kolokatov A.M., Bagramov L.G.).
Det særegne ved fresing er at skjærekantene bare kommer i direkte kontakt med materialet periodisk. Som et resultat - vibrasjoner, sjokkbelastninger og økt slitasje på kuttere. Den mest effektive modusen anses å være den der følgende parametere er optimalt kombinert - dybde, mating og skjærehastighet uten at det går på bekostning av nøyaktigheten og kvaliteten på behandlingen. Dette er det som gjør det mulig å redusere kostnadene for den teknologiske operasjonen betydelig og øke produktiviteten.
Det er umulig å forutse bokstavelig talt alle nyansene til fresing. Emnene som skal behandles er forskjellige i struktur, dimensjoner og form; skjæreverktøy - ved deres geometri, design, tilstedeværelse / fravær av et beskyttende lag, etc. Alt som er oppgitt nedenfor når det gjelder skjæreforhold bør kun betraktes som en veiledning. For å klargjøre spesifikke freseparametere bør du bruke spesielle tabeller og referansedata.
Verktøyvalg
Dette refererer hovedsakelig til dens diameter. Hva er funksjonen ved å velge en kutter () for denne parameteren?
- Økning av diameteren øker automatisk kostnadene for verktøyet.
- Den gjensidige avhengigheten av de to indikatorene - hvis matingen øker, faller skjærehastigheten, da den er begrenset av strukturen til arbeidsstykket (se nedenfor).
Den optimale diameteren til kutteren anses å være slik at verdien tilsvarer (eller litt mer) den nødvendige kuttdybden. I noen tilfeller kan tykkere spon velges i 1 omgang, men dette gjelder kun materialer preget av lav tetthet. For eksempel polystyren eller noen tresorter.
Kuttehastighet
Avhengig av materialet i prøven, kan du fokusere på følgende indikatorer (m / min):
- tre, termoplast - 300 - 500;
- PVC - 100 - 250;
- rustfritt stål - 45 - 95;
- bronse - 90 - 150;
- messing - 130 - 320;
- bakelitt - 40 - 110;
- aluminium og dets legeringer - 200 - 420.
Kutterhastighet
Den enkleste formelen ser slik ut:
N (antall omdreininger) = 1000 Vc (ønsket skjærehastighet) / π D (kutterdiameter).
Fra et sikkerhetssynspunkt bør du ikke kjøre spindelen med maksimal hastighet. Dette betyr at kun på grunn av dette vil skjærehastigheten reduseres med ca. 10 - 15 %. Dette "tapet" kan delvis kompenseres ved å installere en kutter med større diameter. Dette øker farten noe. Hvis det ikke er noen passende for hånden, må du bestemme deg for - å bruke penger på nytt verktøy eller være fornøyd med mulighetene som fresemaskinen har. Igjen, alt dette kontrolleres bare av praksisen med å jobbe med spesifikt utstyr, men sunn fornuft anbefalingen er forståelig.
Innhopp
Vær nøye med denne freseparameteren!
Holdbarheten til kutteren og kvaliteten på arbeidsstykkebehandlingen avhenger av hvor tykt laget fjernes i en penetrasjon, det vil si med hver omdreining av spindelen. I dette tilfellet snakker de om en mating på 1 (2,3) tenner, avhengig av type verktøy (en-, to- eller trestarts kutter).
Anbefalte verdier for mating per tann er spesifisert av verktøyprodusenten. Freseoperatøren på dette punktet av skjæreregimet møter vanskeligheter hvis han jobber med kuttere "laget i Kina" eller en tvilsom (ukjent) opprinnelse. I de fleste tilfeller kan du fokusere på mateområdet (mm) 0,1 - 0,25. Denne modusen passer for nesten alle vanlige fresematerialer. I prosessen med å kutte vil det bli klart om det er nok eller litt å "legge til" (men ikke tidligere enn etter den første samtalen). Men mindre enn 0,1 bør ikke prøves, bortsett fra når du utfører smykkearbeid med mikromøller.
Start fresingen med en minimum mating på 0,1. I prosessen vil det bli tydelig hvor formbart materialet som behandles er foran en bestemt kutter. Dette vil eliminere muligheten for å bryte skjærekanten (tannen) og vil gjøre det mulig å foreta en nøyaktig "diagnose" av egenskapene til maskinen og verktøyet, spesielt hvis det er "fremmed" utstyr.
- Å overskride verdien av den optimale matingen er full av temperaturøkning i arbeidsområdet, dannelse av tykke spon og rask brudd på kutteren. For et verktøy med en diameter på mer enn 3 mm bør du begynne med 0,15, ikke mer
- Hvis det ikke er mulig å øke hastigheten på fresing av en del på grunn av optimal bruk av utstyrets evner, kan du prøve å installere en dobbeltrådskutter.
- Når du velger et verktøy, må det tas i betraktning at en økning i lengden på skjæredelen fører til en reduksjon i mating og en økning i vibrasjon.
- Du bør ikke strebe etter å øke prosesseringshastigheten ved å erstatte kutteren med en lignende, men med et stort antall tenner. Spon fra et slikt verktøy er verre, derfor fører det ofte til at kvaliteten på fresingen reduseres kraftig. I noen tilfeller, når sporene er helt fylt, begynner kutteren å jobbe "tomgang". Det er ingen vits i en slik erstatning.
Konklusjon
Fresing av høy kvalitet kan kun oppnås med erfaring. Spesifikt maskinverktøy + verktøy + praktisk erfaring, ferdigheter. Derfor bør du ikke stole blindt på selv tabelldata. For eksempel tar de ikke hensyn til graden av slitasje på kutteren som skal jobbes med. Du trenger ikke å være redd for å eksperimentere, men du bør alltid starte med minimumsverdien til parameterne. Når mesteren "føler" maskinen, kutteren og materialet som behandles, vil han selv bestemme i hvilken modus det er verdt å jobbe.
Hvorfor mattes en kutter raskt? Hva forårsaker forkulling av det bearbeidede materialet (sponplater, MDF eller tre) etter fresing? Hvorfor brenner kutteren? Hvordan forhindre at harpiks festes på skjærekantene på kutteren? Det er bare ett svar på spørsmålene ovenfor - rotasjonshastigheten (frekvensen) til kutteren er feil valgt.
Moderne freseutstyr for bearbeiding av laminerte sponplater eller MDF-plater er utstyrt med motorer som gjør det mulig å oppnå en spindelhastighet på over 20 000 rpm. På den ene siden påvirker dette produktiviteten til utstyret, da det øker hastigheten til verktøyet eller matehastigheten til arbeidsstykket. På den annen side øker kvaliteten på behandlingen: sannsynligheten for å heve haugen på MDF, utseendet på slitasje på treet og flis på den laminerte sponplaten reduseres.
Av vane, av uvitenhet, eller rett og slett av latskap, for ikke å bry deg med alle slags bruksanvisninger, prosesseringsmoduser og andre triks, settes rotasjonshastigheten til kutteren til det maksimale nivået der alle materialer behandles med alle tilgjengelige kuttere. Det er dette som ligger hovedårsaken alle problemer.
Faktum er at ved høy hastighet (frekvens) rotasjon av kutteren og lav matehastighet for arbeidsstykket, skjærekanten til kutteren mest gang den går på tomgang, og i stedet for å kutte av en annen brikke fra materialet som behandles, gnir den ubrukelig mot den. Alle vet hva som skjer som følge av friksjon - oppvarming. Dessuten, jo høyere rotasjonshastigheten til kutteren er, desto mer intens er friksjonen, og desto mer varmes kutteren opp.
Det ser ut til at det er noe spesielt? Vel, det er varmt. Hvis du tar den i håndflaten, så holder hånden ut. Hva blir det av metallet? Men fortsatt…
Hvorfor brenner kutteren og blir fort sløv
Varmen som følge av friksjonen fra kutteren på materialet blir gradvis jevnt fordelt over hele kroppen. Derfor, under kortvarig drift, føles oppvarming praktisk talt ikke. Under bearbeiding av materialer er det imidlertid ved skjærekantene at temperaturen når maksimale nivåer. Og jo høyere rotasjonshastigheten til kutteren er, jo større er friksjonen og oppvarmingen av kantene.
Dette er spesielt merkbart på kuttere med stor diameter. Her linjehastighet bevegelsen til den ytre delen av skjærekanten i forhold til materialet er mye høyere. Som et resultat blir kantene på kutteren varme opp og, etter avkjøling, mørkere med en blåaktig fargetone, og dette er et sikkert tegn på at metallet har blitt oppvarmet i den grad at det begynner å endre egenskapene. I vitenskapelige termer brenner karbonkomponenten ut i metallet, noe som gir det egenskapene til stivhet. Hvis du husker hvor myk og smidig en vanlig spiker blir, etter å ha vært i de varme kullene i en ovn eller en brann, er det lett å forestille seg hvilke nye egenskaper kutteren vil få som følge av overoppheting.
Det er verdt å legge til at når du skjerper en kutter, påvirker rotasjonshastigheten til slipeskiven eller verktøyets trykkgrad direkte oppvarmingen av kantene som skjerpes. Hvis du ikke bruker kjølevæske, vil ethvert karbidmetall bli til et vanlig jernstykke som kan deformeres etter liten belastning. Forresten, det er derfor arbeidslivet til kuttere, bor og sager etter sliping reduseres betydelig.
Hvorfor brenner materialet
Alt er veldig klart her: som et resultat av friksjonen fra kutteren på materialet, dannes en høy temperatur, under påvirkning av hvilken treet begynner å brenne ut. For å forhindre dette fenomenet, er det nødvendig å redusere hastigheten (frekvensen) av rotasjon av kutteren og øke matehastigheten til arbeidsstykket. Men disse handlingene bør utføres under forutsetning av at kutteren har beholdt sin skarphet. PÅ ellers, belastningen på den, eller kraftenheten, vil øke betydelig, noe som kan føre til sammenbrudd.
Harpiks fester seg til kutteren
Mange tresorter inneholder harpiks. Ved fremstilling av platetrematerialer, som sponplater og MDF, brukes i tillegg formaldehydharpikser. I prosessen med mekanisk bearbeiding av disse materialene, oppvarmet av friksjon, koker harpikspartikler, faller på tennene til skjæreverktøyet og holder seg til dem sammen med støv. Vanligvis forårsaker dette ikke betydelige problemer hvis matemodusen til arbeidsstykket og skjærehastigheten til verktøyet er valgt riktig. Ellers, når en av parametrene beregnes feil, er rotasjonshastigheten til kutteren for høy og behandlingen utføres med lav hastighet, vises et mørkt harpiksbelegg på verktøykutterne. Dessuten, jo sterkere denne uoverensstemmelsen, jo raskere dannes den. Samtidig reduseres kvaliteten på behandlingen, spon vises på de laminerte overflatene, treet begynner å brenne, verktøyet får en ekstra belastning, overopphetes raskt og mislykkes. Dette er grunnen til at valget av kutterhastighet og materialmatingshastighet er så viktig.
I tillegg til riktig beregning av modusen for bearbeiding av materialer, er det nødvendig å ta hensyn til omsorgen for skjæreverktøyet, det vil si å rense de dannede harpiksavleiringene i tide, eller vaske det av med vanlig varmt vann .
Beregning av rotasjonshastigheten (frekvensen) til kutteren
For å foreta en korrekt beregning av rotasjonshastigheten til kutteren og hastigheten på dens bevegelse, er det nødvendig å ta hensyn til mange faktorer, inkludert de fysiske og mekaniske egenskapene til materialet og verktøyet, dybden og bredden på behandlingen, etc. .
På den annen side er materialer som MDF og sponplater mye lettere å bearbeide enn for eksempel ulike metaller. Derfor kan grunnlaget utelukkende tas som en indikator på kvaliteten på behandlingen, det vil si tilstedeværelsen av ruhet, rygger, flis og riper på den behandlede overflaten.
For mer eller mindre høykvalitets bearbeiding av sponplater av laminerte plater, er det nødvendig at matingsmengden per kuttertann (eller ganske enkelt tykkelsen på sponene som kommer ut under kutteren) er 0,05 - 0,15 mm. En konvensjonell kutter med to kutter bør således kutte 0,1 - 0,3 mm per omdreining, og 1500 - 4500 mm per 15 000 omdreininger. Det vil si at matehastigheten til materialet til kutteren, ved 15 000 rpm, skal være 1,5 - 4,5 m / min, eller 25 - 75 mm / s.
Hvis du ønsker å maskinere med lav matingshastighet, for eksempel når du arbeider manuell ruter, så kan beregningen av rotasjonshastigheten til kutteren gjøres basert på bevegelseshastigheten til ruteren, og gjør beregninger i omvendt rekkefølge. La oss si at materialet behandles med en hastighet på 10 mm/sek, eller 600 mm/min. Med en matingshastighet per tann lik 0,1 mm og en to-kutter, vil den nødvendige rotasjonshastigheten til kutteren være 600/(0,1)× 2)=3000 rpm.
Sikkerhetsregler ved arbeid med kuttere
Som regel legger produsenter av freseutstyr og verktøy sikkerhetsinstruksjoner til produktene sine og angir anbefalte driftsmoduser for freser. Tabellen nedenfor viser de sikre parametrene for rotasjonshastigheten til kutteren avhengig av diameteren.
Kutterdiameter, mm |
Maksimal rotasjonshastighet for kutteren, rpm |
opptil 25 |
24000 |
26 – 50 |
18000 |
51 – 63 |
16000 |
64 – 75 |
14000 |
76 – 87 |
12000 |
VALG AV KJÆREMODUS FOR FRESING
§ 78. BETINGELSER SOM BESTEMMER VALGET AV KUTTEMODUS
Konseptet med den mest fordelaktige kuttemodusen
Den mest fordelaktige bør betraktes som en slik kuttemodus når du arbeider med Fres, hvor skjærehastigheten, matingen og dybden til skjærelaget er mest vellykket kombinert, og gir, under gitte spesifikke forhold (dvs. tar hensyn til den beste bruken av skjæreegenskapene til verktøyet, hastighet og kraftkapasiteter til maskinen) , den høyeste arbeidsproduktiviteten og den laveste kostnaden for operasjonen, underlagt de spesifiserte tekniske forholdene når det gjelder nøyaktighet og renslighet av behandlingen.
Forskningsinstituttet for arbeidskraft i statskomiteen for ministerrådet for USSR for arbeidskraft og lønn utviklet med deltakelse av de største innenlandske forskerne, tatt i betraktning praktisk anvendelse i produksjonsforhold, skjæreforhold ved fresing med verktøy laget av høyhastighetsstål og harde legeringer. De kan tjene som startdata ved tildeling av skjærehastigheter og minuttmatinger.
Disse standardene er tilgjengelige ved hvert anlegg og fungerer som en retningslinje for utviklingen teknologisk prosess og lage operasjonskart som det på s. 204-205. Imidlertid er skjærehastighetene og minuttmatingene gitt i dem ikke begrensende og kan i noen tilfeller blokkeres av fresere hvis de bruker mer produktive verktøy eller arbeider på kraftigere og stivere maskiner.
På den annen side, unge, det vil si nybegynnere og som ikke har tilstrekkelig erfaring, fresere er ikke alltid i stand til å jobbe ved de begrensende skjæreforholdene, derfor er mindre alvorlige skjæreforhold gitt for dem i Young Milling Operator's Handbook, med utgangspunkt i dette, det er nødvendig, som avansert opplæring, flytte til strengere.
For å introdusere nye moduser selv, må du kjenne rekkefølgen og rekkefølgen til innstilling av fresemoduser.
Materiale til skjæredelen av kutteren
Den avgjørende faktoren som bestemmer nivået av skjæremodus er materialet til skjæredelen av kutteren. Som nevnt ovenfor lar bruken av kuttere med hardmetallskjær deg jobbe med høye skjærehastigheter og høye matinger sammenlignet med kuttere laget av høyhastighetsstål; som vi vil se nedenfor, gjør hardmetallkuttere det mulig å øke produktiviteten med to til tre ganger sammenlignet med høyhastighetskuttere. Derfor er det tilrådelig å bruke hardmetallkuttere til nesten alle typer fresing; en hindring for bruken av dem kan være den utilstrekkelige kraften til utstyret eller de spesifikke egenskapene til materialet til arbeidsstykket som behandles.
Men i noen tilfeller er bruken av karbon, legert verktøy og høyhastighetsstål for den skjærende delen av freser rasjonell, spesielt når renheten til den bearbeidede overflaten og nøyaktigheten til den resulterende overflaten til delen er viktigere enn hastigheten på arbeidet.
Geometriske parametere for skjæredelen
En like viktig faktor som påvirker valget av skjæreforhold er de geometriske parameterne til skjæredelen av kutteren (skjærevinkler, dimensjoner og form på tannen), som ofte kalles kuttergeometri. Tidligere, i § 7, ble betydningen og påvirkningen av hvert av elementene i kuttertanngeometrien i skjæreprosessen vurdert; her vil vi vurdere de anbefalte geometriske parametrene til skjæredelen av kuttere laget av P18 høyhastighetsstål og med harde legeringsplater.
I tabellen. 35 og 36 viser de anbefalte verdiene for de geometriske parameterne for sylindriske, ende-, skive-, avskjærings-, ende- og formkuttere laget av høyhastighetsstål.
Tabell 35
Geometriske parametere for skjæredelen av kuttere laget av P18 høyhastighetsstål
I. Fremre hjørner

II. Bakre hjørner

III. Lednings- og overgangsvinkler

Notater. 1. For sylindriske kuttere med en tannvinkel på mer enn 30°, er skråvinkelen γ ved bearbeiding av stål σ b mindre enn 60 kg/mm 2 er tatt lik 15°.
2. For profilkuttere med skråvinkel større enn 0°, er en konturkorrigering nødvendig ved bearbeiding av presise profiler.
3. Når du behandler varmebestandige stål med endefreser, ta de øvre verdiene av frontvinklene, ende og sylindriske - nedre og midtre.
4. La et sirkulært slipt bånd med en bredde på ikke mer enn 0,1 på baksiden av kutterne når du skjerpes mm. Tennene til kuttere med slisse (spalte) og avtakbare (sirkelsag) slipes uten å etterlate et bånd.

I tabellen. 37 - 40 viser de anbefalte verdiene for de fremre og bakre vinklene, hoved-, hjelpe- og overgangsvinklene i planen, helningsvinklene til skjærekanten og spiralformede spor, radius på toppen av flaten, sylindrisk, ende og skivekuttere med hardmetallskjær.
Fresene som brukes til å behandle de fleste arbeidsstykker, leveres vanligvis av verktøyfabrikker med geometriske parametere som er i samsvar med GOST, og det er nesten umulig for en fresemaskin, i motsetning til en dreier og høvel, å endre skjærevinklene til freser ved å skjerpe. Som et resultat, gitt i tabell. 35 - 40 vil de geometriske parametrene til den skjærende delen av kutterne hjelpe mølleren til å velge riktig kutter som passer for den gitte behandlingen fra standardkutterne som er tilgjengelige i verktøykammeret til opplærings- og produksjonsverkstedet. Hovedformålet med disse tabellene er imidlertid å gi anbefalinger i tilfelle mølleren selv ønsker å bestille standard- eller spesialfreser med optimale geometriske parametere for denne bearbeidingen.
Tabell 37
Geometriske parametere for den skjærende delen av endefreser med karbidinnsatser

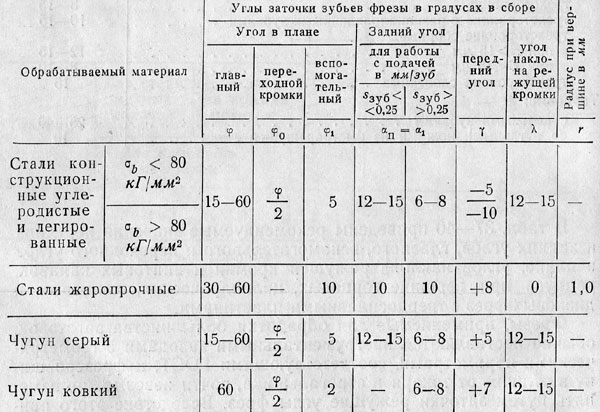
Merk. Små blyvinkler φ = 15 - 30° bør brukes ved maskinering på stive maskiner for grovbearbeiding med små skjæredybder eller etterbearbeiding med lave krav til renslighet og nøyaktighet til den bearbeidede overflaten.
Tabell 38
Geometriske parametere for den skjærende delen av sylindriske kuttere med spiralformede blader av hard legering


Merk. På baksiden av tannen langs skjærekanten, et bånd med en bredde på ikke mer enn 0,1 mm.
Tabell 39
Geometriske parametere for skjæredelen av endefreser med wolframkarbidinnsatser i bearbeiding av strukturelt karbon og legert stål


* Med lav stivhet av systemet maskin - feste - verktøy - del og med store spondeler ( PÅ mer D; t mer enn 0,5 D), samt når du arbeider med lave hastigheter kutte ved utilstrekkelig spindelhastighet ( v mindre enn 100 m/min) rakevinkelen γ er tilordnet positiv + fra 0 til +8°.
**Større verdier for bløtt stål, mindre verdier for hardt stål.
Fresebredde og -dybde
Fresebredde spesifisert på deltegningen. Ved bearbeiding av flere arbeidsstykker som er klemt parallelt i en spennanordning, er fresebredden lik bredden på alle arbeidsstykker. Ved fresing med sett med freser er fresebredden lik den totale bredden på alle sammenfallende flater.
Fresedybde(skjæredybde, kuttet lagtykkelse) angis som avstanden mellom maskinerte og maskinerte overflater. For å redusere behandlingstiden anbefales det å utføre fresing i én omgang. Med økte krav til nøyaktighet og renslighet av den maskinerte overflaten, utføres fresing i to trinn - groving og etterbehandling. I noen tilfeller, ved fjerning av store kvoter eller ved fresing på maskiner med utilstrekkelig kraft, er bearbeiding i to grovbearbeiding mulig.
Tabell 40
Geometriske parametere for den skjærende delen av skivekuttere med karbidinnsatser


Ved fresing av stålsmiing, stål- og støpejernsstøpegods dekket med avleiring, støpeskorpe eller forurenset med støpesand, må fresedybden være større enn tykkelsen på det forurensede laget slik at kuttertennene ikke etterlater svarte kutt på den bearbeidede overflaten, siden gliding langs skorpen påvirker kutteren negativt, og akselererer slitasje på skjærekanten.
For de vanligste fresekassene anbefales det å utføre grovbearbeiding på stål med en skjæredybde på 3-5 mm, og på stål og støpejern- med skjæredybde 5-7 mm. For ferdigfresing ta en skjæredybde på 0,5-1,0 mm.
kutter diameter
Diameteren på kutteren velges hovedsakelig avhengig av bredden på fresen PÅ og skjæredybde t. I tabellen. 41 viser dataene for valg av sylindriske kuttere, i tabell. 42 - endefreser og i tabell. 43 - skivekuttere.

* Bruk prefabrikkerte sammensatte kuttere i henhold til GOST 1979-52.


Vurder effekten av kutterdiameter på freseytelsen.
Diameteren på den sylindriske kutteren påvirker tykkelsen på kuttet: jo større diameteren til kutteren D jo tynnere kuttet er; med samme forsyning s tann og fresedybde t.
På fig. 327 viser et snitt oppnådd med samme fresedybde t og arkivering s tann, men med forskjellige diametre av kuttere. Kuttet oppnådd med en større diameter av kutteren (fig. 327, a) har en mindre tykkelse enn kuttet med en mindre; kutterdiameter (fig. 327, b).

Siden det spesifikke trykket øker med en reduksjon i tykkelsen på det kuttede laget en naib (se tabell 38), er det mer lønnsomt å arbeide med tykkere skiver, dvs. ceteris paribus, med en mindre kutterdiameter.
Diameteren på kutteren påvirker hvor mye bane kutteren må bevege seg i én gang.
På fig. 328 viser banen som kutteren må gå gjennom ved bearbeiding av en del med lengde L; i fig. 329 - banen som planfresen må gå gjennom asymmetrisk fresing av et arbeidsstykke med en lengde L; i fig. 330 - banen som kakeskjæreren må gå gjennom ved symmetrisk fresing av et arbeidsstykke med en lengde L.

Innmatingsverdi l(innkuttet bane):
når du arbeider med sylindriske, skive, avskårne og formede kuttere avhenger av diameteren på kutteren D fresedybde t og uttrykkes med formelen
ved arbeid med endefreser og endefreser for asymmetrisk fresing avhenger av diameteren på kutteren D fresebredde PÅ og uttrykkes med formelen
ved arbeid med planfreser når symmetrisk fresing avhenger av kutterens diameter D fresebredde PÅ og uttrykkes med formelen
Overskridelsesverdi l 1 velges avhengig av diameteren på kutteren innen 2-5 mm.
Derfor, for å redusere innsettings- og overløpsveien til kutteren, dvs. for å redusere maskinens tomgang, er det tilrådelig å velge en mindre diameter på kutteren.
På slutten av boken, i vedlegg 2 og 3, er det verditabeller for stupebanen og overløpet av kutterne.
Kutterdiameteren påvirker verdien dreiemoment: Jo mindre kutterens diameter er, desto mindre dreiemoment må maskinspindelen tilføres.
Derfor ser valget av en kutter med mindre diameter ut til å være mer passende. Men med en reduksjon i diameteren til kutteren, er det nødvendig å velge en tynnere, dvs. mindre stiv fresedor, så det er nødvendig å redusere belastningen på doren, dvs. å redusere tverrsnittet av det kuttede laget .
Innhopp
Mate kl grovarbeid avhenger av materialet som behandles, materialet til skjæredelen av kutteren, drivkraften til maskinen, stivheten til systemmaskinen - festet - verktøyet - delen, bearbeidingsdimensjoner og slipevinkler til kutteren.
Mate kl etterbehandling avhenger av klassen for overflaterenhet som er angitt på detaljtegningen.
Hovedinngangen ved valg av fôr for grovfresing er fôret s tann.
For flatfreser med fôrvalg s tannen gir en måte å installere kutteren i forhold til arbeidsstykket, som bestemmer vinkelen på kuttertannen som møter arbeidsstykket og tykkelsen på de kuttede sponene når kuttertannen kommer inn og ut fra kontakt med arbeidsstykket. Det er fastslått at for en frontkarbidkutter oppnås de mest gunstige forholdene for å kutte en tann i et arbeidsstykke når kutteren er plassert i forhold til arbeidsstykket, som i fig. 324, c, dvs. når kutteren er forskjøvet i forhold til arbeidsstykket med en mengde FRA = (0,03 - 0,05)D. En slik forskyvning av kutteraksen gjør det mulig å øke matingen per tann mot matingen under symmetrisk fresing (fig. 324, a) av støpejern og stål med en faktor to eller mer.
I tabellen. Tabell 44 viser anbefalte mate for grovfresing med karbidplatefreser for disse to tilfellene.

Notater. 1. De viste grovmatingshastighetene er basert på standard freser. Når du arbeider med ikke-standard kuttere med økt antall tenner, bør mateverdiene reduseres med 15 - 25%.
2. I den første driftsperioden til kutteren til slitasje lik 0,2-0,3 mm renheten til den bearbeidede overflaten under finfresing reduseres med omtrent en klasse.

Merk. Ta store matinger for mindre skjæredybder og bearbeidingsbredde, mindre matinger for store dybder og bearbeidingsbredder.

Merk. Mater er gitt for en stiv system maskin - feste - verktøy - del.
Ved planfresing med karbidfreser påvirker også forføringsvinkelen φ matingshastigheten. Innleveringer gitt i tabell. 44 er beregnet for kuttere med φ = 60 - 45°. Ved å redusere foringsvinkelen φ til 30° kan du øke matingen med 1,5 ganger, og å øke vinkelen φ til 90° krever en 30 % reduksjon i matingen.
Mater for etterbehandling med karbidkuttere gitt i tabell. 44 er gitt for en omdreining av kutteren, siden matingene per tann er for små. Fôr gis avhengig av renhetsklassen til den behandlede overflaten i samsvar med GOST 2789-59.
I tabellen. 45 viser anbefalt mating per kuttertann for grovfresing av plan med sylindrisk, flate og skive trekantkuttere fra høyhastighetsstål P18.
I tabellen. 46 viser matinger under etterfresing av plan med sylindriske kuttere laget av P18 høyhastighetsstål, og i tabell. 47 - ved ferdigfresing av plan med plan- og skive tresidige freser laget av P18 høyhastighetsstål. På grunn av de små verdiene for mating per tann på kutteren, oppnådd under finfresing, i tabellen. 46 og 47 er matinger per omdreining av kutteren.
Det bør huskes at du arbeider med feedene som er angitt i tabellen. 44-47, setter en uunnværlig betingelse for tilstedeværelsen av et minimum utløp av tennene til kutteren (se tabell. 50).

Merk. Mater er gitt for en stiv systemmaskin - feste - verktøy - del ved fresing med freser med en hjelpevinkel i planen φ 1 = 2 °; for kuttere med φ 1 = 0 kan mate økes med 50 - 80 %.