À catégorie:
Travaux de fraisage
Sélection de modes de fraisage rationnels
Le choix d'un mode de fraisage rationnel sur une machine donnée signifie que pour les conditions de traitement données (matériau et qualité de la pièce, son profil et ses dimensions, tolérance de traitement), il est nécessaire de sélectionner le type et la taille optimaux de la fraise, la qualité du matériau et paramètres géométriques de la partie coupante de la fraise, liquide de lubrification et de refroidissement et attribuer des valeurs optimales pour les paramètres de mode de coupe suivants : B, t, sz. v, p, Ne, Tm.
De la formule (32), il résulte que les paramètres B, t, sz et v ont la même influence sur la productivité volumétrique de broyage, puisque chacun d'eux est inclus dans la formule au premier degré. Cela signifie que si l’un d’entre eux est multiplié par exemple par deux (les autres paramètres restant inchangés), la productivité volumétrique doublera également. Ces paramètres ont cependant loin d'avoir la même influence sur la durée de vie de l'outil (voir § 58). Par conséquent, compte tenu de la durée de vie de l'outil, il est plus rentable, tout d'abord, de choisir les valeurs maximales admissibles des paramètres qui ont un effet moindre sur la durée de vie de l'outil, c'est-à-dire dans l'ordre suivant : profondeur de passe, avance par dent et vitesse de coupe. Par conséquent, la sélection de ces paramètres de mode de coupe lors du fraisage sur cette machine doit commencer dans le même ordre, à savoir :
1. La profondeur de coupe est attribuée en fonction de la surépaisseur de traitement, des exigences en matière de rugosité de surface et de puissance de la machine. Il est conseillé de supprimer la surépaisseur de traitement en un seul passage, en tenant compte de la puissance de la machine. En règle générale, la profondeur de coupe lors du fraisage grossier ne dépasse pas 4 à 5 mm. Lors de l'ébauche avec surfaçage fraises en carbure(têtes) sur des fraiseuses puissantes, il peut atteindre 20-25 mm ou plus. Une fois le fraisage terminé, la profondeur de coupe ne dépasse pas 1 à 2 mm.
2. L'aliment maximum autorisé dans les conditions de transformation est attribué. Lors de l'établissement des avances maximales autorisées, il convient d'utiliser des avances par dent proches de la « cassure ».
La dernière formule exprime la dépendance de l'avance par dent sur la profondeur de fraisage et le diamètre de la fraise. La valeur de l'épaisseur de coupe maximale, c'est-à-dire la valeur du coefficient constant I c dans la formule (21), dépend des propriétés physiques et mécaniques du matériau traité \ (pour un type et une conception donnés de la fraise). Les valeurs des aliments maximum autorisés sont limitées par divers facteurs :
a) pendant l'ébauche - la rigidité et la résistance aux vibrations de l'outil (avec une rigidité et une résistance aux vibrations suffisantes de la machine), la rigidité de la pièce et la résistance de la partie coupante de l'outil, par exemple une dent de coupe, un volume insuffisant de cannelures à copeaux, par exemple pour les fraises à disques, etc. Ainsi, l'avance par dent lors du fraisage grossier de l'acier avec des fraises cylindriques avec des couteaux à plaquettes et de grandes dents est sélectionnée dans la plage de 0,1 à 0,4 mm/dent, et lors du traitement de la fonte jusqu'à 0,5 mm/dent ;
b) pendant le traitement de finition - rugosité de la surface, précision dimensionnelle, état de la couche de surface, etc. Lors de la finition du fraisage de l'acier et de la fonte, une avance relativement faible par dent de fraise est attribuée (0,05 à 0,12 mm/dent).
3. La vitesse de coupe est déterminée ; puisqu'elle a le plus grande influence sur la durabilité de l'outil, celui-ci est alors sélectionné en fonction de la norme de durabilité acceptée pour cet outil. La vitesse de coupe est déterminée par la formule (42) ou à partir de tableaux de normes de modes de coupe en fonction de la profondeur et de la largeur de fraisage, de l'avance par dent, du diamètre de la fraise, du nombre de dents, des conditions de refroidissement, etc.
4. La puissance de coupe effective Ne pour le mode sélectionné est déterminée à l'aide des tableaux de normes ou de formule (39a) et comparée à la puissance de la machine.
5. Par régler la vitesse coupe (i, ou i^), le niveau de vitesse de broche de la machine le plus proche parmi ceux disponibles sur une machine donnée est déterminé à l'aide de la formule (2) ou selon le graphique (Fig. 174). A partir du point correspondant à la vitesse de coupe acceptée (par exemple 42 m/min), effectuez ligne horizontale, et à partir du point avec la marque du diamètre de coupe sélectionné (par exemple, 110 mm) - vertical. Au point d'intersection de ces lignes, le niveau de vitesse de broche le plus proche est déterminé. Ainsi, dans l'exemple représenté sur la Fig. 172, lors du fraisage avec une fraise d'un diamètre de D = 110 mm avec une vitesse de coupe de 42 m/min, la vitesse de rotation de la broche sera égale à 125 tr/min.
Fig. 174 Nomogramme de la vitesse de rotation de la fraise
6. L'alimentation minute est déterminée à l'aide de la formule (4) ou selon le calendrier (Fig. 175). Ainsi, lors du fraisage avec une fraise D = 110 mm, z = 10 à sz = 0,2 mm/dent et n = 125 tr/min, l'avance minute selon le planning est déterminée comme suit. A partir du point correspondant à l'avance par dent sg = 0,2 mm/dent, on trace ligne verticale jusqu'à ce qu'elle croise une ligne inclinée correspondant au nombre de dents de coupe r = 10. À partir du point résultant, nous traçons une ligne horizontale jusqu'à ce qu'elle croise une ligne inclinée correspondant à la vitesse de broche acceptée l = 125 tr/min. Ensuite, tracez une ligne verticale à partir du point résultant. Le point d'intersection de cette ligne avec l'échelle inférieure des avances minutes disponibles sur une machine donnée détermine le pas d'avances minutes le plus proche.
7. Le temps machine est déterminé.
Le temps des machines. Le temps pendant lequel le processus d'élimination des copeaux se produit sans la participation directe du travailleur est appelé temps machine (par exemple, pour le fraisage du plan de la pièce à partir du moment où l'avance longitudinale mécanique est activée jusqu'à son arrêt).
Riz. 1. Nomogramme de l'alimentation minute
L'augmentation de la productivité lors du traitement sur les machines à couper les métaux est limitée par deux facteurs principaux : les capacités de production de la machine et les propriétés de coupe de l'outil. Si les capacités de production de la machine sont faibles et ne permettent pas d'utiliser pleinement les propriétés de coupe de l'outil, alors la productivité d'une telle machine ne représentera qu'une petite partie de la productivité possible avec une utilisation maximale de l'outil. Dans le cas où les capacités de production de la machine dépassent largement les propriétés de coupe de l'outil, la productivité maximale possible avec un outil donné peut être atteinte sur la machine, mais les capacités de la machine ne seront pas pleinement utilisées, c'est-à-dire la puissance de la machine, les forces de coupe maximales admissibles, etc. d. Les cas optimaux du point de vue de la productivité et de l'utilisation économique de la machine et de l'outil seront les cas où la capacité de production de la machine et les propriétés de coupe de l'outil coïncident ou sont proche l'un de l'autre.
Cette condition est à la base des soi-disant caractéristiques de production des machines, qui ont été proposées et développées par le prof. A.I. Kashirin. La caractéristique de production d'une machine est un graphique des capacités de la machine et de l'outil. Les caractéristiques de production facilitent et simplifient la détermination des conditions de coupe optimales lors du traitement sur une machine donnée.
Les propriétés de coupe d'un outil particulier sont caractérisées par les modes de coupe autorisés pendant le processus de traitement. La vitesse de coupe dans des conditions de traitement données peut être déterminée par la formule (42, a). En pratique, on le trouve à partir du tableau des modes de découpe, qui sont donnés dans les ouvrages de référence d'un normalisateur ou d'un technologue. Cependant, il convient de noter que les normes relatives aux modes de coupe, tant pour le fraisage que pour d'autres types de traitement, sont élaborées sur la base des propriétés de coupe de l'outil pour divers cas traitement (type et taille de l'outil, type et qualité du matériau de la pièce coupante, matériau à traiter, etc.), et ne sont pas liés aux machines sur lesquelles le traitement sera effectué. Étant donné que les capacités de production des différentes machines sont différentes, le mode de traitement optimal pratiquement réalisable sur différentes machines sera différent pour les mêmes conditions de traitement. Les capacités de production des machines-outils dépendent principalement de la puissance effective de la machine, de la vitesse de rotation, des avances, etc.
Riz. 2. Plongée et surcourse
Les caractéristiques de production des fraises pour le cas des fraises coupantes ont été développées par le professeur A. I. Kashirin et l'auteur.
Le principe de construction des caractéristiques de production des fraiseuses (nomogrammes) pour travailler avec des fraises en bout est basé sur un joint solution graphique deux équations qui caractérisent la dépendance de la vitesse de coupe vT selon la formule (42) à -Bz' = const, d'une part, et de la vitesse de coupe et de la puissance admissible de la machine, d'autre part. La vitesse de coupe vN peut être déterminée par la formule
Riz. 3. Caractéristiques de production de la fraiseuse cantilever 6P13
Modes de coupe
Fraises à gauche
Pourquoi plutôt que la meunerie d'aliments pour animaux, c'est mieux.Problème: Le cutter à 2 cannelures fait fondre la mousse PVC.
Solution: choisissez un nombre de tours inférieur ou fraisez avec un coupe-fil à un seul fil. (Image)
1. Plonger :
La fraise doit pouvoir pénétrer dans le matériau avec son extrémité (fonction perçage).
2. Avant-garde :
En règle générale, les bords du passage diffèrent les uns des autres. Le côté opposé du mouvement est « plus beau » que le côté de la synchronicité. Ceci est particulièrement visible lors de l'utilisation d'une fraise à 1 cannelure, ainsi que lors du fraisage de l'aluminium.
Conseil; Fraisez les contours intérieurs dans le sens des aiguilles d'une montre, les contours extérieurs dans le sens inverse des aiguilles d'une montre. De cette façon, le « mauvais » côté finit dans les jetons
3. Élimination des copeaux :
Les copeaux doivent être évacués rapidement afin que les cavités de la fraise ne se remplissent pas et que la fraise se brise. Plus le fraisage est profond et rapide, plus il est difficile d'éliminer les copeaux. Instructions : Ne pas fraiser à une profondeur supérieure au double ou au triple du diamètre de la fraise. Traversez des rainures plus profondes en plusieurs passes. Lors du fraisage du polystyrène et d'autres plastiques, il est judicieux d'utiliser des fraises avec des rainures polies pour un meilleur rendement.
4. Dissipation thermique/lubrification :
La fraise ne doit pas devenir trop chaude : d'une part, un outil avec une température trop élevée perd ses propriétés, d'autre part - encore plus critique - des copeaux de plastique et d'aluminium peuvent « coller » dans les rainures, empêchant ainsi l'élimination des copeaux. et, par conséquent, entraîner la rupture de la fraise. Lors du traitement des métaux, il est impératif de recommander un lubrifiant. Remarque : L'aluminium et les métaux non ferreux peuvent être broyés avec de l'alcool ou des émulsions spéciales ; de l'eau savonneuse peut être utilisée lors du traitement du plexiglas.
5. Risque de casse :
croît de manière linéaire avec l'augmentation de l'alimentation et l'augmentation de la profondeur d'immersion : une double alimentation signifie un risque fractionnaire double, une profondeur d'immersion double signifie un risque fractionnaire multiplié par huit.
Directions:
Il est préférable de fraiser en plusieurs passes, moins profondément et avec une avance plus élevée. Utilisez une fraise avec la longueur de coupe la plus courte possible. Serrez-le autant que possible. Règle générale: un tiers est serré dans le mandrin (pince de serrage) longueur totale coupeurs.
La bonne coupe amène les chips vers le haut.
Une fraise à droite facilite l'évacuation des copeaux vers le haut, ce qui est bon pour une élimination continue ; cependant, elle présente l'inconvénient que la fraise, comme un tire-bouchon, déplace également le matériau de base (pièce) vers le haut, « tourbillonne » lors du fraisage. le bois ou « enterre » lors du traitement de matériaux en feuilles minces ( par exemple l'étain). En revanche, une fraise avec une hélice gauche pousse vers le bas sur le matériau et lors du fraisage de matériaux fibreux tels que le bois ou le carton, vous obtenez un bord supérieur plus lisse (les fibres ne sont pas soulevées mais « pressées » dans le matériau de base). Mais ici, le facteur négatif est la difficulté d'enlever les copeaux.
Note:
Dans les cas standards, utilisez une fraise à droite.
Les couteaux à gauche sont avantageux pour les coupes peu profondes matériaux fins, où le danger d'« enterrer » et de faire remonter la pièce avec le filetage à droite est grand. Cependant, plus le matériau que vous utilisez est dur, plus tôt vous pourrez abandonner la fraise hélicoïdale gauche.
A. Coupe à droite (forme normale) :
Amenez les copeaux vers le haut. Le couteau a tendance à « creuser » et à soulever le matériau de base.
"effet tire-bouchon"
B. Hélice gauche (forme spéciale) : guide les copeaux vers le bas lors de l'usinage depuis l'extrémité, ou utilisée lors du travail dans une cavité déjà fraisée. Le cutter appuie sur le matériau de base (à l'opposé de « l'effet tire-bouchon »).
Ne convient pas au fraisage profond.
Type de cutter : 1 ou 2 lames ?
Il existe un nombre infini de couteaux, mais pour l'essentiel, nous faisons une distinction entre les tranchants et les émoussés. Plus la lame est tranchante, plus la pointe s'use rapidement.Règle générale: Plus la résistance du matériau est élevée, plus l'affûtage de la lame doit être plat. Cet affûtage convient aux métaux durs (par exemple le laiton). Affûtage plus net en queue de poisson pour les plastiques, le bois et l'aluminium souple. Les lames sont les pièces d'usure du coupeur. Dans les fraises à plusieurs lames, la charge est répartie et la durabilité augmente. Ces fraises fonctionnent plus rapidement et vibrent moins dans les matériaux difficiles (par exemple l'acier inoxydable). Plusieurs lames – dans les mêmes conditions de fraisage – produisent des copeaux plus fins, ce qui donne une surface plus lisse.
Le choix du type de fraise « idéal » dépend toujours du matériau à traiter :
Lors du fraisage de matériaux « mous » : Les plastiques souples (PVC, plexiglas, mousse de polystyrène), les matériaux en bois (bois, panneaux de fibres, contreplaqué, panneaux de particules), les qualités d'aluminium souples et les sandwichs (aluminium/plastique) bénéficient de couteaux tranchants à 1 cannelure. Car ici le problème d'un émoussement plus rapide est préférable au risque de colmatage et de casse de la fraise.
Pour les plastiques durs les modèles pointus à 2 voies avec un profil en queue de poisson conviennent.
Lors de l'usinage de métaux plus durs comme le laiton, nous pouvons recommander des fraises à 2 cannelures avec une émouture plate.
Lors du fraisage d'acier de construction extrêmement rigide ou en acier de très haute qualité, utilisez des fraises à trois ou quatre entrées.
Coupeur simple en section transversale
Un couteau laisse un grand espace ouvert
pour enlever les copeaux
Fraise à trois cannelures en coupe transversale
Trois lames réduisent considérablement l'espace
pour enlever les copeaux
Différences entre un tailleur et un graveur
De nombreuses personnes utilisent les termes « Cutter » et « Graveur » de manière interchangeable. Cependant, nous parlons de deux outils différents.
Un graveur est un outil simple, divisant un cylindre en deux, suivi d'un meulage arrière.
La forme peut varier ; les plus courants sont triangulaires. Contrairement aux fraises, elles ne disposent pas de goulotte en spirale pour évacuer les copeaux.
Matériau de coupe : HSS ou carbure ?
Dans la technologie publicitaire, les fraises en carbure sont principalement utilisées.
Le carbure (HM) est un produit artificiel coûteux qui est aggloméré à partir de poudres fines (par exemple Wolfram-Carbid). Pendant le processus d'agglomération, la forme de la fraise est immédiatement créée et ne change pas par la suite (elle est seulement affûtée). Le carbure est extrêmement dur et résistant à l’usure, mais il est sensible aux vibrations et aux chocs. Lors de l'utilisation de fraises HM, il est important de disposer d'une machine stable, éventuellement plus lourde et massive, d'une broche avec une rotation précise et de pinces de serrage de haute qualité. Le matériau à fraiser doit être fixé de manière rigide et immobile sur la machine.
L'acier rapide (HSS) est principalement utilisé là où le carbure est trop sensible : lors du fraisage de tôles d'acier inoxydable, sur des machines bancales ou dans les cas où la rigidité de serrage n'est pas suffisamment assurée. Le HSS s'use beaucoup plus rapidement, mais il y a moins de risque de défaillance prématurée en raison de sa viscosité.
La durée de vie d'une fraise HSS revêtue est considérablement augmentée. Par exemple, le nitrure de titane (TiN) multiplie par six la durée de vie.
Titan-Nitrid est nettement plus rigide que le HSS et également plus rigide que le HM. Grâce au revêtement Titan-Nitrid, les outils HM durent également plus longtemps, bien que la différence de dureté soit négligeable.
La couverture a un effet plus significatif sur le nombre de tours et l'avance. Il peut être augmenté et ainsi le temps de traitement peut être raccourci. Lors du fraisage de l'aluminium, TiN empêche la redoutable cuisson de l'aluminium dans la fraise. Le revêtement agit comme le Téflon dans une poêle (les chips glissent)
Vitesse et alimentation optimale
Les paramètres les plus importants lors du fraisage sont le nombre de tours et l'avance. Les données du tableau coïncident avec la plupart des recommandations des fabricants de couteaux. (En cas de doute, demandez à votre fournisseur quels modes il recommande pour son produit.)Tout d’abord, prenez la vitesse de coupe recommandée pour le matériau à traiter et appliquez-la dans la formule pour calculer le nombre de tours.
Si une machine peu rigide est utilisée, le nombre de tours est déterminé dans la région supérieure et l'avance dans la région inférieure. Si le nombre de tours est connu, l'avance est alors calculée à l'aide de la formule.
Il est fondamentalement considéré : plus la vitesse de coupe est élevée (vc = p * d * n), plus la surface sera lisse. Cependant, l'émoussement de la fraise augmente également avec l'augmentation de la vitesse de coupe.
Procédure de calcul :
1. Nombre de tours n:
Sélectionnez la vitesse de coupe vc de la table. (Si la vitesse de coupe du matériau varie considérablement, vérifiez auprès des ouvrages de référence).
Sur la base des données, calculez la vitesse de la broche
N = (vc *1000) / (3,14 * d)
F = n * fz * z
fz = avance par dent
z = nombre de pales
Exemple:
Vous souhaitez fraiser de l'aluminium dur avec une fraise à 2 cannelures de 3 mm de diamètre. Dans le tableau, vous trouvez : vc = 100... 200 m/min. A partir de là, vous calculez :Max. nombre de tours : n = (200 * 1000) / (3,14 * 3) = 200 000 / 9,42 = 21.230 tours/min
Alimentation correspondante : f = 21230 * 0,04 * 2 = 1698 mm/minDes avances élevées, notamment dans le cas des métaux, nécessitent une machine stable et silencieuse. De plus, la profondeur de la rainure ne doit pas être trop grande (environ 1 * d 1).
Pour les machines moins stables ou avec une profondeur de fraisage accrue, le mode est calculé comme suit :Max. vitesse:
n = (200 * 1 000) / (3,14 * 3) = 200 000 / 9,42 = 21.230 tours/min(comme ci-dessus)
Le minimum nombre de tours : n = (100 * 1000) / (3,14 * 3) = 100 000 / 9,42 = 10,615 tours/min
Alimentation correspondante (minimum) : f = 10615 * 0,04 * 2 = 849 mm/minVous combinez n=21230 U/min et f=849 mm/min.
Contre-mouvement et mouvement synchrone
Comment apparaissent les différentes arêtes de coupe :La lame pénètre dans le matériau par le côté au vent. Dans la zone de contre-mouvement, la fraise se déplace contre le matériau. L'épaisseur des copeaux sera fonction de l'alimentation en matériau de plus en plus grande. Dans la zone de synchronisme, la fraise se déplace avec le matériau, l'épaisseur des copeaux diminue avant de sortir. La zone ombrée montre l'épaisseur relative des copeaux à chaque position de copeau par tour. La lame en contre-mouvement « prend » constamment de la matière, tandis qu'en mouvement synchrone, seule une petite quantité est absorbée juste avant que la lame ne s'envole. C’est pourquoi le dernier morceau semble souvent « éclater ». C’est la raison pour laquelle le côté opposé du mouvement est toujours plus fluide que le côté synchronicité.
Quel cutter pour quelle matière | 1-début | 2-départ | 3 voies | |||
rugueux | purement | rugueux | purement | rugueux | purement | |
Matériaux en bois | ||||||
Bois tendre (pin) | ++ | 0 | +(+) | 0 | 0 | - |
Massif (chêne, hêtre), contreplaqué, MDF | +(+) | 0 | ++ | 0 | +(-) | - |
Plastiques | ||||||
PVC, polystyrène, téflon, mousse | ++ | + | + | 0 | - | -- |
Duroplast, matériaux avec bakélite (aggloméré) | + | + | ++ | + | + | - |
Plexiglas coulé | ++ | + | +(+) | - | 0 | - |
Les métaux | ||||||
Aluminium souple (Alucobond) | ++ | + | + | 0 | - | -- |
Aluminium rigide (Floxal) | 0 | + | + | ++ | 0 | + |
Laiton, bronze, alliages de cuivre | -- | - | 0 | +(-) | + | ++ |
Acier de construction | -- | -- | - | + | - | ++ |
Acier de haute qualité | -- | -- | -- | - | -- | + |
++ Très bien + Bien 0 Satisfaisant |
- Mal -- Ne convient pas |
Lors du traitement des aciers durs, 4 lames ou plus sont utilisées.
Utilisation partielle ou totale de ce matériel uniquement par accord, et avec référence obligatoire à la source
Dans les entreprises qui ont des divisions engagées dans le traitement de surface des pièces, sur la base de documents réglementaires des cartes spéciales sont établies qui guident l'opérateur dans la fabrication d'une pièce particulière. Bien que dans certains cas (par exemple, de nouveaux équipements, outils), l'opérateur de fraisage doive déterminer de manière indépendante les nuances des opérations technologiques. Si une machine de faible puissance est utilisée à la maison, d'autant plus qu'en règle générale, il n'y a pas de conseils officiels à portée de main.
Cet article aidera non seulement à comprendre la base de calcul du mode de coupe lors du fraisage et à choisir l'outil approprié, mais donnera également recommandations pratiques, qui sont suffisants pour le traitement des pièces au niveau domestique.
À ceux qui dans une plus grande mesure est associé aux métaux, pour une connaissance plus détaillée des nuances du fraisage, vous devez vous référer au manuel « Machines à couper les métaux » - 2003, Cherpakov B.I., Alperovich T.A. La procédure de calcul des conditions de coupe est également bien décrite dans divers manuels. Par exemple, dans recommandations méthodologiquesà partir de 2000 (MSAU – Kolokatov A.M., Bagramov L.G.).
La particularité du fraisage est que les arêtes de coupe n'entrent en contact direct avec le matériau que périodiquement. Il en résulte des vibrations, des chocs et une usure accrue des couteaux. Le mode le plus efficace est considéré comme celui dans lequel les paramètres suivants sont combinés de manière optimale : profondeur, avance et vitesse de coupe sans compromettre la précision et la qualité du traitement. C'est ce qui permet de réduire considérablement le coût d'une opération technologique et d'augmenter la productivité.
Il est impossible de prévoir littéralement toutes les nuances du fraisage. Les pièces à usiner diffèrent par leur structure, leurs dimensions et leur forme ; outils de coupe - par leur géométrie, leur conception, la présence/absence d'une couche protectrice, etc. Tout ce qui est indiqué ci-dessous concernant les modes de coupe doit être considéré uniquement à titre indicatif. Pour clarifier des paramètres de fraisage spécifiques, vous devez utiliser des tableaux spéciaux et des données de référence.
Sélection d'outils
Cela concerne principalement son diamètre. Quelle est la particularité de la sélection d'un cutter () en fonction de ce paramètre ?
- L'augmentation du diamètre entraîne automatiquement une augmentation du coût de l'outil.
- L'interdépendance des deux indicateurs - si l'avance augmente, la vitesse de coupe diminue, car elle est limitée par la structure de la pièce (voir ci-dessous).
Le diamètre optimal de la fraise est considéré comme tel que sa valeur correspond à (ou est légèrement supérieure à) la profondeur de coupe requise. Dans certains cas, en un seul passage, vous pouvez sélectionner des copeaux plus épais, mais cela ne s'applique qu'aux matériaux caractérisés par une faible densité. Par exemple, la mousse de polystyrène ou certains types de bois.
Vitesse de coupe
En fonction du matériau échantillon, vous pouvez vous concentrer sur les indicateurs suivants (m/min) :
- bois, thermoplastiques – 300 – 500 ;
- PVC – 100 – 250 ;
- acier inoxydable – 45 – 95 ;
- bronzes – 90 – 150 ;
- laiton – 130 – 320 ;
- bakélite – 40 – 110 ;
- aluminium et ses alliages – 200 – 420.
Vitesse de rotation du coupeur
La formule la plus simple ressemble à ceci :
N (nombre de tours) = 1000 Vc (vitesse de coupe souhaitée) / π D (diamètre de la fraise).
Pour des raisons de sécurité, vous ne devez pas entraîner la broche à vitesse maximale. Cela signifie que ce n'est qu'à cause de cela que la vitesse de coupe diminuera d'environ 10 à 15 %. Cette « perte » peut être partiellement compensée en installant une fraise de plus grand diamètre. Cela augmente légèrement la vitesse. Si vous n’en avez pas sous la main, vous devrez décider si vous souhaitez dépenser de l’argent pour nouvel outil ou se contenter des capacités de la fraiseuse. Encore une fois, tout cela ne peut être vérifié que par la pratique travaillant sur un équipement spécifique, mais sens général Les recommandations sont claires.
Manches
Vous devez prêter une attention particulière à ce paramètre de fraisage !
La durabilité de la fraise et la qualité du traitement de la pièce dépendent de l'épaisseur de la couche enlevée en un seul passage, c'est-à-dire à chaque tour de broche. Dans ce cas, on parle d'une avance pour 1 (2,3) dents, selon le type d'outil (fraise à un, deux ou trois pas).
Les valeurs d'avance recommandées par dent sont spécifiées par le fabricant de l'outil. Le meunier rencontre des difficultés à ce stade du régime de coupe s'il travaille avec des fraises « fabriquées en Chine » ou d'origine douteuse (inconnue). Dans la plupart des cas, vous pouvez vous concentrer sur la plage d'avance (mm) 0,1 - 0,25. Ce mode convient à presque tous les matériaux courants soumis au fraisage. Au cours du processus de découpe, il deviendra clair s'il suffit d'en « ajouter » un peu (mais pas plus tôt qu'après le 1er passage). Mais vous ne devriez pas essayer moins de 0,1, sauf lorsque vous travaillez en bijouterie avec des micro-moulins.
Le fraisage doit commencer avec une avance minimale de 0,1. Au cours du processus, il apparaîtra clairement à quel point le matériau traité est malléable devant une fraise spécifique. Cela éliminera la possibilité de casser le tranchant (dent) et permettra de faire un « diagnostic » précis des capacités de la machine et de l'outil, surtout s'il s'agit d'un équipement « étranger ».
- Le dépassement de la valeur d'avance optimale entraîne une augmentation de la température dans la zone de travail, la formation de copeaux épais et une rupture rapide de la fraise. Pour les outils d'un diamètre supérieur à 3 mm, vous devez commencer par 0,15, pas plus
- Si la vitesse de fraisage d'une pièce ne peut pas être augmentée grâce à une utilisation optimale des capacités de l'équipement, vous pouvez essayer d'installer une fraise à deux dents.
- Lors du choix d'un outil, vous devez tenir compte du fait que l'augmentation de la longueur de la partie coupante entraîne une diminution de l'avance et une augmentation des vibrations.
- Vous ne devez pas vous efforcer d'augmenter la vitesse de traitement en remplaçant la fraise par une fraise similaire, mais avec plus de dents. Les copeaux d'un tel outil sont moins bien éliminés, et entraînent donc souvent une forte diminution de la qualité du fraisage. Dans certains cas, lorsque les rainures sont complètement obstruées, la fraise commence à tourner au ralenti. Un tel remplacement n’a aucun sens.
Conclusion
Un fraisage de haute qualité ne peut être obtenu que par l'expérience. Machine à béton + outil + expérience pratique, compétences. Par conséquent, vous ne devez pas faire aveuglément confiance, même aux données tabulaires. Par exemple, ils ne tiennent pas compte du degré d’usure de la fraise avec laquelle on va travailler. Il n'y a pas lieu d'avoir peur d'expérimenter, mais vous devez toujours commencer par les valeurs minimales des paramètres. Lorsque le maître « sent » la machine, la fraise et le matériau à traiter, il déterminera lui-même dans quel mode il doit travailler.
Pourquoi la fraise s'émousse-t-elle rapidement ? Qu'est-ce qui provoque la carbonisation du matériau traité (panneaux de particules, MDF ou bois) après le traitement avec une fraise ? Pourquoi le cutter brûle-t-il ? Comment éviter que les résines n'adhèrent aux arêtes de coupe d'un cutter ? Il n'y a qu'une seule réponse aux questions ci-dessus : la vitesse (fréquence) de rotation de la fraise est mal sélectionnée.
Les équipements de fraisage modernes destinés au traitement des panneaux de particules stratifiés ou des panneaux MDF sont équipés de moteurs qui permettent d'atteindre des vitesses de broche supérieures à 20 000 tr/min. D'une part, cela affecte la productivité de l'équipement, puisque la vitesse de déplacement de l'outil ou l'avance de la pièce augmente. D'autre part, la qualité du traitement augmente : le risque de soulèvement des poils sur le MDF, d'éraflures sur le bois et d'écaillage sur les panneaux de particules stratifiés est réduit.
Par habitude, par ignorance ou simplement par paresse, pour ne pas vous déranger la tête avec toutes sortes d'instructions d'utilisation, modes de traitement et autres subtilités, la vitesse de rotation de la fraise est réglée au niveau maximum, auquel tout les matériaux sont traités à l'aide de tous les couteaux disponibles. C'est là que ça se trouve raison principale tous les ennuis
Le fait est qu'à une vitesse (fréquence) élevée de rotation de la fraise et une faible vitesse d'avance de la pièce, le tranchant de la fraise la plupart fonctionne au ralenti pendant un certain temps et, au lieu de couper le prochain copeau du matériau en cours de traitement, il le frotte inutilement. Tout le monde sait ce qui se produit en raison du frottement – de l'échauffement. De plus, plus la vitesse de rotation de la fraise est élevée, plus le frottement est intense et plus la fraise s’échauffe.
Il semblerait, qu'est-ce qu'il y a de spécial ici ? Eh bien, ça chauffe. Si vous le prenez dans votre paume, votre main durera. Qu'arrivera-t-il au métal ?! Mais reste…
Pourquoi le cutter brûle-t-il et devient-il rapidement émoussé ?
La chaleur résultant du frottement des couteaux contre le matériau est progressivement répartie uniformément dans tout son corps. Par conséquent, lors d'un fonctionnement à court terme, le chauffage n'est pratiquement pas ressenti. Cependant, lors du traitement des matériaux, c'est au niveau des arêtes de coupe que la température atteint des niveaux maximaux. Et plus la vitesse de rotation de la fraise est élevée, plus le frottement et l'échauffement des bords sont forts.
Ceci est particulièrement visible sur les fraises de grand diamètre. Ici vitesse linéaire le mouvement de la partie extérieure du tranchant par rapport au matériau est beaucoup plus important. En conséquence, les bords de la fraise chauffent et, après refroidissement, s'assombrissent avec une teinte bleuâtre, ce qui est un signe certain que le métal a été chauffé au point où il commence à changer ses propriétés. En termes scientifiques, le composant carbone du métal brûle, ce qui lui confère des propriétés de rigidité. Si vous vous souvenez à quel point un ongle ordinaire devient mou et souple lorsqu'il a été dans les charbons ardents d'un poêle ou d'un feu, il est alors facile d'imaginer quelles nouvelles propriétés un coupeur acquerra à la suite d'une surchauffe.
Il convient d'ajouter que lors de l'affûtage d'une fraise, la vitesse de rotation de la meule ou du disque et le degré de pression de l'outil affectent directement l'échauffement des arêtes affûtées. Si vous n'utilisez pas de liquide de refroidissement, tout carbure métallique se transformera en un morceau de fer ordinaire qui peut être déformé après charge légère. C'est d'ailleurs pourquoi la durée de vie des fraises, forets et scies après affûtage est considérablement réduite.
Pourquoi le matériau brûle-t-il ?
Tout est ici très clair : du fait du frottement de la fraise contre le matériau, une température élevée se forme, sous l'influence de laquelle le bois commence à brûler. Pour éviter ce phénomène, il est nécessaire de réduire la vitesse (fréquence) de rotation de la fraise et d'augmenter l'avance de la pièce. Mais ces actions doivent être effectuées à condition que la fraise ait conservé son affûtage. DANS sinon, la charge sur celui-ci ou sur le groupe motopropulseur augmentera considérablement, ce qui peut entraîner leur panne.
Résine qui colle au cutter
De nombreux bois contiennent des résines. Dans la fabrication de panneaux en bois tels que les panneaux de particules et le MDF, des résines de formaldéhyde sont également utilisées. Lors du traitement mécanique de ces matériaux, chauffés par friction, des particules de résines bouillonnent, tombent sur les dents de l'outil de coupe et, avec la poussière, s'y collent. Habituellement, cela ne pose pas de problèmes importants si le mode d'alimentation de la pièce et la vitesse de coupe de l'outil sont sélectionnés correctement. Sinon, lorsqu'un des paramètres est mal calculé, que la vitesse de rotation de la fraise est trop élevée et que le traitement est effectué à basse vitesse, une couche de résine sombre apparaît sur les fraises de l'outil. De plus, plus cet écart est fort, plus il se forme rapidement. Dans le même temps, la qualité du traitement diminue, des copeaux apparaissent sur les surfaces stratifiées, le bois commence à brûler, l'outil subit une contrainte supplémentaire, surchauffe rapidement et tombe en panne. Par conséquent, le choix de la vitesse de rotation de la fraise et de la vitesse d’alimentation du matériau est si important.
En plus du calcul correct du mode de traitement du matériau, il est nécessaire de prêter attention à l'entretien de l'outil de coupe, c'est-à-dire de nettoyer rapidement le revêtement de résine obtenu ou de le laver à l'eau tiède ordinaire.
Calcul de la vitesse (fréquence) de rotation de la fraise
Pour effectuer un calcul correct de la vitesse de rotation de la fraise et de la vitesse de son mouvement, il est nécessaire de prendre en compte de nombreux facteurs, notamment les propriétés physiques et mécaniques du matériau et de l'outil, la profondeur et la largeur du traitement, etc.
En revanche, les matériaux tels que le MDF et les panneaux de particules sont beaucoup plus faciles à traiter que divers métaux, par exemple. Par conséquent, nous pouvons nous baser uniquement sur l'indicateur de la qualité du traitement, c'est-à-dire la présence de rugosité, de crêtes, d'éclats et de bavures sur la surface traitée.
Pour un traitement de plus ou moins haute qualité des panneaux de particules stratifiés, il est nécessaire que la vitesse d'avance par dent de coupe (ou, en termes simples, l'épaisseur des copeaux sortant sous la fraise) soit de 0,05 à 0,15 mm. Ainsi, une fraise à deux coupes conventionnelle doit couper 0,1 à 0,3 mm par tour et 1 500 à 4 500 mm tous les 15 000 tours. C'est-à-dire que la vitesse d'alimentation du matériau vers le coupeur, à 15 000 tr/min, doit être de 1,5 à 4,5 m/min, ou de 25 à 75 mm/s.
Si un usinage est nécessaire avec de faibles avances, par ex. routeur manuel, le calcul de la vitesse de rotation de la fraise peut alors être effectué sur la base de la vitesse de déplacement de la fraise, en effectuant les calculs dans l'ordre inverse. Disons que le matériau est traité à une vitesse de 10 mm/s ou 600 mm/min. Avec une avance par dent égale à 0,1 mm et en travaillant avec une fraise à double coupe, la vitesse de rotation requise de la fraise sera de 600/(0,1× 2)=3000 tr/min.
Précautions de sécurité lors du travail avec des couteaux
En règle générale, les fabricants d'équipements et d'outils de fraisage attachent des instructions de sécurité à leurs produits et indiquent les modes de fonctionnement recommandés pour les fraises. Le tableau ci-dessous présente les paramètres sûrs pour la vitesse de rotation de la fraise en fonction du diamètre.
Diamètre de coupe, mm |
Vitesse de rotation maximale de la fraise, tr/min |
Jusqu'à 25 |
24000 |
26 – 50 |
18000 |
51 – 63 |
16000 |
64 – 75 |
14000 |
76 – 87 |
12000 |
SÉLECTION DU MODE DE COUPE LORS DU FRAISAGE
§ 78. CONDITIONS DETERMINANT LE CHOIX DU MODE DE COUPE
Le concept du mode de coupe le plus avantageux
Ce mode de coupe doit être considéré comme le plus avantageux lorsque l'on travaille sur fraiseuse, dans lequel la vitesse de coupe, l'avance et la profondeur de la couche coupée sont combinées avec le plus de succès, en fournissant dans ces conditions spécifiques (c'est-à-dire en tenant compte de la meilleure utilisation des propriétés de coupe de l'outil, des capacités de vitesse et de puissance de la machine) la productivité du travail la plus élevée et le coût de l'opération le plus bas tout en respectant les conditions techniques spécifiées concernant la précision et la pureté du traitement.
Institut de recherche scientifique sur le travail du Comité d'État du Conseil des ministres de l'URSS pour le travail et salaires développé avec la participation d'éminents scientifiques nationaux, en tenant compte application pratique dans les conditions de production, modes de coupe lors du fraisage avec des outils en acier rapide et en alliages durs. Ils peuvent servir de données d'entrée lors de l'attribution de vitesses de coupe et d'avances minutes.
Ces normes sont disponibles dans chaque usine et servent de guide pour le développement processus technologique et l'élaboration de diagrammes opérationnels comme celui présenté aux pages 204-205. Cependant, les vitesses de coupe et les avances minimes qui y sont indiquées ne sont pas maximales et peuvent dans certains cas être dépassées par les fraiseurs s'ils utilisent des outils plus productifs ou travaillent sur des machines plus puissantes et rigides.
D'autre part, les fraiseurs jeunes, c'est-à-dire débutants et sans expérience suffisante, ne peuvent pas toujours travailler dans des conditions de coupe extrêmes. C'est pourquoi des conditions de coupe moins sévères leur sont proposées dans le « Manuel du jeune fraiseur », à partir duquel il est nécessaire, au fur et à mesure de la formation avancée, passez à des formations plus difficiles.
Afin d'introduire vous-même de nouveaux modes, vous devez connaître l'ordre et la séquence d'établissement des modes de fraisage.
Matériau de la fraise
Le facteur décisif déterminant le niveau de mode de coupe est le matériau de la partie coupante de la fraise. Comme mentionné ci-dessus, l'utilisation de fraises avec plaquettes en carbure permet de travailler à des vitesses de coupe et des avances élevées par rapport aux fraises en acier rapide ; Comme nous le verrons plus loin, les fraises en carbure permettent d'augmenter la productivité de deux à trois fois par rapport aux fraises à grande vitesse. Par conséquent, il est conseillé d’utiliser des fraises en carbure pour presque tous les types de fraisage ; un obstacle à leur utilisation peut être une puissance insuffisante de l'équipement ou les propriétés spécifiques du matériau de la pièce à usiner.
Cependant, dans un certain nombre de cas, l'utilisation d'aciers au carbone, d'aciers à outils alliés et d'aciers rapides pour la partie coupante des fraises est rationnelle, surtout lorsque la propreté de la surface usinée et la précision de la surface résultante de la pièce sont plus importantes. que la vitesse du travail.
Paramètres géométriques de la partie coupante
Un facteur tout aussi important influençant le choix des modes de coupe sont les paramètres géométriques de la partie coupante de la fraise (angles de coupe, dimensions et forme de la dent), souvent appelés géométrie de la fraise. Auparavant, au § 7, l'importance et l'influence de chacun des éléments de la géométrie des dents de la fraise au cours du processus de coupe ont été examinées ; Nous examinerons ici les paramètres géométriques recommandés pour la partie coupante des fraises en acier rapide R18 et avec plaquettes en carbure.
Dans le tableau 35 et 36 montrent les valeurs recommandées des paramètres géométriques des fraises cylindriques, d'extrémité, de disque, de coupe, d'extrémité et de forme en acier rapide.
Tableau 35
Paramètres géométriques de la partie coupante des fraises en acier rapide P18
I. Coins avant

II. Coins arrières

III. Angles de bord d'attaque et de transition

Remarques 1. Pour les fraises cylindriques avec un angle d'inclinaison des dents supérieur à 30°, l'angle de coupe γ lors du traitement de l'acier σ b est inférieur à 60. kg/mm 2 est pris égal à 15°.
2. Pour les fraises profilées avec un angle de coupe supérieur à 0°, une correction du contour est nécessaire lors du traitement de profils précis.
3. Lors du traitement d'aciers résistants à la chaleur avec des fraises en bout, prenez les valeurs supérieures des angles de coupe, et avec des fraises en bout et cylindriques, prenez les valeurs inférieures et moyennes.
4. Lors de l'affûtage, laissez une bande de ponçage circulaire d'une largeur ne dépassant pas 0,1 sur la surface arrière des couteaux. mm. Les dents des fraises à fente (fendue) et coupantes (scie circulaire) sont affûtées sans laisser de bande.

Dans le tableau 37 - 40 montrent les valeurs recommandées des angles avant et arrière, les angles principaux, auxiliaires et de transition dans le plan, les angles d'inclinaison du tranchant et des rainures hélicoïdales, le rayon de face au sommet, fraisage cylindrique, d'extrémité et de disque fraises avec plaquettes en carbure.
Les fraises utilisées pour traiter la plupart des pièces sont généralement fournies par des usines d'outils avec des paramètres géométriques correspondant à GOST, et il est presque impossible pour le fraiseur, contrairement au tourneur et à la raboteuse, de modifier les angles de coupe des fraises par affûtage. En conséquence, ceux donnés dans le tableau. 35 à 40 paramètres géométriques de la partie coupante des fraises aideront l'opérateur de fraisage à sélectionner correctement la fraise appropriée pour un traitement donné parmi les fraises standards disponibles dans le magasin d'outils de l'atelier de formation et de production. Cependant, l'objectif principal de ces tableaux est de fournir des recommandations dans le cas où l'opérateur de fraiseuse souhaite commander au service outillage des fraises standards ou spéciales avec des paramètres géométriques optimaux pour un usinage donné.
Tableau 37
Paramètres géométriques de la partie coupante des fraises en bout avec plaquettes en carbure

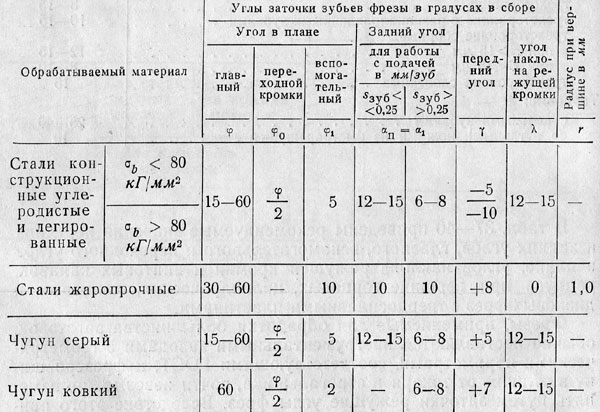
Note: Lors de l'usinage sur des machines rigides, pour des passes d'ébauche avec de petites profondeurs de coupe ou des passes de finition avec de faibles exigences en matière de propreté et de précision de la surface usinée, il convient d'utiliser de petits angles d'entrée φ = 15 - 30°.
Tableau 38
Paramètres géométriques de la partie coupante des fraises cylindriques avec inserts à vis en alliage dur


Note: Sur la surface arrière de la dent le long du tranchant, un ruban d'une largeur ne dépassant pas 0,1 est autorisé mm.
Tableau 39
Paramètres géométriques de la partie coupante des fraises en bout avec plaquettes en carbure lors du traitement des aciers structurels au carbone et alliés


* Avec une faible rigidité du système machine - montage - outil - pièce et avec de grandes sections de copeaux ( DANS plus D; t plus de 0,5 D), ainsi que lorsque vous travaillez avec basses vitesses coupe à une vitesse de broche insuffisante ( v moins que 100 m/min) l'angle frontal γ est affecté positif + de 0 à +8°.
** Valeurs plus élevées pour les aciers doux, valeurs plus faibles pour les aciers durs.
Largeur et profondeur de fraisage
Largeur de fraisage spécifié dans le dessin de la pièce. Dans le cas du traitement de plusieurs pièces serrées en parallèle dans un seul dispositif de serrage, la largeur de fraisage est égale à la largeur de toutes les pièces. Dans le cas d'un traitement avec des jeux de fraises, la largeur de fraisage est égale à la largeur totale de toutes les surfaces de contact.
Profondeur de fraisage(profondeur de coupe, épaisseur de la couche coupée) est donnée comme la distance entre les surfaces usinées et usinées. Pour réduire le temps de traitement, il est recommandé d'effectuer le fraisage en une seule passe. Avec des exigences accrues en matière de précision et de propreté de la surface usinée, le fraisage s'effectue en deux transitions : l'ébauche et la finition. Dans certains cas, lors de l'élimination de surépaisseurs importantes ou lors du fraisage sur des machines de puissance insuffisante, un usinage en deux passes d'ébauche est possible.
Tableau 40
Paramètres géométriques de la partie coupante des fraises à disques avec plaquettes en carbure


Lors du fraisage de pièces forgées en acier, de pièces moulées en acier et en fonte recouvertes de calamine, de croûte de fonderie ou contaminées par du sable de fonderie, la profondeur de fraisage doit être supérieure à l'épaisseur de la couche contaminée afin que les dents de coupe ne laissent pas sur la surface usinée des ébauches , car le glissement sur la croûte a un effet négatif sur le couteau, accélérant l'usure du tranchant.
Pour les cas de fraisage les plus courants, il est recommandé d'effectuer une ébauche sur de l'acier avec une profondeur de coupe de 3 à 5. mm, et pour l'acier et coulée de fer- avec profondeur de coupe 5-7 mm. Pour le fraisage de finition, prenez une profondeur de coupe de 0,5 à 1,0 mm.
Diamètre de coupe
Le diamètre de la fraise est choisi principalement en fonction de la largeur du fraisage DANS et profondeurs de coupe t. Dans le tableau 41 montre les données pour le choix des fraises cylindriques, tableau. 42 - fraises en bout et en tableau. 43 - coupe-disques.

* Utilisez des couteaux composites préfabriqués conformément à GOST 1979-52.


Considérons l'influence du diamètre de la fraise sur les performances de fraisage.
Le diamètre de la fraise cylindrique affecte l'épaisseur de la coupe : plus le diamètre de la fraise est grand D plus la coupe est fine ; avec le même flux s profondeur de dent et de fraisage t.
En figue. 327 montre la coupe obtenue à la même profondeur de fraisage t et soumission s dent, mais avec des diamètres de coupe différents. La coupe obtenue avec un diamètre de coupe plus grand (Fig. 327, a) a une épaisseur plus petite que la coupe avec un diamètre plus petit ; diamètre de la fraise (Fig. 327, b).

Puisque la pression spécifique augmente avec la diminution de l'épaisseur de la couche coupée UN Naib (voir tableau 38), il est plus rentable de travailler avec des sections plus épaisses, c'est-à-dire, toutes choses égales par ailleurs, avec un diamètre de coupe plus petit.
Le diamètre de la fraise affecte la distance que la fraise doit parcourir pour un passage.
En figue. 328 montre le chemin que le coupeur doit parcourir lors du traitement d'une partie de longueur L; En figue. 329 - le chemin que la fraise à surfacer doit parcourir lors du fraisage asymétrique d'une pièce de longueur L; En figue. 330 - le chemin qu'un coupe-gâteau doit parcourir lors du fraisage symétrique d'une pièce de longueur L.

Taille d'entrée l(chemin de coupe) :
lorsque vous travaillez avec des fraises cylindriques, à disque, coupantes et façonnées, cela dépend du diamètre de la fraise D profondeurs de fraisage t et s'exprime par la formule
lorsque vous travaillez avec des fraises à surfacer et en bout pour le fraisage asymétrique, cela dépend du diamètre de la fraise D largeur de fraisage DANS et s'exprime par la formule
lorsque vous travaillez avec des fraises à surfacer pour un fraisage symétrique, cela dépend du diamètre de la fraise D largeur de fraisage DANS et s'exprime par la formule
Valeur de surcourse l 1 est sélectionné en fonction du diamètre de la fraise dans 2-5 mm.
Par conséquent, pour réduire la trajectoire de coupe et la surcourse de la fraise, c'est-à-dire pour réduire le régime de ralenti de la machine, il est conseillé de choisir un diamètre de fraise plus petit.
A la fin de l'ouvrage, dans les annexes 2 et 3, des tableaux sont donnés pour les valeurs des courses d'approche et de dépassement des fraises.
Le diamètre de la fraise affecte la valeur couple: plus le diamètre de la fraise est petit, moins il faut transmettre de couple à la broche de la machine.
Ainsi, choisir une fraise de plus petit diamètre semble plus approprié. Cependant, avec une diminution du diamètre de la fraise, il est nécessaire de choisir un mandrin de fraisage plus fin, c'est-à-dire moins rigide, il est donc nécessaire de réduire la charge sur le mandrin, c'est-à-dire de réduire la section transversale de la couche coupée. .
Manches
Nourrir à ébauche dépend du matériau à traiter, du matériau de la partie coupante de la fraise, de la puissance d'entraînement de la machine, de la rigidité du système machine - montage - outil - pièce, des dimensions de traitement et des angles d'affûtage de la fraise.
Nourrir à finition dépend de la classe de propreté de surface indiquée sur le dessin de la pièce.
La principale valeur initiale lors du choix d'une alimentation pour le fraisage grossier est l'alimentation s dent.
Pour fraises à surfacer, avance sélectionnable s La dent a un moyen d'installer la fraise par rapport à la pièce, qui détermine l'angle de rencontre de la dent de coupe avec la pièce et l'épaisseur des copeaux coupés lorsque la dent de coupe entre et sort du contact avec la pièce. Il a été établi que pour une fraise en carbure, les conditions les plus favorables pour tailler une dent dans une pièce sont obtenues lorsque la fraise est positionnée par rapport à la pièce, comme sur la Fig. 324, po, c'est-à-dire lorsque la fraise est déplacée par rapport à la pièce à usiner d'une quantité AVEC = (0,03 - 0,05)D. Ce déplacement de l'axe de la fraise permet d'augmenter l'avance par dent contre l'avance lors du fraisage symétrique (Fig. 324, a) de la fonte et de l'acier d'un facteur de deux ou plus.
Dans le tableau 44 montre les vitesses d'avance recommandées pour le fraisage grossier avec des fraises en carbure pour ces deux cas.

Remarques 1. Les valeurs données des avances d'ébauche sont calculées pour travailler avec des fraises standard. Lorsque vous travaillez avec des fraises non standard avec un nombre de dents accru, les valeurs d'avance doivent être réduites de 15 à 25 %.
2. Pendant la période initiale de fonctionnement de la fraise, jusqu'à ce que l'usure soit égale à 0,2-0,3 mm, la propreté de la surface usinée lors du fraisage fin est réduite d'environ une classe.

Note. Utilisez des avances plus grandes pour des profondeurs de coupe et des largeurs de traitement plus petites, des avances plus petites pour des profondeurs et des largeurs de traitement plus grandes.

Note. Les avances sont données pour le système rigide machine - montage - outil - pièce.
Lors du surfaçage avec des fraises en carbure, l'avance est également affectée par l'angle d'attaque φ. Flux donnés dans le tableau. 44, conçu pour les fraises avec φ = 60 - 45°. Réduire l'angle d'attaque φ à 30° permet d'augmenter l'avance de 1,5 fois, et augmenter l'angle d'attaque φ à 90° nécessite une réduction de l'avance de 30 %.
Avances pour la finition avec des fraises en carbure, indiquées dans le tableau. 44, sont donnés pour un tour de fraise, car les avances par dent sont trop faibles. Les aliments sont donnés en fonction de la classe de propreté de la surface traitée selon GOST 2789-59.
Dans le tableau 45 montre les avances recommandées par dent de fraise pour le fraisage grossier de plans avec cylindre, face et disque fraises à trois faces en acier rapide R18.
Dans le tableau 46 montre les avances pour le fraisage de finition des plans avec des fraises cylindriques en acier rapide P18, et dans le tableau. 47 - pour le fraisage de finition de rabots avec des fraises à trois faces frontales et à disque en acier rapide P18. En raison des faibles vitesses d'avance par dent de fraise obtenues lors du fraisage de finition, dans le tableau. Les figures 46 et 47 montrent les avances par tour de la fraise.
Il convient de garder à l'esprit que vous travaillez avec les flux indiqués dans le tableau. 44-47, en fait une condition indispensable pour la présence d'un faux-rond minimal des dents de la fraise (voir Tableau 50).

Note. Les avances sont données pour un système rigide machine - montage - outil - pièce lors de l'usinage avec des fraises avec un angle d'entrée auxiliaire φ 1 = 2° ; pour les fraises avec φ 1 = 0, les avances peuvent être augmentées de 50 à 80 %.